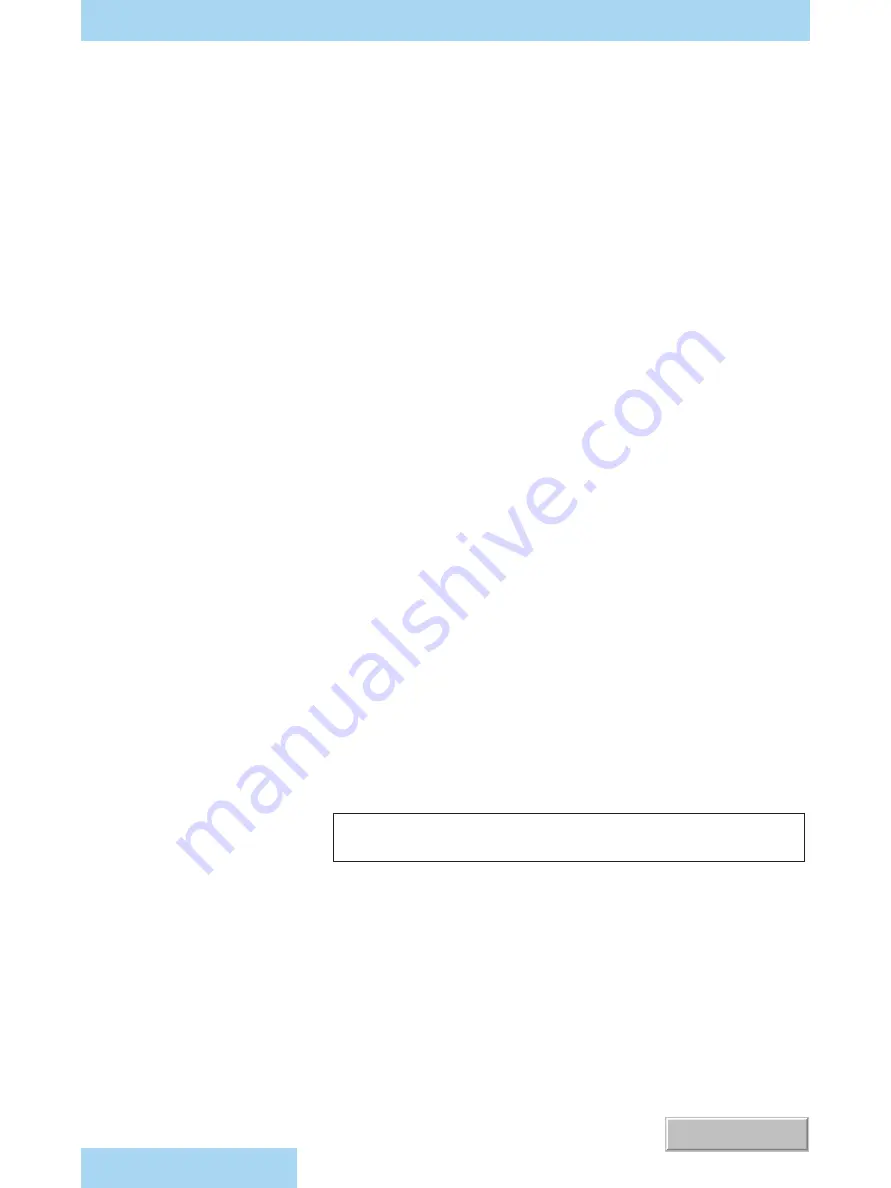
OUTPUT
The output stage of the driver card is a two channel PWM (Pulse Width Modulated)
current source with current feedback for precise control of the current through the coil
regardless of the changes in coil resistance. The two outputs are protected against
short circuits across the coil and short circuits to ground.
PWM frequency
The frequency of the PWM high current driver is factory set to 200Hz (JP2 A-B). JP2
allows the frequency to be lowered to 120Hz by removing the JP2 jumper, or raised to
400Hz by moving JP2 to position B-C.
INPUT
This panel-mounted version of the 900 driver operates with remote signals only; it does
not have a local command poteniometer.
