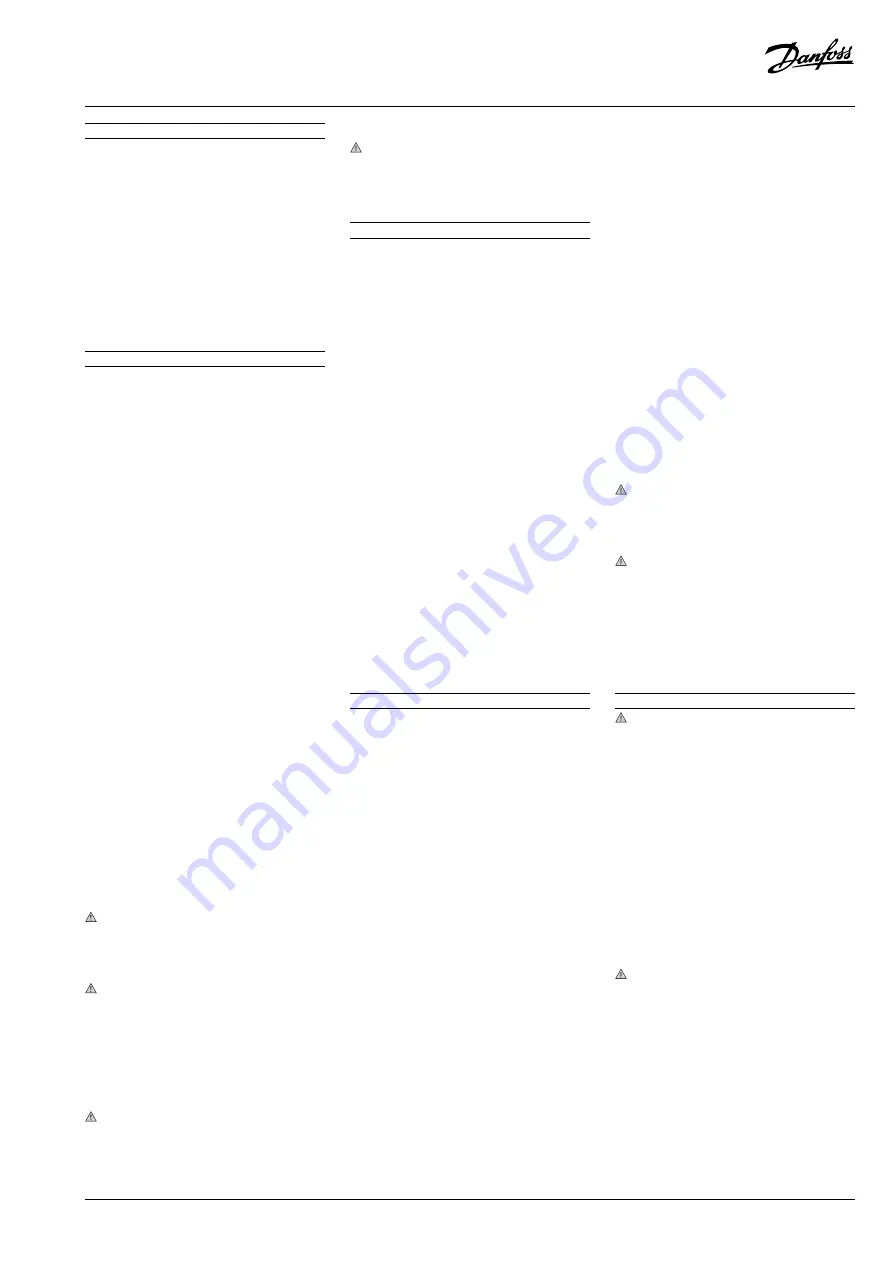
Instructions
AN293820378892en-000101 | 5
© Danfoss | DCS (CC) | 2019.01
Contents
1 - Introduction
2 - Transportation, storage
3 - Safety measures prior to assembly
4 - Assembly
5 - Leak detection
6 - Vacuum dehydration procedure
7 - Electrical connections
8 - Filling the system
9 - Verification before commissioning
10 - Start up
11 - Troubleshooting
12 - Maintenance
13 - Replacement
14 - User advisory
1 - Introduction
These instructions pertain to Bluestar condensing
units used for refrigeration purposes. They are
intended to provide necessary information regar-
ding safety features and proper handling of this
product.
Note that this is a general document for the en-
tire range of condensing units; certain details
therefore may not be applicable to the particular
model you purchased. Please keep your manual
and all relevant information handy for future re-
ference.
• Equipment description: condensing units are
available under different configurations. They
incorporate a compressor and a fan-cooled
condenser mounted on a base frame. In addi-
tion, they may include a liquid receiver, a pres-
sure switch, a connecting box and service valves.
• Approved list of refrigerants:
- The LGHC and LCHC product line (fitted with
Maneurop® NT compressors) can be used with
R404A/R507.
- The MCZC and MGZC product line (fitted
with Maneurop® MTZ compressors) can be used
with R404A, R507 and R134a.
• Note that Maneurop® compressors are filled
with lubricant before leaving the factory:
- The MTZ series with polyolester oil (ref. 175PZ),
- The NTZ series with polyolester oil (ref. 175Z).
These lubricants must not be mixed with one another.
• Condensing units must only be used for their
designed purpose(s) and within their scope of
application (refer to Fig. 1).
