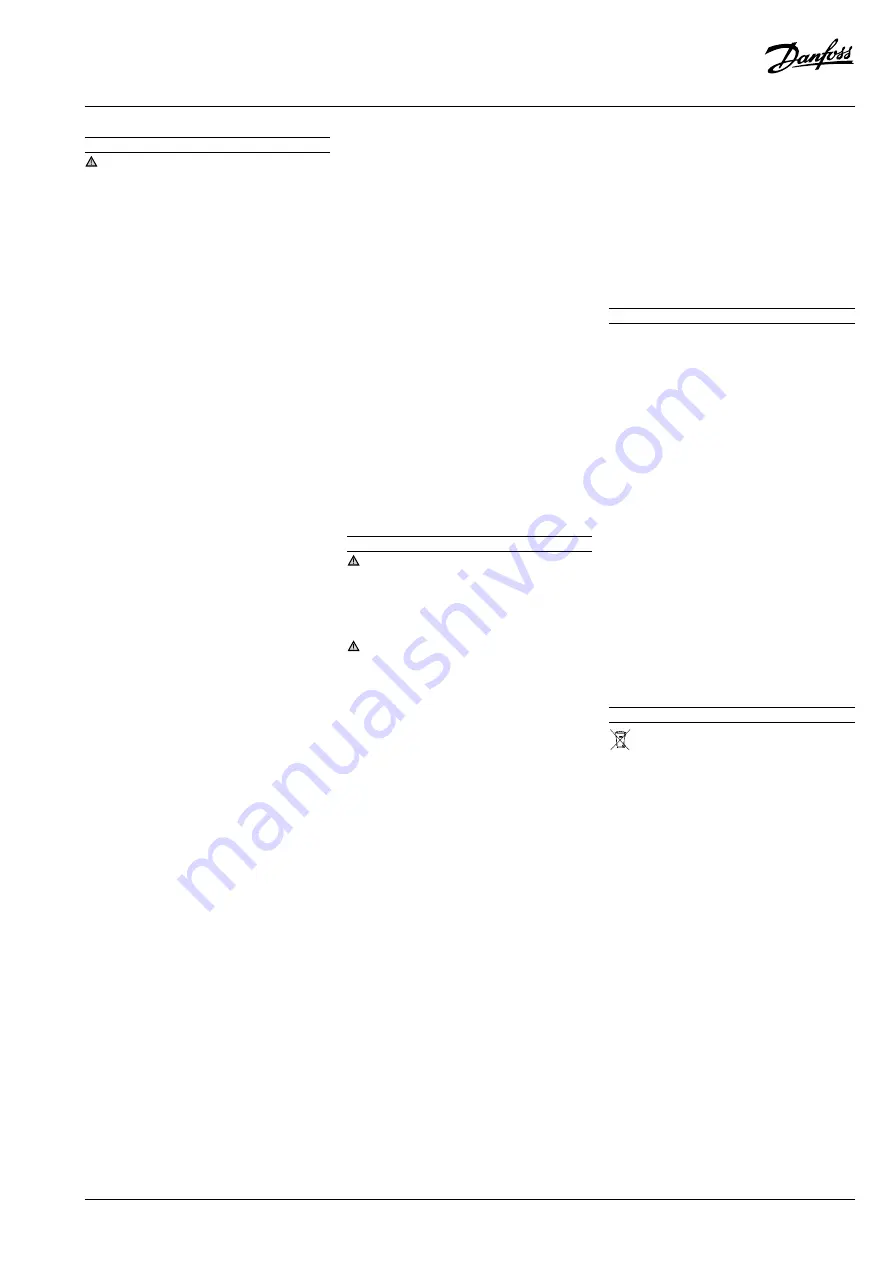
Instructions
AN233086441027en-000201 | 5
© Danfoss | DCS (CC) | 2019.03
11 – Check with running compressor
Check current draw and voltage. Measurement
of amps and volts during running conditions must
be taken at other points in the power supply, not
in the compressor electrical box.
• Check suction superheat to reduce risk of
slugging.