The user has a choice of voltage, current-loop or potentiometer input signals. Voltage
inputs may be ±5V, or ±10V. Current-loop inputs are differential 4-20mA1 or ±0-20mA.
DIP switches on board are for current-loop set-up.
An auxilliary ±10V input is also available. This input provides the user more input
options. With all the input options provided, it is the user’s responsibility to interlock mul-
tiple inputs if driver card is to be controlled by one input at a time.
1
The reverse CMD input can be used to obtain bidirectional operation.
RAMP GENERATOR
Adjustable positive and negative ramping of the output is provided in two ranges of
0.2-6 and .0.8-40 seconds. Ramping, on-off, and ramping ranges are selected by dip
switches on the card.
CONTROLS AND INDICATORS
Key indicators, potentiometer adjustments, switches and test points are located on the
circuit board for monitoring, set-up and calibration purposes. LEDs are provided for indi-
cating the status of the power (internal ±15VDC supplies), the coil that is energized and
the state of the emergency stop function.
Potentiometer adjustments include ±ramps, I
A,B
min and I
A,B
max. Test points
are furnished for measurement of the input, output, ramp and signal ground.
EMERGENCY STOP OPTION
The emergency stop (E-stop) input controls the K1 relay that provides 24VDC to the
output driver stage. Applying logic level +15 to 24VDC to the E-stop enables the driver
card output stage. Removing the E-stop signal will abruptly halt the output current.
(See soft-stop option). In revision level C and up an isolated E-stop signal option is
provided. If an isolated E-stop signal is required, remove the JP4 jumper and connect
the isolated signal common to terminal C24.
SOFT STOP OPTION
The soft stop option is used to set the output current to zero at a rate set by the
ramp circuit. Placing JP3 in the A-B position will enable the soft stop option, position
B-C will disable the soft stop option. If the soft stop is enabled 24VDC and GND
must be connected to the soft stop input for normal operation. Removing 24VDC
from the soft stop input will turn off the output at a rate set by the ramp settings.
REVERSE CMD OPTION
Connecting 24VDC and GND across the reverse CMD input will cause the output
to switch the current from one channel to the other at a rate set by the ramp circuit.
This will allow a unipolar command signal to control the pump on both sides of center.
WARNING: Once the reverse CMD input has been energized loss of this signal
will reverse the driver cards output signal.
RAMP-AT-ZERO OPTION
The ramp-at-zero is an output that indicates when the ramp circuit output is at zero.
The ramp-at-zero output is 15VDC when ramp is at zero and 0VDC when ramp is not
at zero. One application for the ramp-at-zero function is to hold the integrator of the
Jupiter options card, S20-11716, at zero when system command is zero.
CLOSED-LOOP-CONTROL
The driver card operating as a stand alone driver is used primarily for open-loop control.
With the Jupiter options card, S20-11716, the driver card can be used for closed-loop
speed control systems. The options card provides digital encoder and DC tachometer
feedback, horsepower limiting and PI control of the feedback error.
FUNCTIONAL DESCRIPTION
4
Back to Content
Содержание Jupiter 900
Страница 11: ...INSTALLATION DRAWINGS 7 Back to Content...
Страница 12: ...INSTALLATION DRAWINGS 8 SWITCH AND JUMPER SETTINGS Back to Content...
Страница 14: ...INPUT SIGNAL OPTIONS 10 85 264VAC 47 440HZ Back to Content...
Страница 15: ...INPUT SIGNAL OPTIONS 11 85 264VAC 47 440HZ Back to Content...
Страница 16: ...APPLICATION DIAGRAMS 12 Back to Content...
Страница 18: ...APPLICATION DIAGRAMS 14 COMMAND OUT INVERT Back to Content...
Страница 19: ...APPLICATION DIAGRAMS 15 COMMAND OUT INVERT Back to Content...
Страница 20: ...APPLICATION DIAGRAMS 16 COMMAND OUT INVERT Back to Content...
Страница 21: ...APPLICATION DIAGRAMS 17 COMMAND OUT INVERT Back to Content...
Страница 22: ...APPLICATION DIAGRAMS 18 COMMAND OUT INVERT Back to Content...
Страница 23: ...NOTES 19 Back to Content...