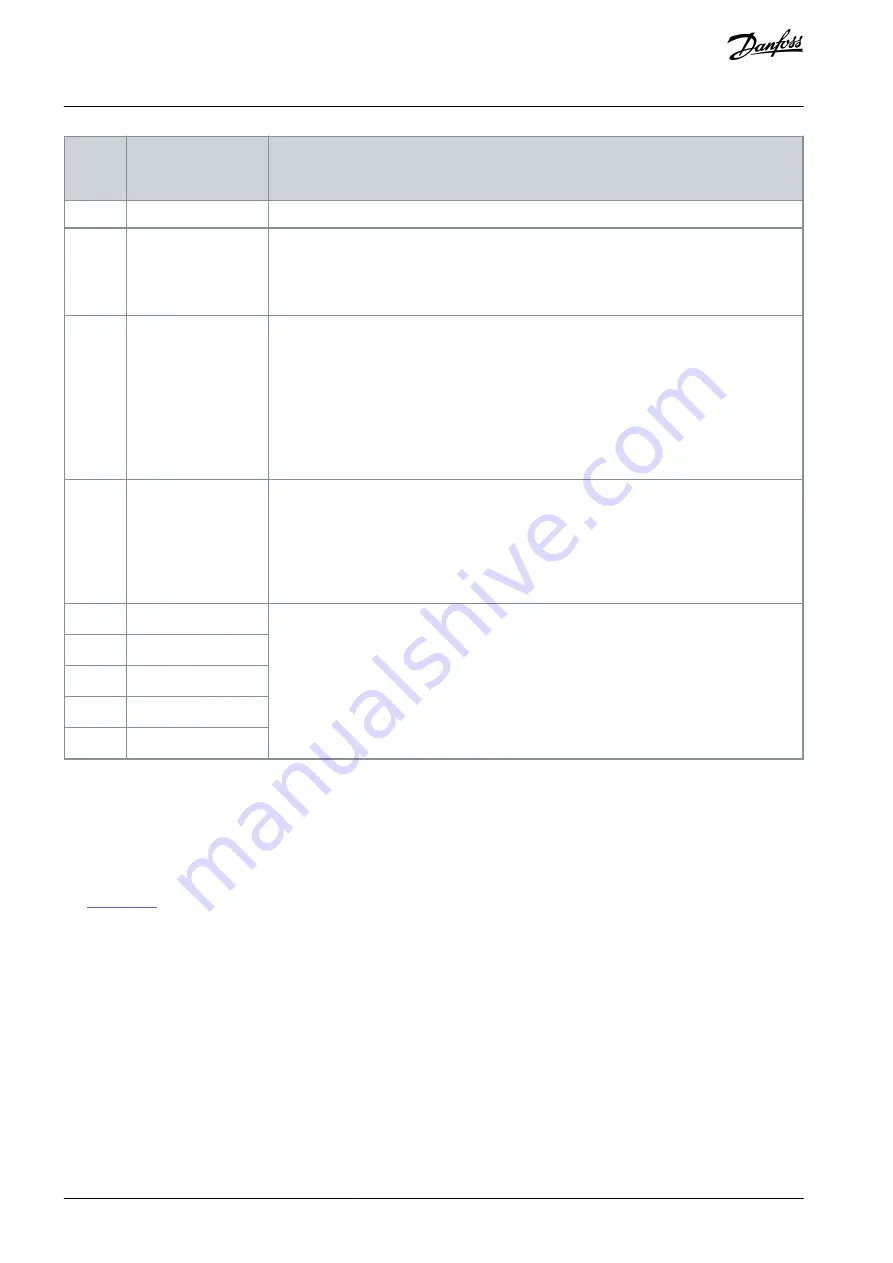
•
•
•
•
•
•
•
•
•
Bit
Num-
ber
Name
Description
0 = There are no warnings.
8
Speed=reference/
Speed<>reference
1 = The present motor speed matches the present speed reference within a given tolerance.
The tolerance is product specific.
0 = The motor runs, but the present speed is different from the present speed reference. It
could, for example, be the case while the speed ramps up/down during start/stop.
9
Bus control/Local op-
eration
1 = The device is controlled and reacting to I/O and Process data
0 = The device does not react on commands from fieldbus, because of one of the following
reasons:
CTW bit 10 = 0
HMI is in local mode.
MyDrive® Insight has taken control.
Control places do not include fieldbus.
10
Frequency limit
ok/Out of frequency
limit
1 = The output frequency is within the defined motor limits.
0 = The output frequency has exceeded the defined motor limits given by parameters.
The speed limits are set by parameters:
P 5.8.3.4 High Speed Warning
P 5.8.3.9 Low Speed Monitor Limit
11
User defined
These bits enable mapping application functionality of the drive to the status word. Map-
ping is done through parameters. For more information, refer to the application guide.
12
User defined
13
User defined
14
User defined
15
User defined
2.4.3 PROFIdrive State Machine
In the PROFIdrive control profile, the control bits perform different functions:
0–3 perform the basic start-up and power-down functions.
4–10 perform application-oriented control.
12–15 can be configured for different purposes.
See
bit indicates the actual state. The black dots indicate the priority of the control signals. Fewer dots indicate lower priority, and more
dots indicate higher priority.
The general state diagram is defined in the PROFIdrive standard.
AQ408626183394en-000101 / 136R0280
14 | Danfoss A/S © 2023.06
Product Overview
iC7 Series PROFINET
Operating Guide