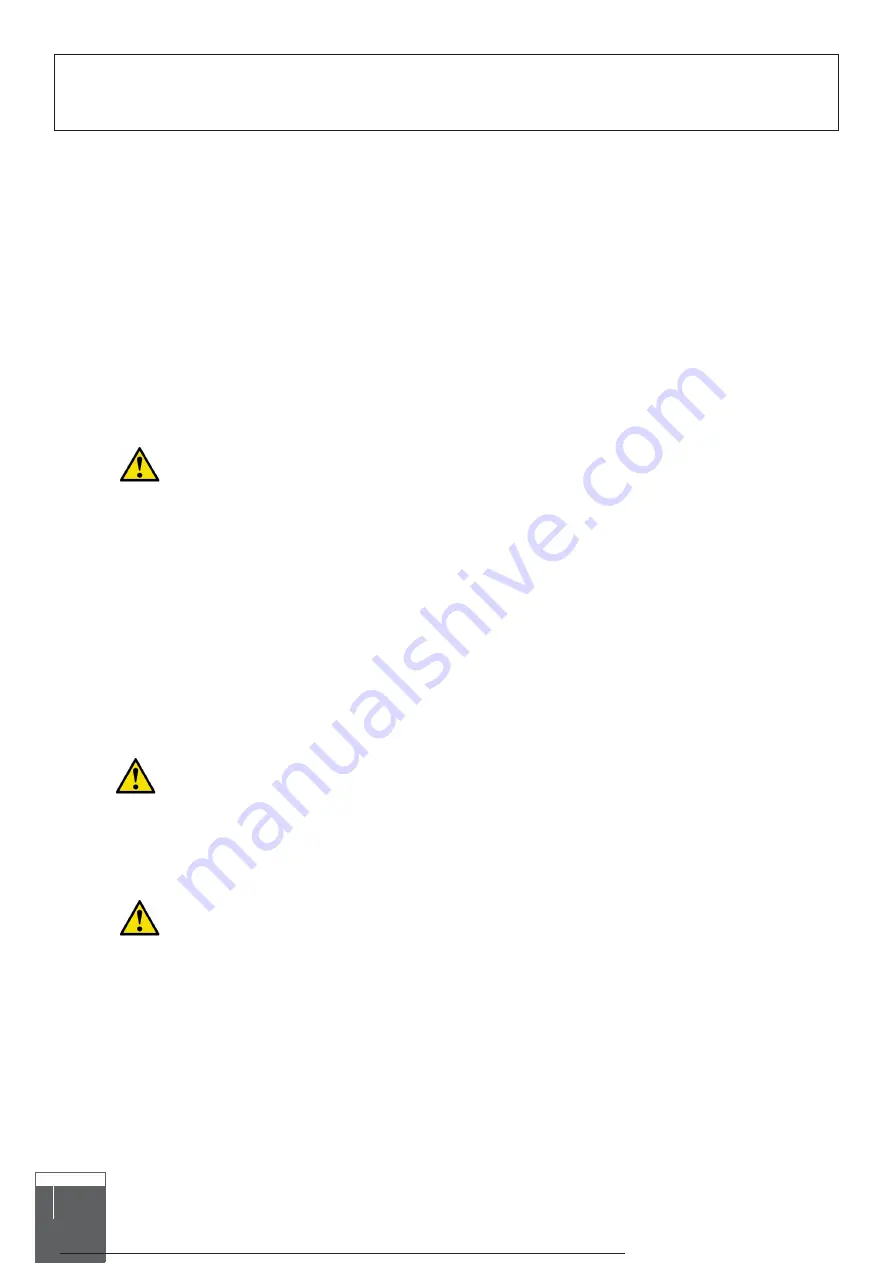
Long drain hose or the hose bore too small – either of these can contribute to an increase in back pressure.
Extremely cold weather – if the base machine hydraulic oil is of an inappropriate viscosity grade for the
ambient temperature it may well be too thick. This will cause an increase in back pressure in the drain hose.
Faulty Blow-Off Valve on the motor casing – check that this has a minimum crack pressure of 6 bar and a
maximum of 7 bar. Replace if unsure using a new calibrated valve and a new sealing ring.
Leaking seals on the sequence valve cartridge leading to excessive drain line flow rate – remove the drain
line from the EMV and measure leakage flow rate. Leakage in excess of 5 l/min (1.33gpm) indicates either
a seal kit problem with the sequence valve or high internal motor leakage. Split the sequence valve drain
line and motor case drain line and measure leakage rates independently – the sequence drain line should
have little or know leakage.
OIL BLOWING OUT OF THE GEARBOX BREATHER VALVE & THE GEAR BOX IS FULL OF OIL
The drive motor case seal has been blown, typically because the drain line pressure has been exceeded.
The unit will need to be removed from the job site and repaired in a suitably equipped workshop. The oil in
the box will be a mixture of hydraulic and gear oils.
Once in the workshop drain the oil from the gearbox and inspect the oil for signs of debris. If only the seal
has blown out without any damage to the motor casting then it may be possible to repair the motor with an
authorised Parker Hydraulics (VOAC) distributor, change the gear oil and rebuild the unit.
If however, the motor casting has also been damaged in the area of the seal housing it will be necessary
to completely inspect the inside of the gearbox. Remove the gearbox lid and inspect the gear teeth and
inspect all bearings. Check the gears for any signs of damage. Remove all bearing covers from the
gearbox sides and inspect the outer races for signs of grooves or any other contamination or damage –
look at the rollers in each bearing. The bearings and all running faces should be in perfect condition, if
not they will need to be replaced. Consult with the manufacturer at this stage or one of their approved
distributors – it is strongly recommended that the unit be repaired by the manufacturer in order to ensure
correct procedures and materials are used for an effective repair.
CLAMP CLOSES ITSELF IMMEDIATELY AFTER BEING OPENED
This fault can only occur on older units prior to serial number 45-083 without the reverse flow check valve
fitted to the return motor port. It occurs when the D reg check valve on the flow regulator becomes jammed
shut. When opening the clamp the drive motor can then rotate slowly. Once the control lever is released
the motor effectively becomes a pump, driven by the inertia of the eccentric weights in the gearbox.
Consequently the clamp can be driven closed again. Should this problem occur Dawson could supply a
reverse flow check valve as a fix.
Check the condition of the Hard Jaws.
CLAMP LOOSES GRIP ON THE PILE
The clamp can also loose grip on the pile when clamped, with the vibrator not vibrating, if the check valve
on the rear of the clamp cylinder has faulty/leaking seals or it the clamp cylinder piston seals are damaged/
worn.
Alternatively there may be insufficient system operating pressure if the sequence valve setting has been
adjusted down in order to attempt running on an unsuitable excavator. Check the system operating
pressure and excavator specifications.
emv550 hose kit
excavator mounted vibrator
30
continued - troubleshooting
Содержание EMV 550
Страница 2: ......
Страница 4: ......
Страница 34: ...parts lists for the emv550 www dcpuk com 34 ...
Страница 41: ......
Страница 44: ......
Страница 46: ......
Страница 48: ...appendix a auxiliary equipment ...
Страница 50: ......
Страница 56: ......