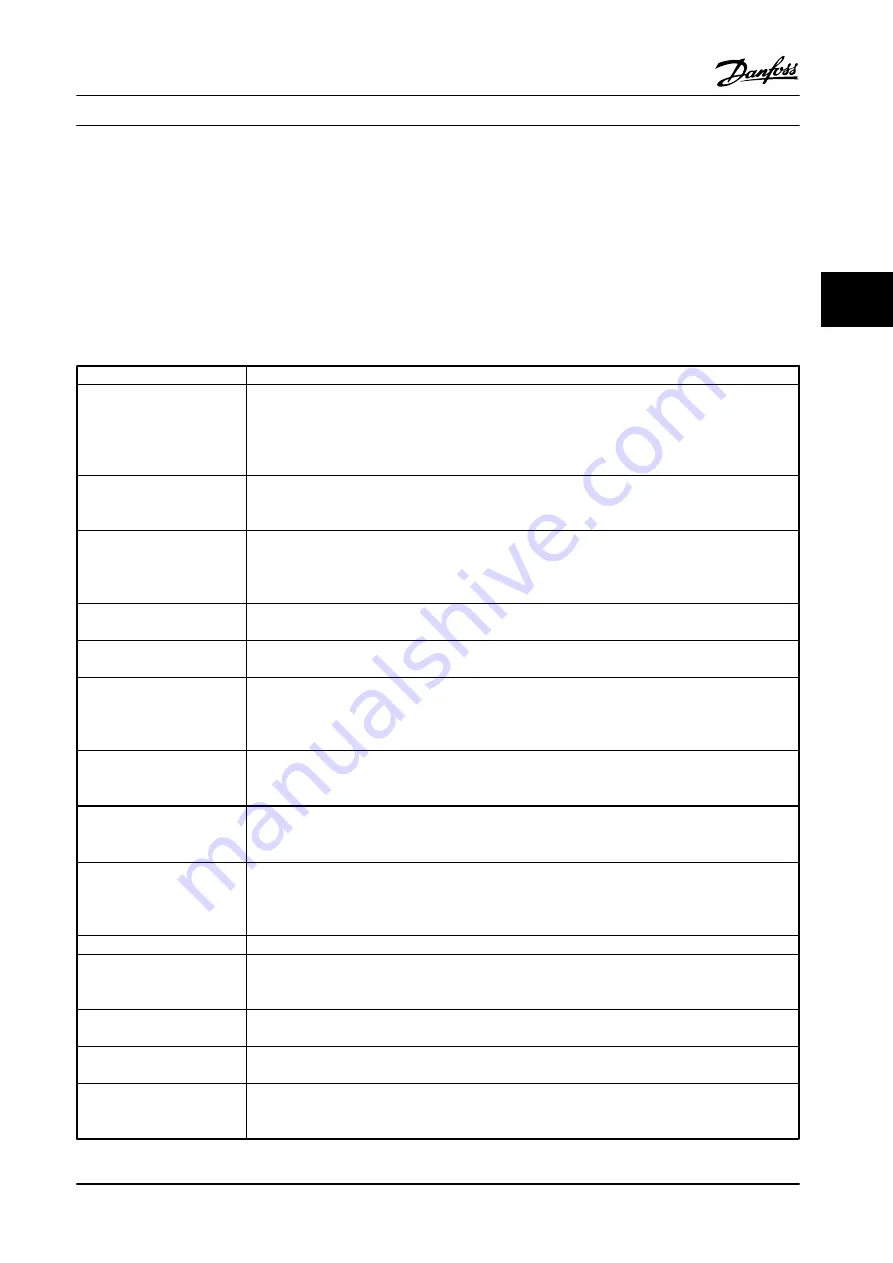
Finally, a list of tests
chapter 4.7 After Repair Tests
is provided. Always perform these tests under the following conditions:
•
Starting an adjustable frequency drive for the first time.
•
Approaching an adjustable frequency drive that is suspected of being faulty.
•
After a repair to the adjustable frequency drive.
4.4 Visual Inspection
lists various conditions that require visual inspection as part of any initial troubleshooting procedure.
Inspect For
Description
Auxiliary equipment
Look for auxiliary equipment, switches, disconnects, or input fuses/circuit breakers that reside on either
the input power side of adjustable frequency drive or the output side to the motor. Examine the
operation and condition of these items for possible causes of operational faults. Check the function and
installation of pressure sensors or encoders or other devices that provide feedback to the adjustable
frequency drive.
Cable routing
Avoid routing motor wiring, line power wiring, and signal wiring in parallel. If parallel routing is
unavoidable, try to maintain a separation of 150–200 mm (6–8 inches) between the cables or separate
them with an grounded conductive partition. Avoid routing cables through free air.
Control wiring
Check for broken or damaged wires and connections. Check the voltage source of the signals. Though
not always necessary depending on the installation conditions, the use of shielded cable or a twisted
pair is recommended. Ensure that the shield is terminated correctly. Refer to
.
Drive cooling
Check the operational status of all cooling fans. Check the door filters on NEMA 12 (IP54) units. Check
for blockage or constrained air passages. Make sure that the bottom connector plate is installed.
Drive display
Warnings, alarms, drive status, fault history, and many other important items are available via the local
control panel display on the adjustable frequency drive.
Drive interior
The adjustable frequency drive interior must be free of dirt, metal chips, moisture, and corrosion. Check
for burned or damaged power components or carbon deposits resulting from catastrophic component
failure. Check for cracks or breaks in the housings of power semiconductors, or pieces of broken
component housings loose inside the unit.
EMC considerations
Check for proper installation regarding electromagnetic capability. Refer to the adjustable frequency
drive instruction manual and
chapter 5 Adjustable Frequency Drive and Motor Applications
for further
details.
Environmental conditions
Under specific conditions, these units can be operated within a maximum ambient temperature of 122
°
F
[50
°
C]. Humidity levels must be less than 95% non-condensing. Check for harmful airborne contaminates
such as sulfur-based compounds.
Grounding
The adjustable frequency drive requires a dedicated ground wire from its frame to the building ground.
It is also suggested that the motor be grounded to the adjustable frequency drive frame as well. The use
of a conduit or mounting the adjustable frequency drive onto a metal surface is not considered a
suitable ground. Check for good ground connections that are tight and free of oxidation.
Input power wiring
Check for loose connections. Check for proper fusing. Check for blown fuses.
Motor
Check the nameplate ratings of the motor. Ensure that the motor ratings coincide with the adjustable
frequency drives. Make sure that the motor parameters (
1-20 Motor Power [kW]
through
1-25 Motor
Nominal Speed
) are set according to the motor ratings.
Output to motor wiring
Check for loose connections. Check for switching components in the output circuit. Check for faulty
contacts in the switch gear.
Programming
Make sure that the adjustable frequency drive parameter settings are correct according to motor,
application, and I/O configuration.
Proper clearance
Adjustable frequency drives require adequate top and bottom clearance to ensure proper air flow for
cooling in accordance with the adjustable frequency drive size. Adjustable frequency drives with exposed
heatsinks out the back must be mounted on a flat solid surface.
Troubleshooting
Service Manual
MG94A222
Danfoss A/S © Rev. 2014-02-10 All rights reserved.
47
4
4