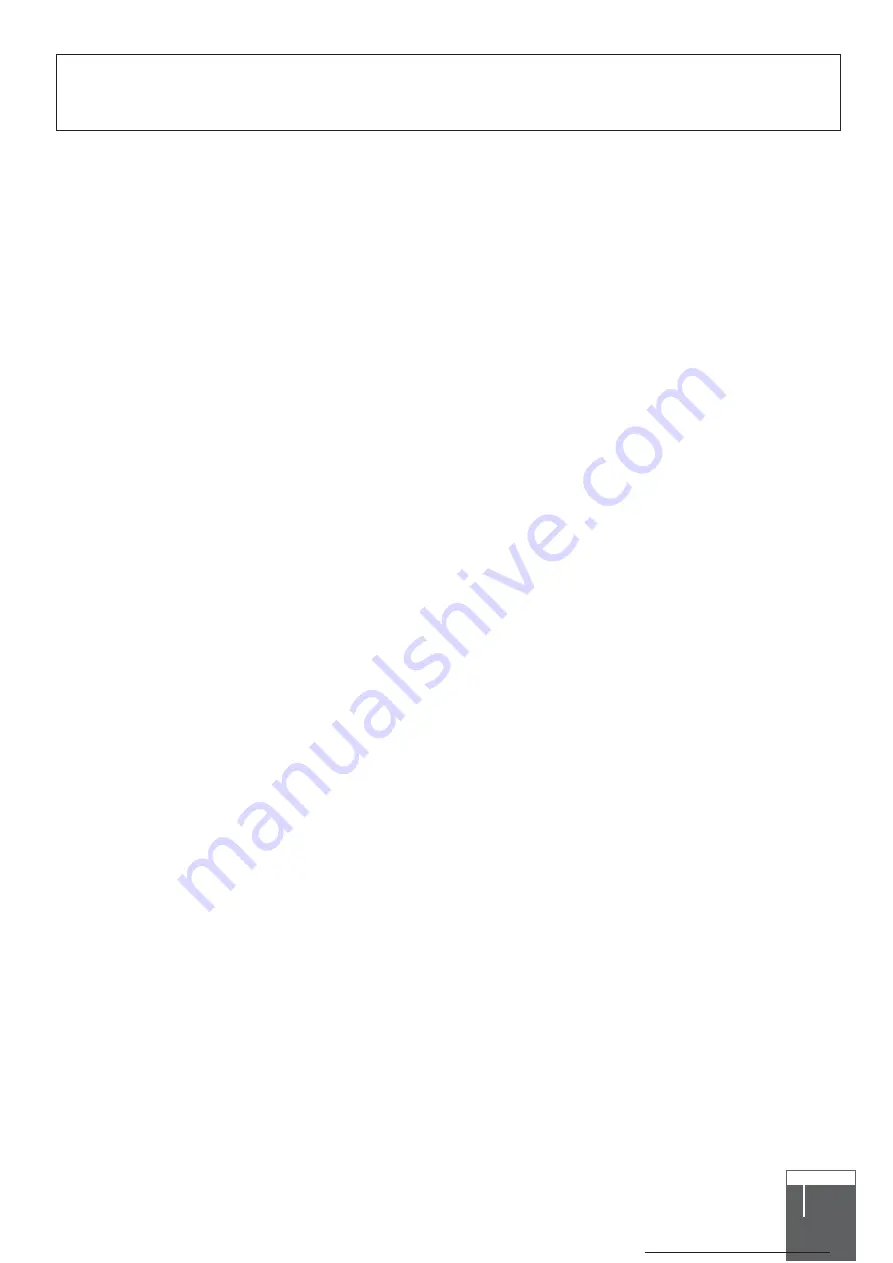
EMV
70
220
300
450
550
MAXIMUM PUSH/
PULL LOADING
lbs
6,171
16,500
33,600
33,600
49,500
kg
2,800
7,500
15,000
15,000
22,500
EMV70 (requires 30 L/min, 240 bar) ~ 5.5 - 17 t excavator
EMV220 (requires 90 L/min, 280 bar) ~ 7 - 18 t excavator
EMV300 (requires 130 L/min, 280 bar) ~ 13 - 25t excavator
EMV450 (requires 195 L/min, 270 bar) ~ 25 - 45t excavator
EMV550 (requires 256 L/min, 280 bar) ~ 30 - 55t excavator
Modern pile vibrators basically work in the same way. Pairs of high-speed contra-rotating eccentric weights
are geared together so as to produce net vertical vibratory forces.
The vibrations produced are transmitted to the pile through a powerful hydraulic grip. Consequently the pile
is vibrated at the same speed and displacement (or movement) as the gearbox itself. This vibration effect is
transmitted to the pile tip where the surrounding soils become almost fluid like.
The fluidising effect on the soil permits particles to shuffle themselves around creating some spaces for the
pile to move into. This combined with the weight of the pile and vibrator is adequate to push the pile into the
ground.
Not all soil types will however fluidise. Clays soils are very cohesive and extremely dense by comparison
to sands and gravels where vibrators work best. The dense clay soil does not allow soil particles to shuffle
them selves around so no fluidising effect can occur. Also the ground effectively sticks itself to the pile and
much of the power generated is lost in shaking the ground.
The EMV is particularly effective for its size and weight because it is able to utilise the crowd force available
from the excavator to add further push force to the pile.
The gearbox in the EMV unit is driven by a hydraulic drive motor that receives hydraulic power from the
excavators bucket ram circuit. Typically this circuit will be able to supply adequate working pressure but
excessive amount of oil flow rate. The EMV has a built-in flow regulator that limits the oil flow rate supplied
to the drive motor so that the gearbox can not be run too fast. This is essential to prevent excessive bearing
loads and correct performance of the unit.
In addition, the flow regulator has a sequence valve built-in that will not allow the vibrator to run until
adequate clamping force has been applied to the pile – an essential safety feature. This simplified hydraulic
system enables simple installation and reliable performance.
how does the emv work?
www.dcpuk.com
11
Содержание EMV 550
Страница 2: ......
Страница 4: ......
Страница 34: ...parts lists for the emv550 www dcpuk com 34 ...
Страница 41: ......
Страница 44: ......
Страница 46: ......
Страница 48: ...appendix a auxiliary equipment ...
Страница 50: ......
Страница 56: ......