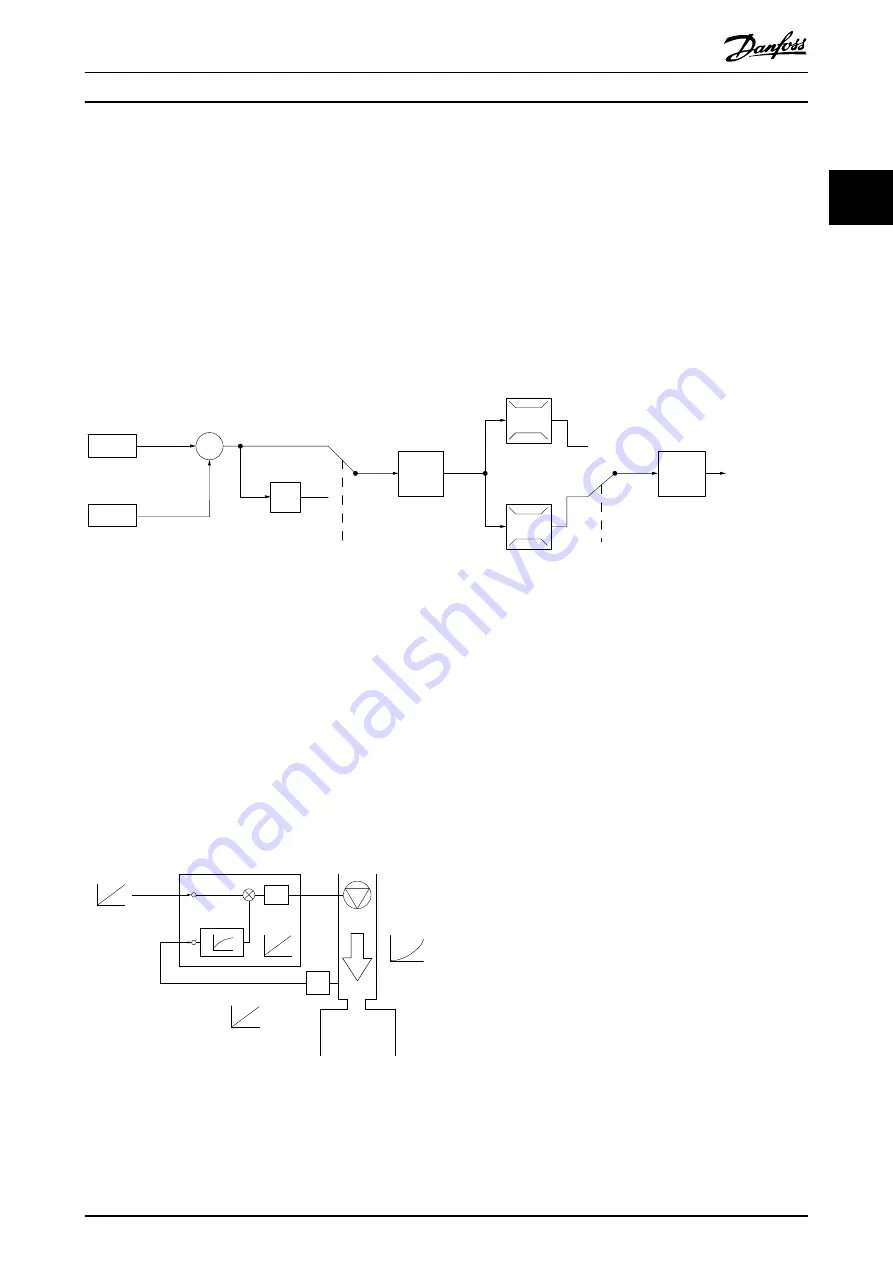
2.6.3 Control Structure Closed Loop
The internal controller allows the frequency converter to become a part of the controlled system. The frequency converter
receives a feedback signal from a sensor in the system. It then compares this feedback to a setpoint reference value and
determines the error, if any, between these 2 signals. It then adjusts the speed of the motor to correct this error.
For example, consider an application where the speed is to be controlled so that the static pressure in a pipe is constant.
The desired static pressure value is supplied to the frequency converter as the setpoint reference. A static pressure sensor
measures the actual static pressure in the pipe and supplies this to the frequency converter as a feedback signal. If the
feedback signal is greater than the setpoint reference, the frequency converter slows down to reduce the pressure. In a
similar way, if the pipe pressure is lower than the setpoint reference, the frequency converter automatically speeds up to
increase the pressure provided by the pump.
7-30 PI
Normal/Inverse
Control
PI
Reference
Feedback
Scale to
speed
P 4-10
Motor speed
direction
To motor
control
130BB894.11
S
100%
0%
-100%
100%
*[-1]
_
+
Illustration 2.3 Control Structure Closed Loop
While the default values for the frequency converter’s closed-loop controller often provides satisfactory performance, the
control of the system can often be optimized by adjusting some of the closed-loop controller’s parameters.
2.6.4 Feedback Conversion
In some applications, it may be useful to convert the
feedback signal. One example of this is using a pressure
signal to provide flow feedback. Since the square root of
pressure is proportional to flow, the square root of the
pressure signal yields a value proportional to the flow. See
130BB895.10
+
-
PI
P
P
P
Ref.
signal
Desired
flow
FB conversion
Ref.
FB
Flow
FB
signal
Flow
P 20-01
Illustration 2.4 Feedback Signal Conversion
Product Overview
Design Guide
MG18N202
Danfoss A/S © 12/2015 All rights reserved.
13
2
2