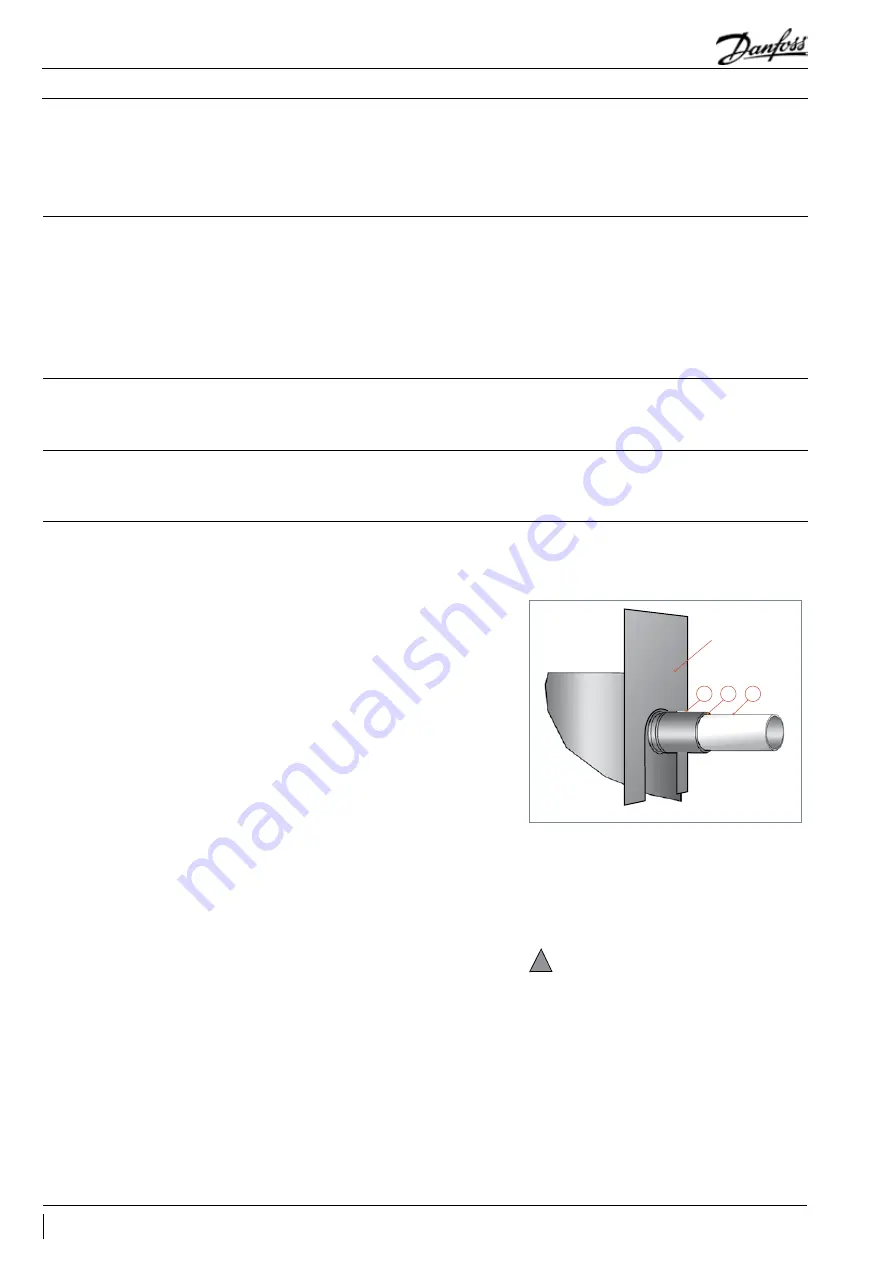
Installation
Compressor holding
charge
Compressor mounting
Maximum inclination from the vertical plane,
while operating must not exceed 7 degrees.
All compressors are delivered with 4 rubber
grommets and metal sleeves. Compressors
must always be mounted with these grommets.
Recommended torque for mounting bolts: 21 Nm
(±1 Nm).
Brazing material
For copper suction and discharge fittings, use
copper-phosphorus brazing material. Sil-Fos® and
other silver brazing materials are also acceptable.
If flux is required for the brazing operation, use
coated rod or flux core wire. To avoid system
contamination, do not brush flux on.
Tube brazing procedure
Do not bend the compressor discharge or suction
lines or force system piping into the compressor
connections, because this will increase
stresses that are a potential cause of failure.
Recommended brazing procedures and material,
are described on following page.
Each compressor is shipped with a nominal dry
nitrogen holding charge between 0.3 and 0.7 bar
and is sealed with elastomer plugs.
Before the suction and discharge plugs are
removed, the nitrogen holding charge must be
released via the suction Schrader valve to avoid
an oil mist blowout. Remove the suction plug
first and the discharge plug afterwards. The plugs
shall be removed only just before connecting the
compressor to the installation in order to avoid
moisture from entering the compressor. When
the plugs are removed, it is essential to keep the
compressor in an upright position so as to avoid
oil spillage.
Compressor connection
When brazing the compressor fittings, do not
overheat the compressor shell, which could
severely damage certain internal components
due to excessive heating. Use of a heat shield
and/or a heat-absorbent compound is highly
recommended. For brazing the suction and
discharge connections, the following procedure
is advised:
• Make sure that no electrical wiring is connected
to the compressor.
• Protect the terminal box and compressor
painted surfaces from torch heat damage (see
diagram).
• Use only clean refrigeration-grade copper
tubing and clean all connections.
• Purge nitrogen through the compressor in order
to prevent against oxidation and flammable
conditions. The compressor should not be
exposed to the open air for extended periods.
• Use of a double-tipped torch is recommended.
• Apply heat evenly to area
A
until the brazing
temperature is reached. Move the torch to
area
B
and apply heat evenly until the brazing
temperature has been reached there as well, and
then begin adding the brazing material. Move
the torch evenly around the joint, in applying
only enough brazing material to flow the full
circumference of the joint.
• Move the torch to area
C
only long enough to
draw the brazing material into the joint, but not
into the compressor.
• Remove all remaining flux once the joint has
been soldered with a wire brush or a wet cloth.
Remaining flux would cause corrosion of the
tubing.
Ensure that no flux is allowed to enter into the
tubing or compressor. Flux is acidic and can cause
substantial damage to the internal parts of the
system and compressor.
The PVE oil used in MLZ compressors is highly
hygroscopic and will rapidly absorb moisture
from the air. The compressor must therefore not
be left open to the atmosphere for a long period
of time. The compressor fitting plugs shall be
removed just before brazing the compressor.
!
Before eventual unbrazing the
compressor or any system component, the
refrigerant charge must be removed from
both the high and low pressure sides. Failure
to do so may result in serious personal injury.
Pressure gauges must be used to ensure all
pressures are at atmospheric level.
For more detailed information on the appropriate
materials required for brazing or soldering, please
contact the product manufacturer or distributor.
For specific applications not covered herein,
please contact Danfoss for further information.
Heat shield
C
B
A
32
FRCC.PC.035.A5.02
Application Guidelines
Single compressors
Содержание MLM116
Страница 1: ...Danfoss Scroll for Refrigeration MLM MLZ116 50Hz R404A R22 Application guidelines http cc danfoss com ...
Страница 2: ......
Страница 3: ...Content Single compressors 4 Manifold compressors 39 3 FRCC PC 035 A5 02 Application Guidelines ...
Страница 58: ......
Страница 59: ......