•
Observe the oil level at start and during
operation to confirm that the oil level remains
visible. Excess foaming in oil sight glass
indicates refrigerant on the sump.
• Monitor the oil sight glass for 1 hour after
system equilibrium to ensure proper oil return
to the compressor. This oil check has to be
done over the speed range to guarantee:
- a good oil return at low speed with minimum
gas velocity.
- a good oil management at high speed with
maximum oil carry over.
• Respect the operating limits.
•
Check all tubes for abnormal vibration.
Movements in excess of 1.5 mm / 0.06 inch
require corrective measures such as tube
brackets.
• When needed, additional refrigerant in liquid
phase may be added in the low-pressure side
as far as possible from the compressor. The
compressor must be operating during this
process.
• Do not overcharge the system.
• Never release refrigerant to atmosphere.
• Before leaving the installation site, carry out
a general installation inspection regarding
cleanliness, noise and leak detection.
• Record type and amount of refrigerant charge
as well as operating conditions as a reference
for future inspections.
• Compressor failure to build up pressure: Check
all bypass valves in the system to ensure that
none of these has been opened. Also check
that all solenoid valves are in their proper
position.
• Abnormal running noise: Ensure the absence
of any liquid flood-back to the compressor by
means of measuring the return gas superheat
and compressor sump temperature. The sump
should be at least 6K above the saturated
suction temperature under steady-state
operating conditions.
•
The high-pressure switch trips out: Check
condenser operations (condenser cleanliness,
fan operation, water flow and water
pressure valve, water filter, etc.). If all these
are OK, the problem may be due to either
refrigerant overcharging or the presence of
a noncondensable (e.g. air, moisture) in the
circuit.
•
The low-pressure switch trips out: Check
evaporator operations (coil cleanliness, fan
operations, water flow, water filter, etc.), liquid
refrigerant flow and pressure drops (solenoid
valve, filter dryer, expansion valve, etc.),
refrigerant charge.
• Low refrigerant charge: The correct refrigerant
charge is given by the liquid sight glass
indication, the condenser delta T in relation
to the refrigerant pressure tables (pressure-
temperature), the superheat and the sub-
cooling, etc. (if additional charge is deemed
necessary, refer to section 8).
•
Compressor short cycling: The number of
cycles shall never exceed 12 starts per hour.
12 – Maintenance
Internal pressure and surface temperature
are dangerous and may cause permanent injury.
Maintenance operators and installers require
appropriate skills and tools. Tubing temperature may
exceed 100°C / 212°F and can cause severe burns.
Ensure that periodic service inspections to
ensure system reliability and as required by local
regulations are performed.
To prevent system related compressor problems,
following periodic maintenance is recommended:
• Verify that safety devices are operational and
properly set.
• Ensure that the system is leak tight.
• Check the compressor current draw by reading
one of the parameters via Modbus.
• Confirm that the system is operating in a way
consistent with previous maintenance records
and ambient conditions.
• Check that all electrical connections are still
adequately fastened.
•
Keep the compressor clean and verify
the absence of rust and oxidation on the
compressor shell, tubes and electrical
connections.
• Acid / moisture content in system and oil
should be checked regularly.
13 - Warranty
Always transmit the model number and serial
number with any claim filed regarding this
product.
Use the fault memory of the frequency converter
to recover the fault descriptions before initializing
the system and even before shutting off the
power.
Variable speed drive model and serial number
must also be transmitted with the claim.
The product warranty may be void in following
cases:
• Absence of nameplate.
• External modifications; in particular, drilling,
welding, broken feet and shock marks.
• Compressor opened or returned unsealed.
• Rust, water or leak detection dye inside the
compressor.
• Use of a refrigerant or lubricant not approved
by Danfoss.
• Any deviation from recommended instructions
pertaining to installation, application or
maintenance.
• Use in mobile applications.
• Use in explosive atmospheric environment.
• No model number or serial number transmitted
with the warranty claim.
14 – Disposal
Danfoss recommends that compressors and
compressor oil should be recycled by a
suitable company at its site.