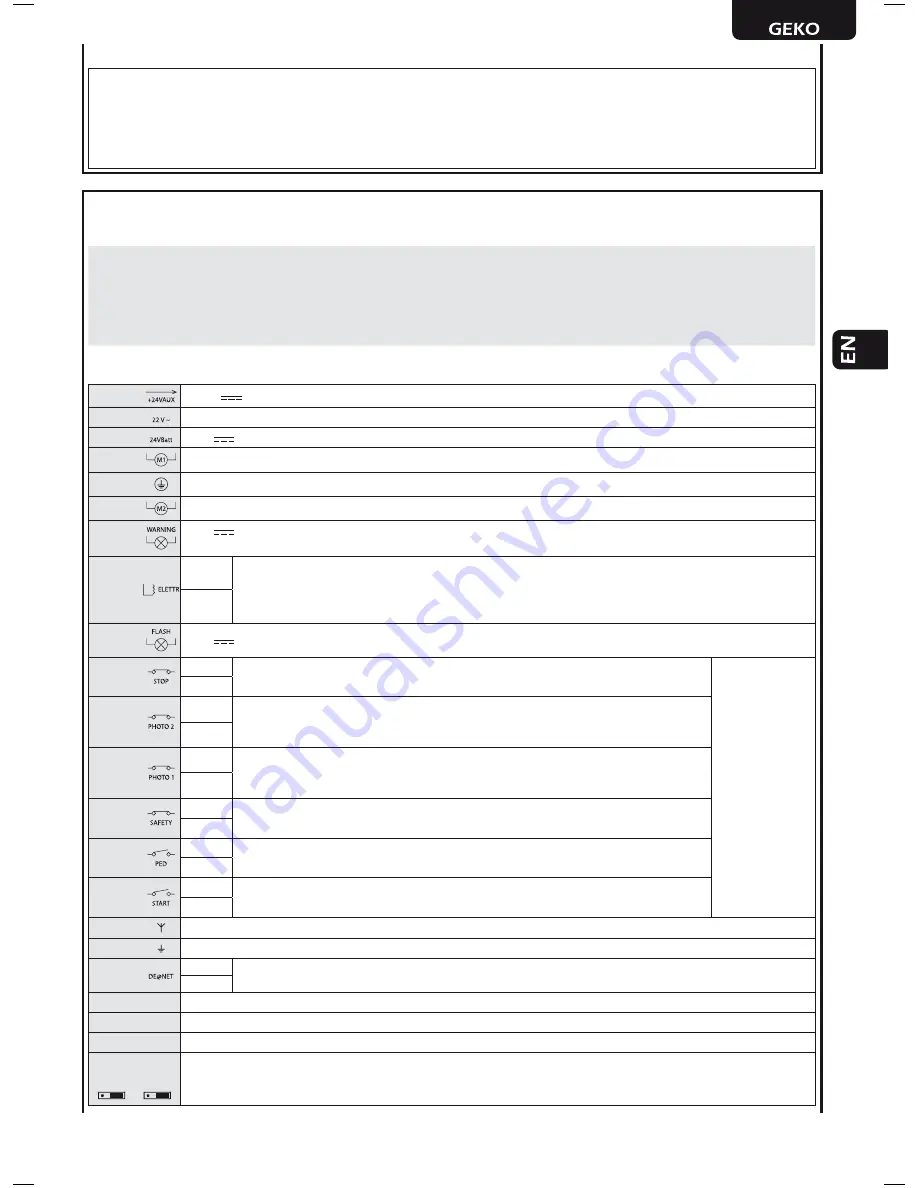
19
4.4 How to fix and adjust the mechanical limit switches
• Unlock the operator;
• Rotate the wing to the position of complete opening, position the mechanical limit switch on the stop with the straight arm and fasten it
with the provided screws (Pic. 10). If necessary, you can mount a second mechanical limit switch for the closing stop. In this case follow
the above directions by moving the door in the desired closed position and fix it with the screws provided in detention;
• Repeat the previous step for a possible second door;
• Secure the protective cover on the straight arm with the screws provided (Pic. 10).
