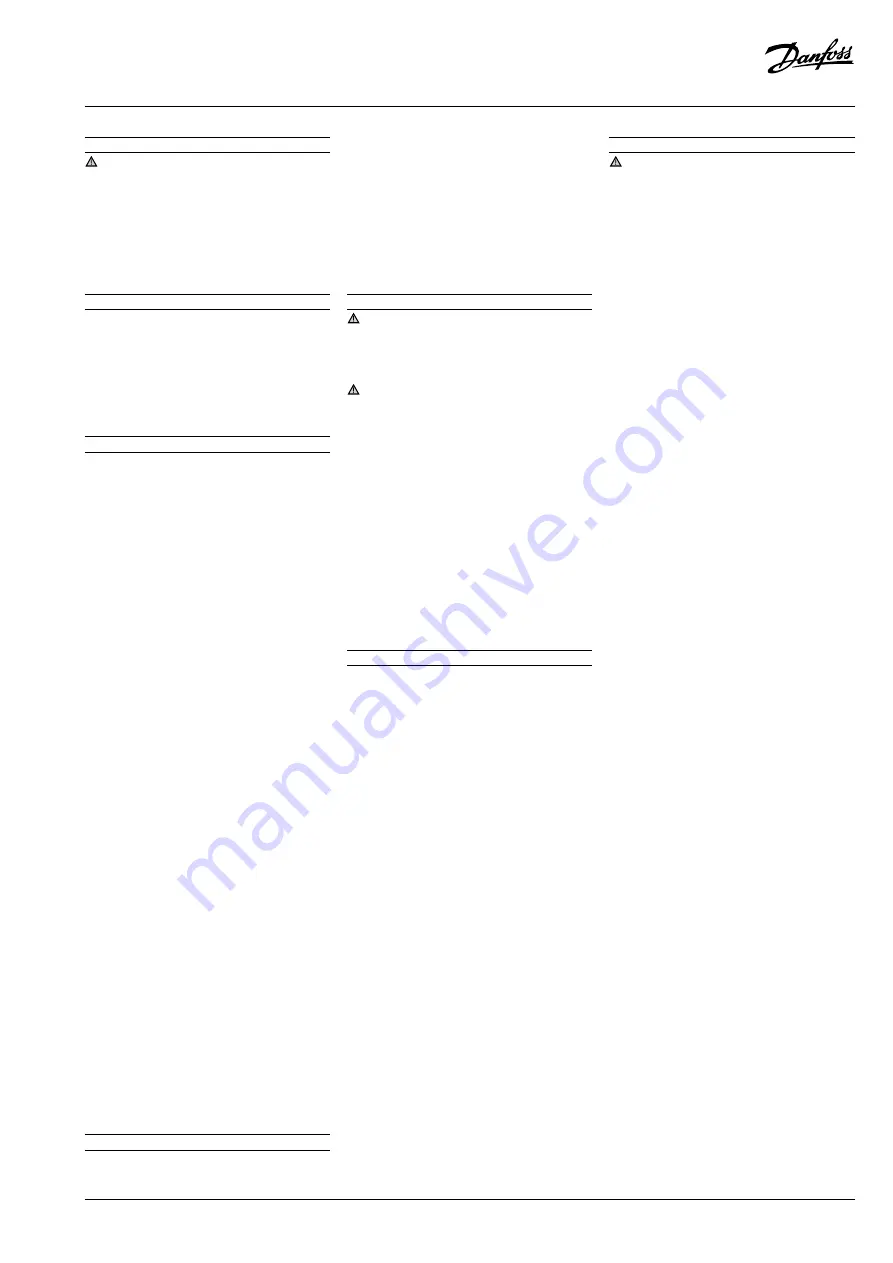
Instructions
8510286P01AA - AN280556890612en-000201 | 3
© Danfoss | DCS (CC) | 2022.11
5 – Leak detection
Never pressurize the circuit with oxygen or dry
air. This could cause fire or explosion.
• Do not use leak detection dye.
• Perform a leak detection test on the complete
system.
• The low side test pressure must not exceed 31 bar
/450 psi.
• When a leak is discovered, repair the leak and
repeat the leak detection.
6 – Vacuum dehydration
• Never use the compressor to evacuate the
system.
• Connect a vacuum pump to both the LP & HP sides.
• Pull down the system under a vacuum of 500
µm Hg (0.67 mbar) / 0.02 inch Hg absolute.
• Do not use a mega ohmmeter nor apply power
to the compressor while it is under vacuum as
this may cause internal damage.
7 – Electrical connections
• Switch off and isolate the main power supply.
• Before touching any potentially live part of the
drive, wait at least 4 minutes.
• The compressor is protected against excess
current by the frequency converter. Follow
local regulations regarding power line
protection.The compressor must be connected
to ground.
• Use 6.3 mm tabs for quick connect spade
terminals.
• Use a self-tapping screw to connect the ground
conductor to the compressor.
•
Care must be taken during installation to
ensure that the compressor operates in the
correct direction. T1 (U), T2 (V) and T3 (W)
terminals of compressor and drive U, V, W must
match. Please refer to drawings for typical
wiring connections and examine the specific
wiring diagram located in the frequency
converter package. For further details, refer to
the application guidelines.
• Mounting: The base frame of the frequency
converter must be very well fixed to the
support to ensure a very good continuity
between the ground potential of all electrical
panels and electrical boxes of the system.
•
Wiring: All control wires have to be of a
screened design. The cable for electrical motor
supply has to be of a shielded design as well.
