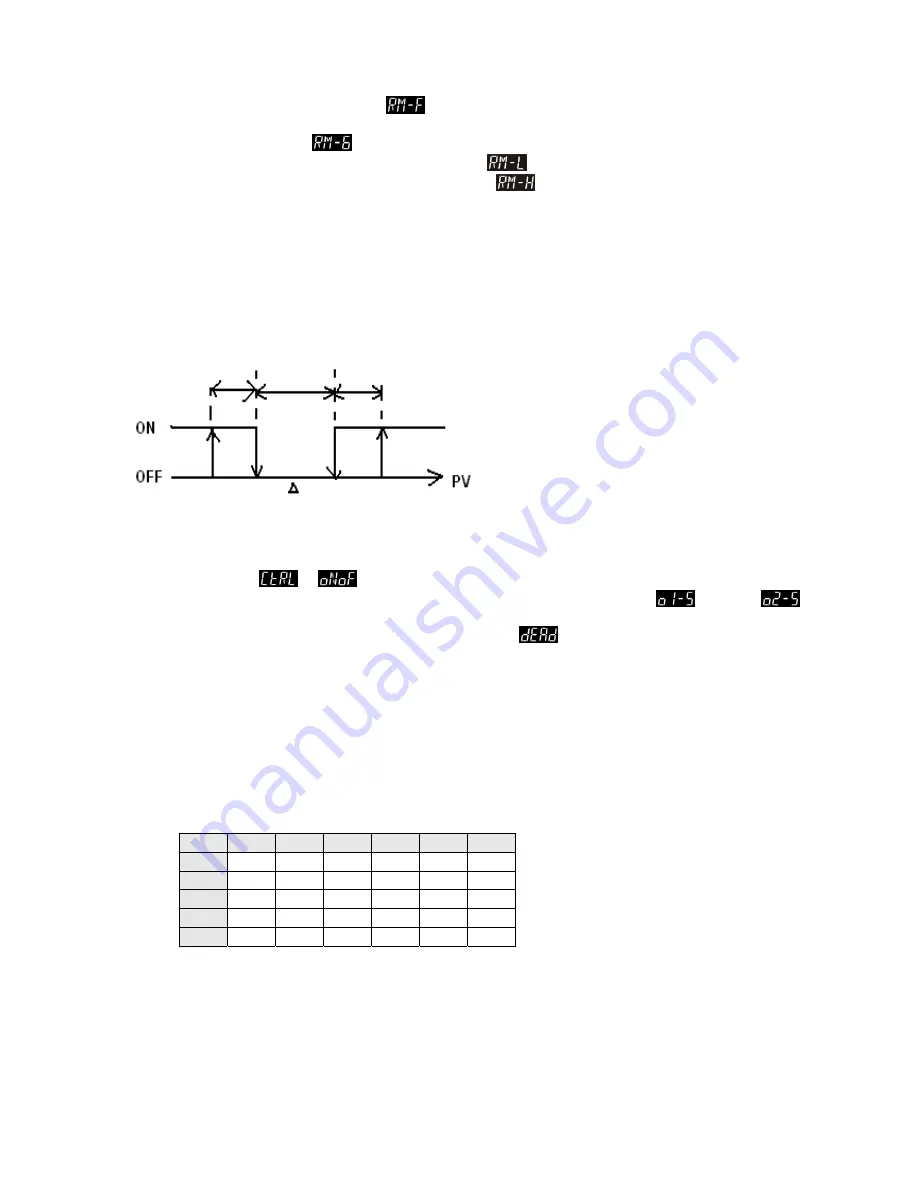
11
¾
Remote compensation adjustment: input corresponding lower limit of analog signal at the Remote end, set Remote
compensation adjustment by parameter
in
【
Regulation Mode
】
¾
Remote gain adjustment: input corresponding upper limit of analog signal at the Remote end, set Remote compensation
adjustment by parameter
in
【
Regulation Mode
】
¾
Remote lower limit: Setting Remote lower limit by parameter
in
【
Regulation Mode
】
¾
Remote higher limit: Setting Remote higher limit by parameter
in
【
Regulation Mode
】
Control Mode Setting
There are 4 control modes; ON-OFF, PID, FUZZY and MANUAL.
z
ON-OFF Mode:
For heating output, the output is off when input is greater than the setting value; output is on when input is smaller
than (setting value – adjustment sensitivity setting value). For cooling output, the output is on when the input is greater than
(setting value + adjustment sensitivity setting value); output is off when input is smaller than the setting value. If one of 2 outputs is
set for heating and the other for cooling, a non-action zone can be set as follows.
¾
Set
parameter
to
in
【
Initial Setting Mode
】
¾
Set adjustment sensitivity: Set adjustment sensitivity by parameter
【
Regulation Mode
】
to
(Output 1),
(output 2)
¾
Setting of DeadBand of both outputs: Set DeadBand by parameter
in
【
Regulation Mode
】
z
PID Mode:
When set for heating or cooling, the program performs PID operation via input temperature and setting temperature,
with the operation result output for the temperature control. A PID parameter and control period must be set for this function; these
parameters can also be generated automatically via auto-tuning (AT).
a
、
A total of six sets of PID parameters are available, one of which can be selected for carrying out PID, and the program may
automatically select a set of PID that is most close to the input value. In order to achieve this, each set of PID parameters has
a reference input setting value which allows the user to set for manual setting or for auto-tuning (AT). E.G., for the six sets of
PID parameters as shown below, SV is reference input setting. Let us select the 4
th
set as the PID running parameter: i.e.,
P=40, I=220, D=55, IOF=30%. If we select AT to find the set closest to the setting value with a setting input of 230, the
program will automatically find the second set as the running parameter for PID operation.
0
1
2
3
4
5
SV 80 160 240 320 400 480
P 120 46 70 60 40 50
I 100 140 180 200 220 240
D 25 35 45 50 55 60
IOF 20 10 30 20 30 21
b
、
Set PID parameters and the control period: in which PID parameters can be adjusted manually according to system
characteristics or created automatically by AT, the pre-set integral value is set as I parameter
≠
0, allowing for promptly
achieving the setting value; unit is % output; proportional error compensation is: when I parameter is set to =0, for the
adjustment of reduced time to reach the temperature. The Control Period is the period of PID operation, if the control period is
10s, it means a PID operation is carried out every 10s. The result is then output to control the temperature. If the system
heats up quickly, the control period shall not be set too long. For relay output, the lifespan of the relay shall be considered; a
short period will shorten the lifespan of relay.
DeadBand
Heating sensitivity
adjustment
Heating
Cooling
Set value
(Output ON-OFF control of both actions)
Cooling sensitivity
adjustment