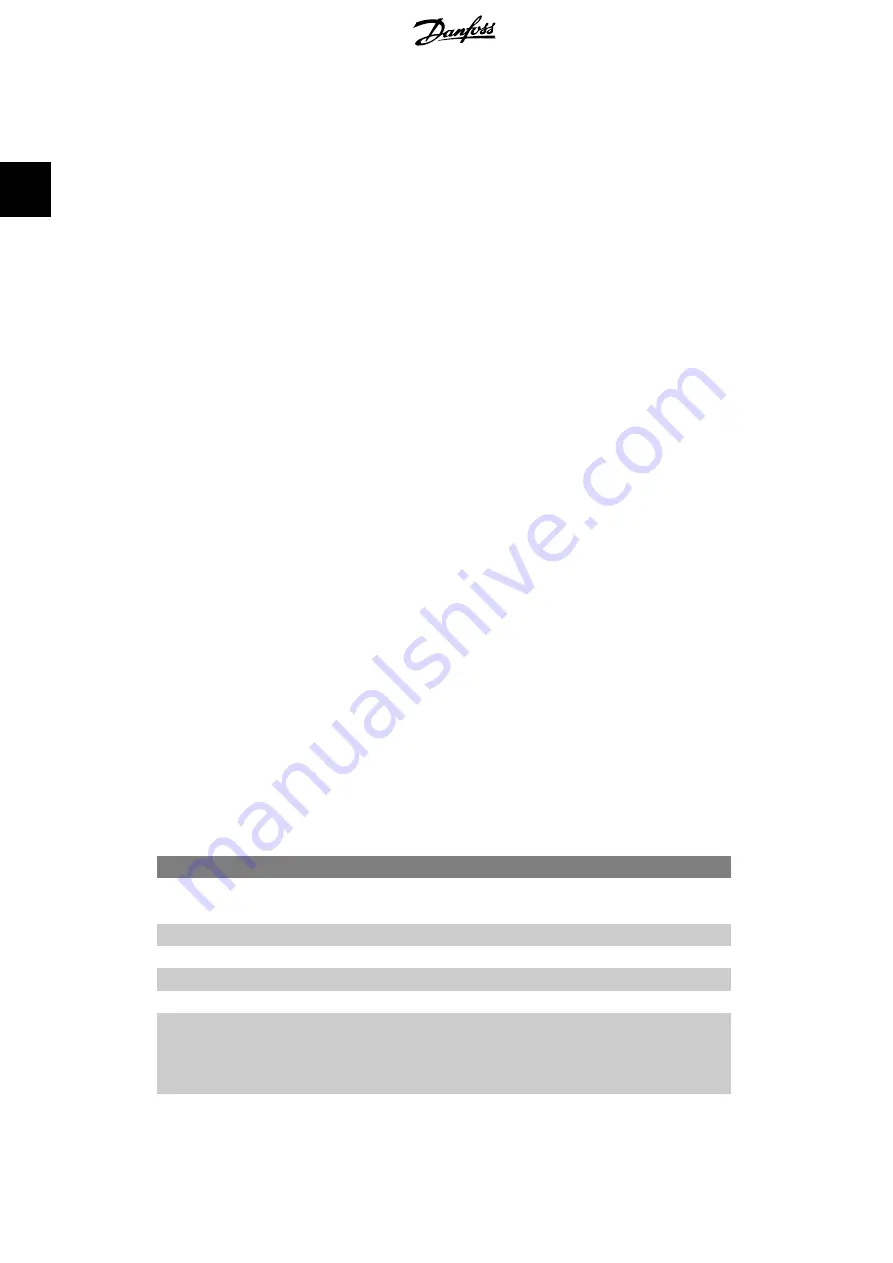
In order to control a modulating device (e.g. a valve motor), this device must be a positioning
servo motor with built-in electronics accepting either a 0-10V or a 0/4-20 mA control signal. The
analog output Terminal 42 or X30/8 (requires an optional card General Purpose Input Output
Module MCB101) can be used for this purpose by selecting one of the options [113]-[115] or
[143-145] Ext. Closed Loop 1-3, in par. 6-50, Terminal 42 Output or par. 6-60, Terminal X30/8
Output.
2.18.2. 21-0* Extended CL Auto-Tuning
The extended PID Closed Loop PID controllers (
par 21-**, Ext. Closed Loop
) can each be auto-
tuned, simplifying and saving time during commissioning, whilst ensuring accurate PID control
adjustment.
To use PID Auto-tuning it is necessary for the relevant Extended PID controller to have been
configured for the application.
A Graphical Local Control Panel (LCP) must be used in order to react on messages during the
autotuning sequence.
Enabling Auto-tuning par 21-09 puts the relevant PID controller into PID Auto-tuning mode. The
LCP then directs the user with on-screen instructions.
PID Auto-tuning functions by introducing step changes and then monitoring the feedback. From
the feedback response, the required values for PID Proportional Gain, par 21-21 for EXT CL 1, par
21-41 for EXT CL 2 and par 21-61 for EXT CL 3 and Integral Time, par 21-22 for EXT CL 1, par
21-42 for EXT CL 2 and par 21-62 for EXT CL3 are calculated. PID Differentiation Time, Par 21-23
for EXT CL 1, par 21-43 for EXT CL 2 and par 21-63 for EXT CL 3 are set to value 0 (zero). Normal /
Inverse, par 21-20 for EXT CL 1, par 21-40 for EXT CL 2 and par 21-60 for EXT CL 3 are determined
during the tuning process.
These calculated values are presented on the LCP and the user can decide whether to accept or
reject them. Once accepted, the values are written to the relevant parameters and PID Auto-tuning
mode is disabled in par 21-09. Depending on the system being controlled the time required to
carry out PID Auto-tuning could be several minutes.
Excessive feedback sensor noise should be removed using the input filter (parameter groups 6*,
5.5* and 26*, Terminal xx Filter Time Constant/Pulse Filter Time Constant xx) before activating
PID Autotuning.
21-00 Closed Loop Type
Option:
Function:
[0]
*
Auto
[1]
Fast Pressure
[2]
Slow Pressure
[3]
Fast Temperature
[4]
Slow Temperature
This parameter defines the application response. The default
mode should be sufficient for most applications. If the relative
application speed is known, it can be selected here. This will
decrease the time needed for carrying out PID Autotuning. The
2. Parameter Description
VLT
®
AQUA Drive Programming Guide
186
MG.20.O2.02 - VLT
®
is a registered Danfoss trademark
2