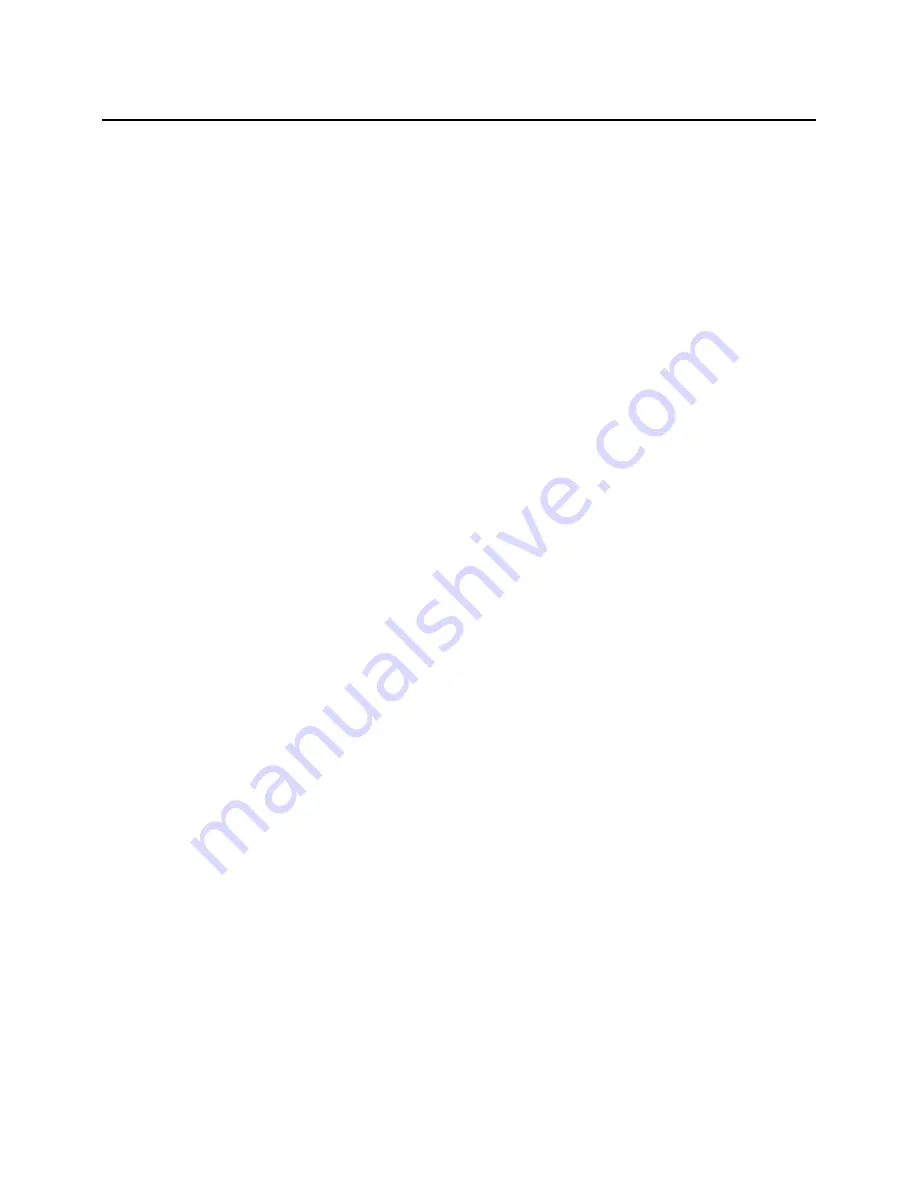
Interfacing Load to the Output Cable
The output of the PCX-7500 uses a DB-37 connector that is connected to a stripline
cable. One of these output cables is included with every system. The user may order
additional output cables if there is a need for more than one cable.
To interface to your load, you may solder the stripline directly to your load, or design a
simple two-layer interface board (recommended). The interface board must have very
low resistance, and more importantly, very low inductance in order to ensure that the
droop and overshoot specifications are met. In order to reduce the inductance, there
should be very wide copper planes on the top and bottom of the board and no copper
inner planes. PCBs thinner than 0.070 inches perform best in reducing inductance.
Copper thickness should be 2 ounces or more to reduce resistance.
DEI recommends soldering your laser directly to the interface PCB without any
additional cables or wire. If wires are absolutely necessary, they should be as short as
possible and twisted if longer than 3 cm. Wires and cabling from an interface board to
the laser will increase inductance which increases overshoot. DEI can design a custom
interface board for you at a nominal cost; please contact customer support for a
quotation.
The two photos on the next page show an interface board created for a laser used in
the DEI lab. The top of the interface board has solid copper from the stripline to the
laser’s positive terminal. The bottom of the interface board has solid copper plane
everywhere the positive plane is, plus additional copper to connect to the negative side
of the laser. The bottom copper is connected to the top of the board using as many vias
as possible (over 400 in this case). Using multiple vias reduces both inductance and
resistance. The laser is mounted in the center of the PCB, but it may be mounted
anywhere on the board.