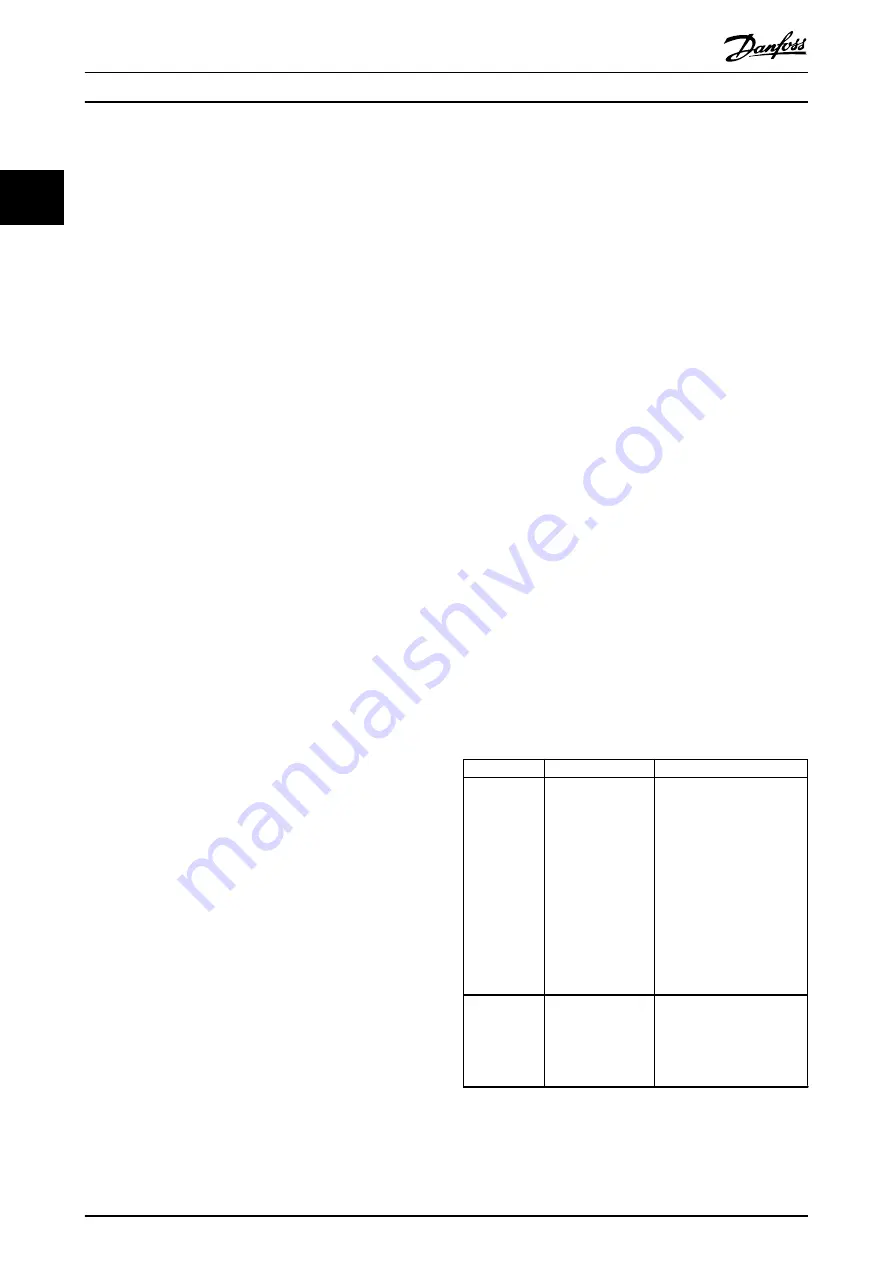
2.10 Automated Operational Functions
2.10.1 Short Circuit Protection
2.10.1.1 Servo Access Box Features
The SAB has several protection functions for limiting the
current:
•
I
N
100% (15 A
RMS
), no limitation.
•
100–200% current is limited by an I
2
t function. A
load of 160% is allowed for 1 minute. The RMS
current must be lowered to
≤
100% before a new
overload is allowed. The time taken to reset the
I
2
t function depends on the load current. A 2 A
overload for 10 s (17 A) requires a nominal
current of
≤
13 A for 10 s to reset the I
2
t function.
I
DC
protection (UDC)
•
Imax0: At 200% RMS, the output will be discon-
nected within 1.5 s.
•
Imax1: At 51 A peak current, the output will be
disconnected within 500
μ
s.
•
Imax2: At 125 A peak current, the output will be
disconnected within 10
μ
s.
I
AUX
protection
•
Software limit range: 0–15 A
-
A warning and alarm is issued at user-
specified levels. A warning is issued at
90% of the selected value. An alarm is
issued when the measured value has
exceeded the software limit.
•
These software limits are disabled by default. See
parameters
AUX line 1 user current limit
and
AUX
line 2 user current limit
in the
VLT
®
Integrated Servo
Drive ISD 510 System Programming Guide
.
•
A low-pass filter is implemented in the firmware
to avoid unintended warnings or alarms due to
inrush currents.
2.10.1.2 ISD 510 Servo Drive Features
To protect the servo drive and the machinery attached to
the servo drive shaft, a current limit protection is
implemented in the servo drive.
Current limit protection is implemented on the servo drive
and the currents are constantly monitored. If an
overcurrent occurs, an error is issued and the servo drive
coasts to stop as default. For servo drives with the
mechanical brake option, the brake engages.
2.10.2 Ground Fault Protection
When a ground fault current of >3 A is present, a warning
is issued immediately. The SAB issues an error if the
warning is present for 10 s.
2.10.3 Temperature-controlled Fans
The SAB has 2 built-in forced air convection fans to ensure
optimum cooling. The main fan forces the airflow along
the cooling fins on the heat sink, ensuring cooling of the
internal air. A secondary fan cools the SAB power control
board. Both fans are controlled by the internal temperature
and speed increases. The fans not only ensure maximum
cooling when required, but also reduce noise and energy
consumption when the workload is low.
If overtemperature occurs in the SAB, an error/warning is
issued, resulting in a coast and trip lock.
2.10.4 Thermal Protection
Thermal protection exists for both the servo drive and the
SAB. See
chapter 4.6.3 Thermal Protection
for further
information.
2.10.5 Additional Protection Features
2.10.5.1 Servo Access Box
The SAB has the additional protection features detailed in
Function
Description
Limits/errors
UDC
overvoltage
When the DC-link
voltage rises above
a certain level, a
warning/error is
issued.
A brake resistor can
be connected to
the SAB and
activated via
parameter 0x2030
in
the DDS Toolbox
software.
•
Brake active: >778 V
•
Warning: >810 V
•
Error: >820 V
UDC
undervoltage
When the DC-link
voltage drops
below a certain
level, a warning/
error is issued.
•
Warning: <410 V
•
Error: <373 V
System Overview
VLT
®
Integrated Servo Drive ISD
®
510 System
24
Danfoss A/S © 08/2017 All rights reserved.
MG36C102
2
2