Correct earthing of the shield cover has to be
done using the method shown on drawings,
every time this one has to be earthed on each
end of the cables. Distinct cable trays must be
used for control and motor supply.
• The frequency converter ensures direct motor
protection and the factory set parameters
are such to protect the motor over all current
malfunctions. An external overload is not
necessary.
• Set the frequency converter parameters in
accordance with Danfoss recommendations
for the frequency converter and VLZ variable
speed compressor.
•
Refer to variable speed drive manual for
electrical connections details and installation.
• Compressor motor protection is provided by
the variable speed drive.
8 – Filling the system
• Keep the compressor switched off.
• Fill the refrigerant in liquid phase into the
outlet of the condenser or the liquid receiver.
The charge must be as closed as possible
to the nominal system charge to avoid low
pressure operation and excessive superheat.
For VLZ028-044, the refrigerant charge limit is
3.6 kg, Pump down switch setting should be
not lower than 1.0 bar(g) for R448A/1.0 bar(g)
for R449A/1.5 bar(g) for R404A.
• Never leave the filling cylinder connected to
the circuit.
9 – Verification before commissioning
Use safety devices such as safety pressure
switch and mechanical relief valve in compliance
with both generally and locally applicable
regulations and safety standards. Ensure that
they are operational and properly set.
Check that the settings of high-pressure
switches do not exceed the maximum service
pressure of any system component.
• A low-pressure switch is mandatory to avoid
vacuum operation. Minimum setting 0.8 bar(g)
for R448A/R449A. Minimum pressure 1.3 bar(g)
for R404A.
•
Verify that all electrical connections are
properly fastened and in compliance with local
regulations.
•
When using discharge temperature sensor,
ensure that the discharge temperature sensor
is correctly installed and fitted to the discharge
piping (6 inches from discharge fitting) and
well connected, especially after maintenance
operations.
• After comissioning it is strongly recommended to
keep the frequency converter always energized.
10 – Start-up
• Never start the compressor when no refrigerant
is charged.
• Do not provide any power to the drive unless
suction and discharge service valves on
compressor are open, if installed.
• Energize the drive. The compressor must start,
according to defined ramp-up settings. If
the compressor does not start, check wiring
conformity.
• Check the frequency converter control panel:
If any alarm is displayed check the wiring and
in particular the polarity of the control cables.
If an alarm is shown, refer to the frequency
converter application manual. Verify in
particular the combination of compressor,
frequency converter and refrigerant.
• Check current draw and voltage levels on the
mains. The values for the compressor electrical
motor can be directly displayed on the
frequency converter control panel.
• The optimum compressor suction superheat is
around 10K.
• Eventual reverse rotation can be detected by
following phenomena; the excessive noise,
no pressure differential between suction
and discharge, and line warming rather than
immediate cooling. A service technician should
be present at initial start-up to verify that
wiring from drive to compressor is properly
phased and that the compressor is rotating in
the correct direction.
• Note that a 300 seconds period is necessary
between 2 starts, a shorter period will be not
allowed by the drive. The minimum running
time is 12s for each start.
11 – Check with running compressor
Check current draw and voltage. Measurement
of amps and volts during running conditions must
be taken at other points in the power supply, not
in the compressor electrical box.
• Check suction superheat to reduce risk of
slugging.
•
Observe the oil level at start and during
operation to confirm that the oil level remains
visible. Excess foaming in oil sight glass
indicates refrigerant on the sump.
• Monitor the oil sight glass for 1 hour after
system equilibrium to ensure proper oil return
to the compressor. This oil check has to be
done over the speed range to guarantee:
- a good oil return at low speed with minimum
gas velocity.
- a good oil management at high speed with
maximum oil carry over.
• Respect the operating limits.
•
Check all tubes for abnormal vibration.
Movements in excess of 1.5 mm / 0.06 inch
require corrective measures such as tube
brackets.
• When needed, additional refrigerant in liquid
phase may be added in the low-pressure side
as far as possible from the compressor. The
compressor must be operating during this
process.
• Do not overcharge the system.
• Never release refrigerant to atmosphere.
• Before leaving the installation site, carry out
a general installation inspection regarding
cleanliness, noise and leak detection.
• Record type and amount of refrigerant charge
as well as operating conditions as a reference
for future inspections.
• Compressor failure to build up pressure: Check
all bypass valves in the system to ensure that
none of these has been opened. Also check
that all solenoid valves are in their proper
position.
• Abnormal running noise: Ensure the absence
of any liquid flood-back to the compressor by
means of measuring the return gas superheat
and compressor sump temperature. The sump
should be at least 10K above the saturated
suction temperature under steady-state
operating conditions.
•
The high-pressure switch trips out: Check
condenser operations (condenser cleanliness,
fan operation, water flow and water
pressure valve, water filter, etc.). If all these
are OK, the problem may be due to either
refrigerant overcharging or the presence of
a noncondensable (e.g. air, moisture) in the
circuit.
•
The low-pressure switch trips out: Check
evaporator operations (coil cleanliness, fan
operations, water flow, water filter, etc.), liquid
refrigerant flow and pressure drops (solenoid
valve, filter dryer, expansion valve, etc.),
refrigerant charge.
• Low refrigerant charge: The correct refrigerant
charge is given by the liquid sight glass
indication, the condenser delta T in relation
to the refrigerant pressure tables (pressure-
temperature), the superheat and the sub-
cooling, etc. (if additional charge is deemed
necessary, refer to section 8).
•
Compressor short cycling: The number of
cycles shall never exceed 12 starts per hour.