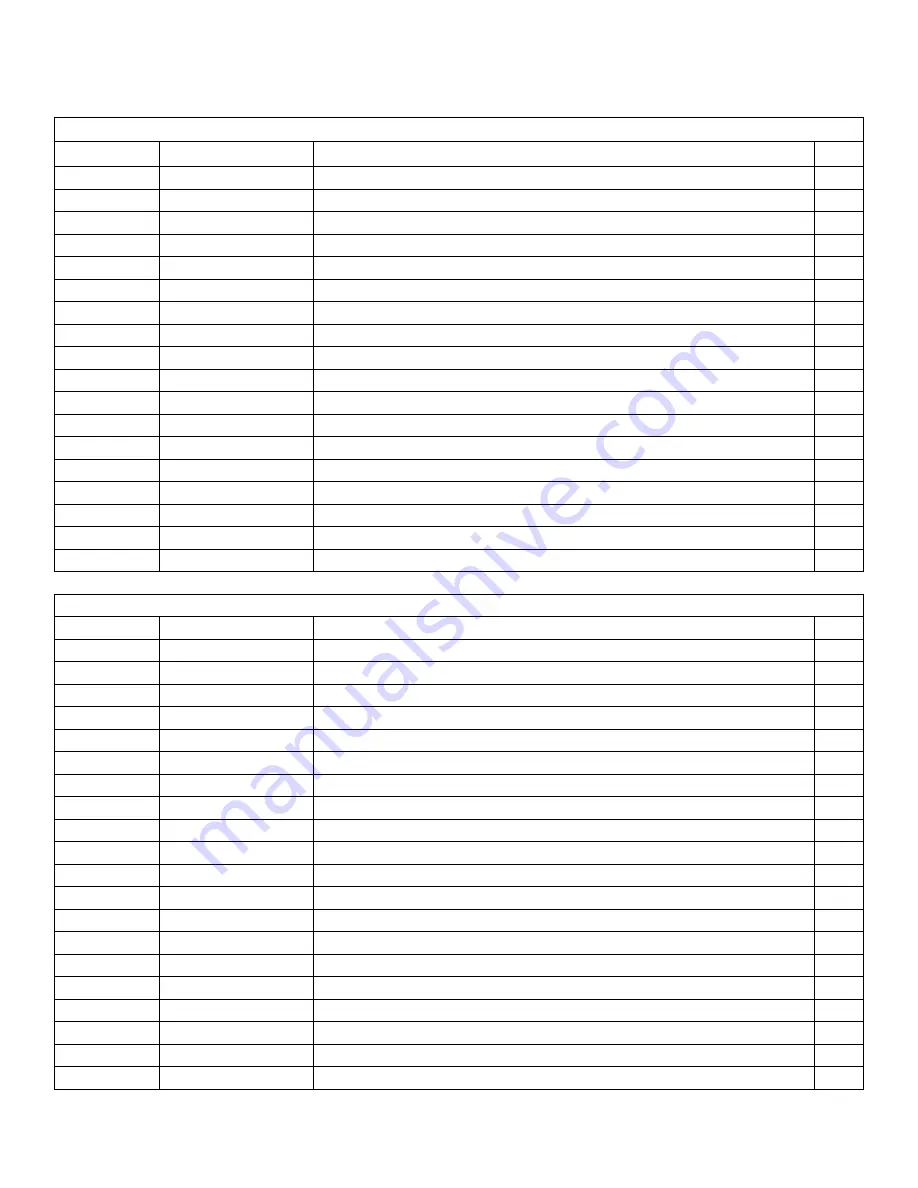
MAX JAX ASSEMBLY
ITEM NO
PART NUMBER
DESCRIPTION
QTY
1
17150002
MAX JAX POST ASSEMBLY
2
2
17154001
MAX JAX POWER UNIT STAND ASSEMBLY
1
3
17200028
M8 x 20 HEX HEAD BOLT
4
4
17201010
M8 NYLON LOCK NUT
8
5
17206016
MJ-MAORB 90~ LONG 6801-LL-06-06-NWO
1
6
17206017
MALE 90° ELBOW, EXTRA LONG 2501-LL-06-06
1
7
17156001
MAX JAX HYD. HOSE ASSEMBLY Ø10 x 4520mm
2
8
17156002
MAX JAX HYDRAULIC HOSE ASSEMBLY Ø10 x 295mm
1
9
17300003
110 VOLT, 1HP POWER UNIT
1
10
17207037
HYDRAULIC FLOW DIVIDER
1
11
17108041
SHORT LIFT PAD EXTENSION
4
12
17207015
POWER UNIT VIBRATION DAMPENER
1
13
17200005
M8 x 25 HEX HEAD BOLT
4
14
17207011
7/8 x 3-13/16 DROP IN SLEEVE ANCHOR
10
15
17200017
5/8-11 HEX HEAD BOLT
10
16
17202012
5/8 FLAT WASHER
10
17
17207033
SHIM
20
18
17107006
SLIP ON LIFT PAD ASSEMBLY
4
MAX JAX POST ASSEMBLY
ITEM NO
PART NUMBER
DESCRIPTION
QTY
1
17151001
MAX JAX POST WELDMENT
1
2
17157001
MAX JAX SAFETY PIN ASSEMBLY
1
3
17152001
MAX JAX LIFT HEAD WELDMENT
1
4
17157002
MAX JAX LIFT HEAD PIN WELDMENT
2
5
17158009
MAX JAX SLIDE BLOCK
4
6
17102009
ARM LOCK ASSEMBLY
2
7
17153001
MAX JAX ARM WELDMENT
2
8
17250017
CYLINDER ASSEMBLY Ø2.0 x 42
1
9
17200029
HEX HEAD BOLT M8 x 55mm
2
10
17200021
M10 x 45 HEX HEAD BOLT
2
11
17201010
M8 NYLON LOCK NUT
2
12
17201017
M10 NYLON LOCK NUT
2
13
17207038
C RING Ø38mm OD 5103-150
2
14
17158010
MAX JAX WHEEL
2
15
17200022
SERRATED HEX FLANGE SCREW M8 x 12
8
16
17206015
3/8-18 NPT MALE QUICK DISCONNECT COUPLING
1
17
17206019
45° STREET ELBOW 5503-06-06
1
18
17206018
HEX NIPPLE 5404-06-06
1
19
17206020
STRAIGHT EXPANDER 5405-04-06
1
20
17157003
MAX JAX POST STRAP WELDMENT
1
MAX JAX PARTS LIST
FOR TECHNICAL QUESTIONS, CALL (877)432-6627
9
Содержание maxjax
Страница 35: ......