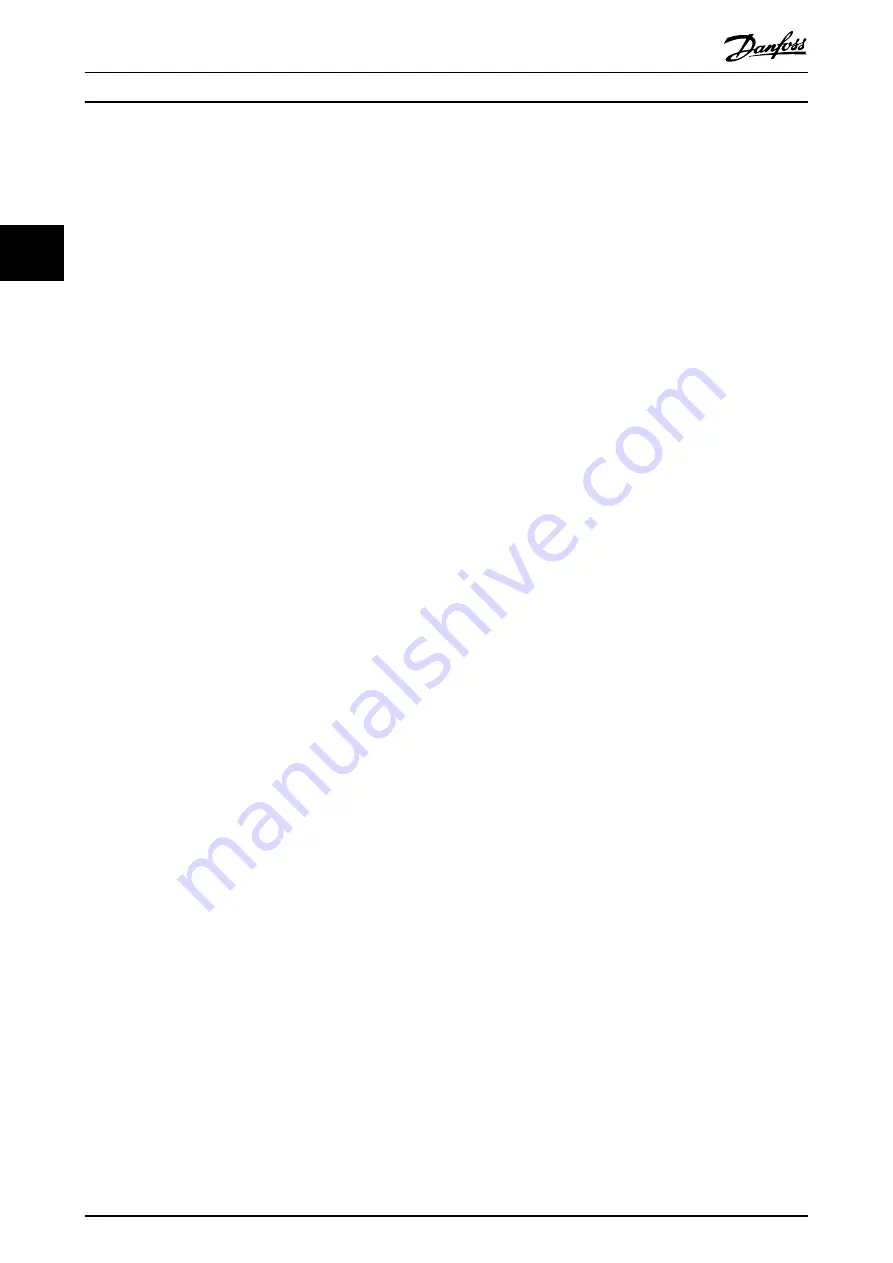
3.2.12 Power Fluctuation Performance
The drive withstands mains fluctuations such as:
•
Transients.
•
Momentary drop-outs.
•
Short voltage drops.
•
Surges.
The drive automatically compensates for input voltages
±
10% from the nominal to provide full rated motor voltage
and torque. With auto restart selected, the drive automat-
ically powers up after a voltage trip. With flying start, the
drive synchronizes to motor rotation before start.
3.2.13 Resonance Damping
Resonance damping eliminates the high-frequency motor
resonance noise. Automatic or manually selected frequency
damping is available.
3.2.14 Temperature-controlled Fans
Sensors in the drive regulate the operation of the internal
cooling fans. Often, the cooling fans do not run during low
load operation, or when in sleep mode or standby. These
sensors reduce noise, increase efficiency, and extend the
operating life of the fan.
3.2.15 EMC Compliance
Electromagnetic interference (EMI) and radio frequency
interference (RFI) are disturbances that can affect an
electrical circuit due to electromagnetic induction or
radiation from an external source. The drive is designed to
comply with the EMC product standard for drives IEC
61800-3 and the European standard EN 55011. Motor
cables must be shielded and properly terminated to
comply with the emission levels in EN 55011. For more
information regarding EMC performance, see
chapter 7.13.1 EMC Test Results
3.2.16 Galvanic Isolation of Control
Terminals
All control terminals and output relay terminals are galvan-
ically isolated from mains power, which completely
protects the controller circuitry from the input current. The
output relay terminals require their own grounding. This
isolation meets the stringent protective extra-low voltage
(PELV) requirements for isolation.
The components that make up the galvanic isolation
are:
•
Supply, including signal isolation.
•
Gatedrive for the IGBTs, trigger transformers, and
optocouplers.
•
The output current Hall effect transducers.
3.3 Custom Application Features
Custom application functions are the most common
features programmed in the drive for enhanced system
performance. They require minimum programming or set-
up. See the
programming guide
for instructions on
activating these functions.
3.3.1 Automatic Motor Adaptation
Automatic motor adaptation (AMA) is an automated test
procedure used to measure the electrical characteristics of
the motor. AMA provides an accurate electronic model of
the motor, allowing the drive to calculate optimal
performance and efficiency. Running the AMA procedure
also maximizes the automatic energy optimization feature
of the drive. AMA is performed without the motor rotating
and without uncoupling the load from the motor.
3.3.2 Built-in PID Controller
The built-in proportional, integral, derivative (PID)
controller eliminates the need for auxiliary control devices.
The PID controller maintains constant control of closed-
loop systems where regulated pressure, flow, temperature,
or other system requirements must be maintained.
The drive can use 2 feedback signals from 2 different
devices, allowing the system to be regulated with different
feedback requirements. The drive makes control decisions
by comparing the 2 signals to optimize system
performance.
3.3.3 Motor Thermal Protection
To protect the application from serious damage, the drive
offers several dedicated features.
Torque limit
The torque limit protects the motor from being overloaded
independent of the speed. Torque limit is controlled in
parameter 4-16 Torque Limit Motor Mode
and
parameter 4-17 Torque Limit Generator Mode
.
Parameter 14-25 Trip Delay at Torque Limit
controls the time
before the torque limit warning trips.
Current limit
Parameter 4-18 Current Limit
controls the current limit, and
parameter 14-24 Trip Delay at Current Limit
controls the
time before the current limit warning trips.
Product Overview and Featur...
VLT® AutomationDrive FC 361
10
Danfoss A/S © 03/2019 All rights reserved.
MG06K102
3
3
Содержание VLT AutomationDrive FC 361
Страница 2: ......