5 ELECTRICAL CONNECTIONS
Execute the wiring following the directions of table 1 and diagrams on page 20.
WARNING
To ensure an appropriate level of electrical safety always keep the 230V power supply cables apart (minimum 4mm in the
open or 1 mm through insulation) from low voltage cables (motors power supply, controls, electric locks, aerial and auxiliary circuits
power supply), and fasten the latter with appropriate clamps near the terminal boards.
WARNING
Connect to the power supply 230 V ~± 10% 50 Hz through a multi pole switch or a different device that can ensure multi pole
disconnection from the power supply, with a contact opening of 3 mm.
WARNING
To connect the encoder to the control panel, use only a dedicated cable 3x0,22mm
2
.
Table 1 “terminal board connections”
1-2
+24 V
power supply output for auxiliary devices 200mA
3-4
22 V ~ transformer power supply input
5-6
24 V
battery power supply or photovoltaic accumulator Green Energy input (follow carefully polarity indications).
7-8
Operator 1 output
9
Connection of motors metallic parts
10-11
Operator 2 output (if present)
12-13
24 V
max 15 W output for open gate fix warning light (if P052=0), flashing (if P052=1) or courtesy light (if
P052>1)
14-15
14 (-)
“Boost” output for electric-lock, max 1 x art. 110 (if P062=0), 24V pulse output, max 5W (if P062=1), step
by step (if P062=2), electro-brake output for not self-locking operators (if P062=3), output for electric-lock
power supply via external relay (if P062=4), output for electro-magnets power supply for barriers (if P062=5)
or temporized output (if P062>5).
15 (+)
16-17
24 V
Flashing light output max 15W art. Lumy/24A/S
18-19
18 - N.C.
Input 6 STOP. In case of intervention, it stops the movement of both motors during any
operation.
If unused, short circuit
.
If
the
installation
req
uires
dif
ferent
commands
and
/
or
additional
to
the
standar
d,
you
can
configure each in
put t
o the req
uired rat
e.
R
ef
er t
o Chap
ter
“
Adv
anced Programming”.
19 - Com
20-21
20 - N.C.
Input 5 PHOTO 2. When enabled (see parameter P051 in the table), activation of PHOTO
2 provokes: an inversion of direction (during closing), the arrest of the movement (during
opening), prevent the start (gate closed).
If unused, short circuit
.
21 - Com
22-23
22 - N.C.
Input 4 PHOTO 1. When enabled (see parameter P050 in the table), activation of PHOTO
1 provokes: an inversion of direction (during closing), the arrest of the movement (during
opening), prevent the start (gate closed).
If unused, short circuit
.
23 - Com
24-25
24 - N.C.
Input 3 SAFETY. If activated, it causes the inversion. See P055 and P056 on the parame-
ters table.
If unused, short circuit
.
25 - Com
26-27
26 - N.O.
Input 2 PED. If activated, it opens motor nr. 1 only.
27 - Com
28-29
28 - N.O.
Input 1 START. In case of intervention it provokes: the operator opening or closing. It may
operate as “inversion” mode (P049=0) or “step by step” mode (P049=1).
29 - Com
30
Aerial signal input
31
Ground aerial input
32-33
32 (+)
DE@NET mains input (unused at the moment)
33 (-)
CON 1
230 V ~ ±10% (50/60 Hz) power supply input
CON 2
Connection of encoder to operator 2 (1-2-3)
CON 3
Connection of power supply to operator 2 + ground (4-5-6)
J5
J9
Encoder selection Jumper:
•A position = operators with encoder (remind to set P029=0)
•B position = operators without encoder (remind to set P029=1)
A
B
A
B
Содержание SWINGER
Страница 18: ...32 ...