Condensing units are delivered under ni-
trogen gas pressure (between 1 and 2 bar) and
hence cannot be connected as is; please refer to
the
«Assembly»
section for further details.
Condensing units are not certified for mobile
and explosion-proof applications. Any use of
flammable refrigerant (e.g. hydrocarbons) or air
is also strictly forbidden.
• Under all circumstances, the EN 378-2:2016 (or other
applicable local regulation) requirement must be ful-
filled.
When pressure tests are required on the sys-
tem, they are to be performed by qualified per-
sonnel, in paying close attention to potential
pressure-related hazards and heeding the pres-
sure limits displayed on the compressor name-
plate or in the application guidelines.
Modifications or alterations to the compres-
sor or receiver (such as brazing on the shell) not
expressly approved by the party responsible for
ensuring compliance could invalidate the user’s
authorization to operate the equipment.
2 - Transportation, storage
• The condensing unit must be handled in the
vertical position (maximum offset from the
vertical: 15°). Should the unit be handled in an
upside-down position, its performance may no
longer be insured.
• Beware that all condensing unit handling must
be carried out with extreme caution to avoid any
shocks. Appropriate and safe lifting equipment
is to be used during handling and unpacking. Be
careful with the condenser’s front surface (note
that the condenser side is indicated on the pac-
kaging).
• Any damage noticed on either the packaging
or the product itself upon reception should be
indicated on a Customer Claim addressed to the
shipping company. The same recommendation
applies to all instances when transport instruc-
tions have not been fully respected.
• Please review the safety instructions printed on
the cardboard packaging before storage.
• Verify that the condensing unit is never stored
in an ambient temperature of below -35°C
(-31°F) or above 50°C (122°F).
• Ensure that the condensing unit and its packa-
ging are not exposed to rain and/or a corrosive,
flammable atmosphere.
3 - Safety measures prior to assembly
• All installation and servicing is to be performed
by qualified personnel in compliance with all
pertinent practices and safety procedures.
• The condensing unit must be located in a
well-ventilated area; air flow through unit shall
not be restricted in any way (refer to Fig.2). Make
sure that the ambient temperature never ex-
ceeds 50°C (122°F) during the off-cycle.
• For outdoor installations, provide a shelter or
use a Danfoss condensing unit housing.
• Make certain that the condensing unit can be
mounted onto a horizontal plane with a maxi-
mum slope of 3°.
• Check that the condensing unit model corres-
ponds to system specifications (capacity, use of
refrigerant, etc.).
• Verify that the power supply corresponds to
compressor and fan motor characteristics (refer
to the condensing unit nameplate for precision).
• Ensure that the refrigerant charging equip-
ment, vacuum pumps, etc. for HFC refrigerant
systems have been specifically reserved for
these refrigerants and never used with other
CFC, HCFC refrigerants.
• Use only clean and dehydrated refrigera-
tiongrade copper tubes as well as silver alloy
brazing material.
• Verify that all system components are appro-
priate (use of refrigerant, etc.), clean and dehy-
drated before being connected to the comple-
ted assembly.
Perform a check on the suction lines: horizontal
sections are to be sloped downwards towards
the compressor. Suction gas velocity must be
high enough to provide for an adequate oil re-
turn.This velocity must be within 8 to 12 m/s in
vertical risers. In horizontal pipes, this velocity
can decrease to 4 m/s. The use of U-trap and
double-suction risers may be required on ver-
tical sections, but not in excess of 4 m unless a
second U-trap system has been fitted (refer to
Fig. 3).
Suction line piping must be insulated in order to
minimize the effects of superheating.
• The piping connected to the compressor must
be configured on the basis of a flexible 3-axis de-
sign to dampen vibrations and designed in such
a way as to prevent free liquid refrigerant migra-
tion and drainage back to the compressor sump.
When installing a liquid receiver or any other
pressure-containing component on the conden-
sing unit, be sure that these components com-
ply with the PED 2014/68/EU.
Make sure the installation is equipped with
high-pressure safety components (e.g. pressure
switch, pressure relief valve) to prevent against the
bursting of pressure-containing components.
• Note that all local and regional regulations and
safety standards, such as EN 378-2:2016, must be
taken into account when designing, connecting
and running the system.
4 - Assembly
The condensing unit’s time of exposure to the
atmosphere during installation shall be held to
a minimum. The condensing unit is fitted with
suction and liquid copper stubs equipped with
shut-off valves to enable connection to the cir-
cuit without ingress of air or moisture in the unit.
Opening the shut-off valves before connection
will cause moisture contamination of the com-
pressor lubricant.
• Rubber grommets can be installed under the
condensing unit base frame, as shown in Fig 4,
to prevent vibration interference from other
operating equipment or machinery and to re-
duce vibration transmission to the supporting
structure.
Before opening the compressor connection
fittings, it is mandatory to connect a 1/4” service
hose to the Schrader fitting on the compressor
shell in order to gradually release the nitrogen
holding charge.
• Ensure that no material enters into the system
while cutting the tubing. Moreover, never drill
holes in the pipe work after installation.
• Avoid flare-type connections and exercise great
care while brazing (use only state-of-the-art
practices); apply a nitrogen gas flow to prevent
oxidation inside the tubing, especially when
HFC refrigerants are being used. All brazing ma-
terial is to contain a minimum of 5% silver.