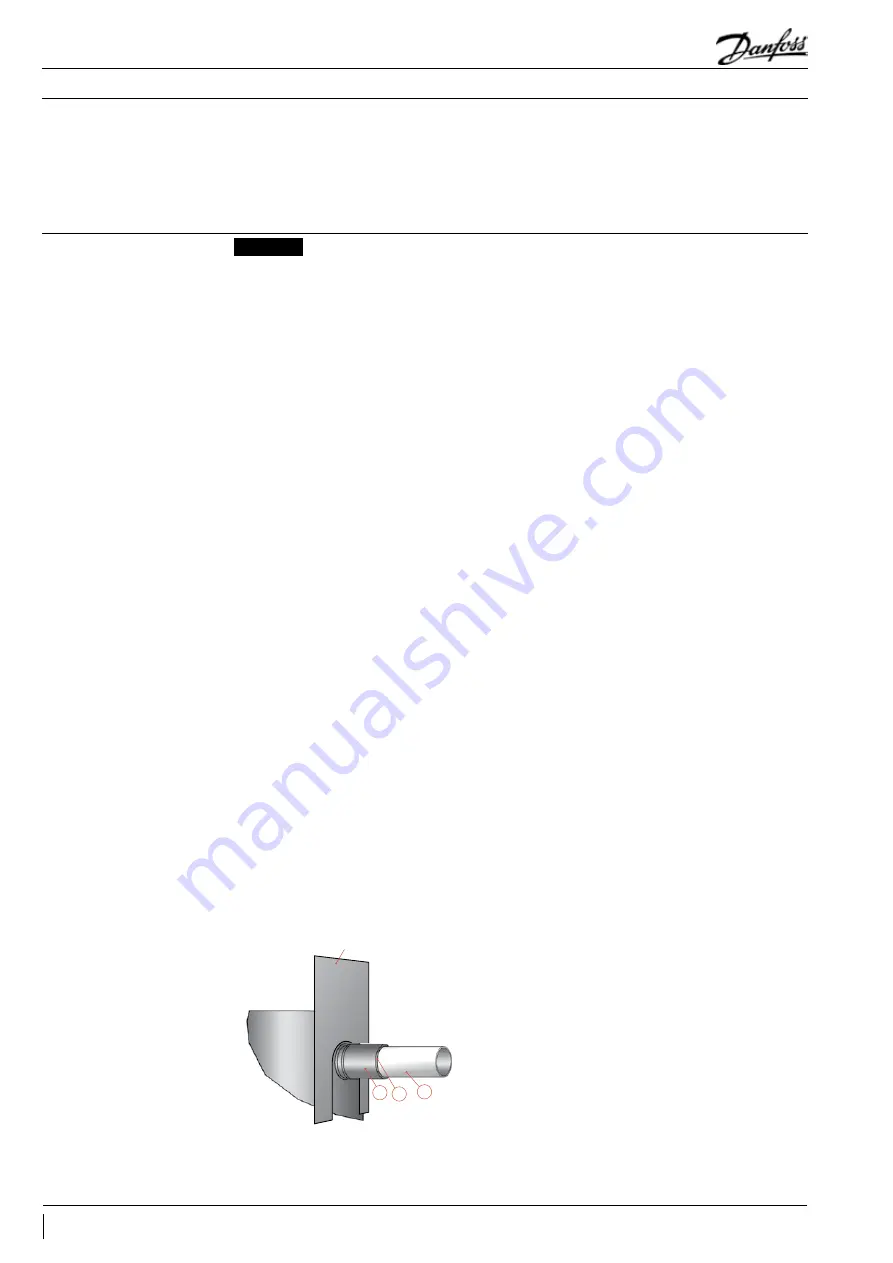
Installation
4.6 Phase sequence
4.7 Brazed connections
Optyma
™
Plus INVERTER units are equipped with
variable speed scroll compressors for which
proper phase sequence is compulsory in order to
secure rotation in right direction and therefore
compression.
The phase sequence has to be secured between
the drive and compressor.
(The phase sequence between network and unit
drive is of no influence on the compressor rotation
direction).
NOTICE
Refrigerant connections, brazing and
flange connections has to be done by a
qualified installer according to EN378.
The unit is supplied with an positive protective
pressure of Nitrogen (1 bar).
The use of substances containing chlorine, mineral
oil or other chemicals is not allowed.
Piping has to be designed to avoid vibrations,
either through flexibility or piping
brackets. Furthermore piping has to be done in
such a way that oil return for the
compressor is ensured and the risk of liquid slug
over in compressor is eliminated.
Only use clean and dehydrated refrigeration grade
copper tubing. Tube-cutting must be
carried out so as not to deform the tubing
roundness and to ensure that no foreign debris
remains within the tubing. Only refrigerant grade
fittings should be used and these must be of
both a design and size to allow for a minimum
pressure drop through the completed assembly.
Follow the brazing instructions bellow. Never drill
holes into parts of the pipe-work where filings
and particles cannot be removed. Even during
installation, if the system is left for
any reasonable period of time (say 1 hour), pipes
should be re-capped to prevent moisture and
contaminant from entering the system.
Liquid/suction tubes are extended from
the condensing unit housing, therefore we
recommend to isolate the housing by using a heat
shield and/or a heat-absorbent compound (e.g.
wet cloth) on the copper tubing. Use a double-
tipped torch.
heat shield
C B
A
For brazing the suction and liquid line
connections, the following procedure is advised:
• Make sure that no electrical wiring is connected
to the compressor.
• Use brazing material with a minimum of 5% silver
content.
• Fit the copper tube into the unit tube.
• Apply heat evenly to area A until the brazing
temperature is reached. Move the torch to
area B and apply heat evenly until the brazing
temperature has been reached there as well, and
then begin adding the brazing material. Move
the torch evenly around the joint, in applying
only enough brazing material to flow the full
circumference of the joint.
• Move the torch to area C only long enough to
draw the brazing material into the joint.
• Remove all remaining flux “once the joint has
been soldered” with a wire brush or a wet cloth.
Remaining flux would cause corrosion of the
tubing. Ensure that no flux is allowed to enter into
the tubing. Flux is acidic and can cause substantial
damage to the internal parts of the system and
compressor.
The polyolester oil used in VLZ compressors
is highly hygroscopic and will rapidly absorb
moisture from the air. Condensing unit must
therefore not be left open to the atmosphere for
a long period of time. Unit fitting plugs shall be
removed just before brazing. Condensing unit
should always be the last component brazed into
the system.
Before eventual unbrazing of the compressor or
any system component, the refrigerant charge
must be removed from both the high- and
low-pressure sides. Failure to do so may result in
serious personal injury. Pressure gauges must be
used to ensure all pressures are at atmospheric
level.
For more detailed information on the appropriate
materials required for brazing or soldering, please
contact the product manufacturer or distributor.
For specific applications not covered herein, please
contact Danfoss for further information.
It is compulsory to braze with a protective
atmosphere of nitrogen inside the piping.
Nitrogen displaces the air and prevents the
formation of copper oxides in the system.
24
FRCC.PC.044.A6.02
Application Guidelines
Содержание Optyma Plus
Страница 2: ......
Страница 22: ...Installation Picture1 Normal wiring Picture2 Emergency wiring 22 FRCC PC 044 A6 02 Application Guidelines...
Страница 41: ......