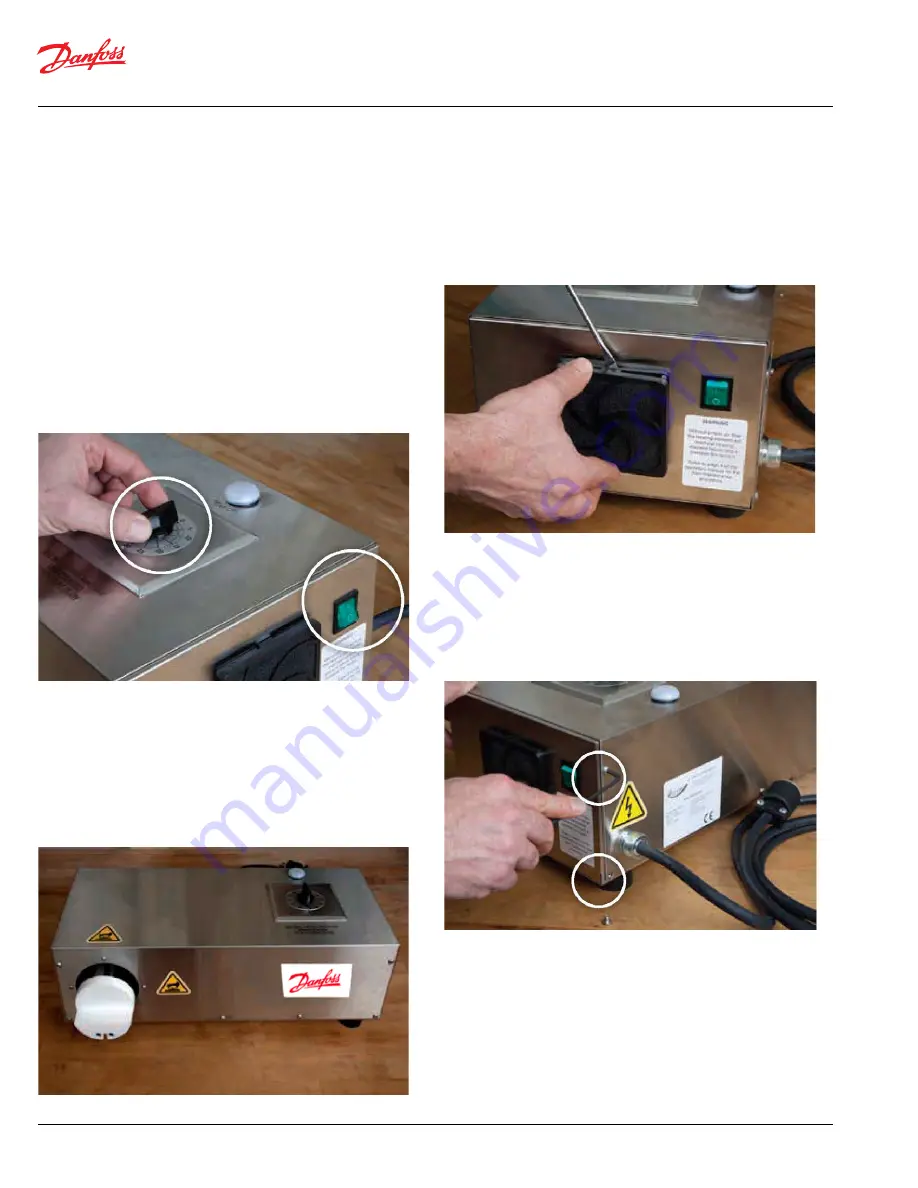
Danfoss
FT1555-BM bench mount capping machine Operator’s Manual
8 | © Danfoss FT1555-BM bench mount capping machine Operator’s Manual | 2023.03.
AQ445452814730en-000101
Maintenance
Bi-monthly cleaning of the Danfoss FT1555-BM Capping System
Intake Air Filter and Grill is vital in maintaining correct operating
temperatures and function of the heating element. Proper air flow
through the system will prevent the element from over heating
which can cause internal damage and possible fire hazard. Airborne
contaminates varies from location to location, and it is imperative
that the Air Intake Filter and Grill is cleaned every two months at a
minimum.
Step 1:
Turn the timer to “0” position and turn off the main power switch
and disconnect the FT1555-BM Capping System from the power
source. (See Figure 11).
Step 2:
Visually inspect the Capping System for signs of overheating
i.e. discoloration of the stainless steel cover, warning labels,
discoloration or cracking of the plunger or deformation of the
rubber mounts. (See Figure 12).
Step 3:
Pry and remove the black plastic filter retainer on the back of the
switch plate and remove the foam filter. Wash the filter in warm
soap and water and dry completely. (See Figure 13).
Step 4:
Using a 1/8” hex key wrench remove four 10-32 x 1/4” button head
cap screws from the main switch end plate, two in the front and
two in the back. (See Figure 14).
Figure 11
Figure 12
Figure 13
Figure 14