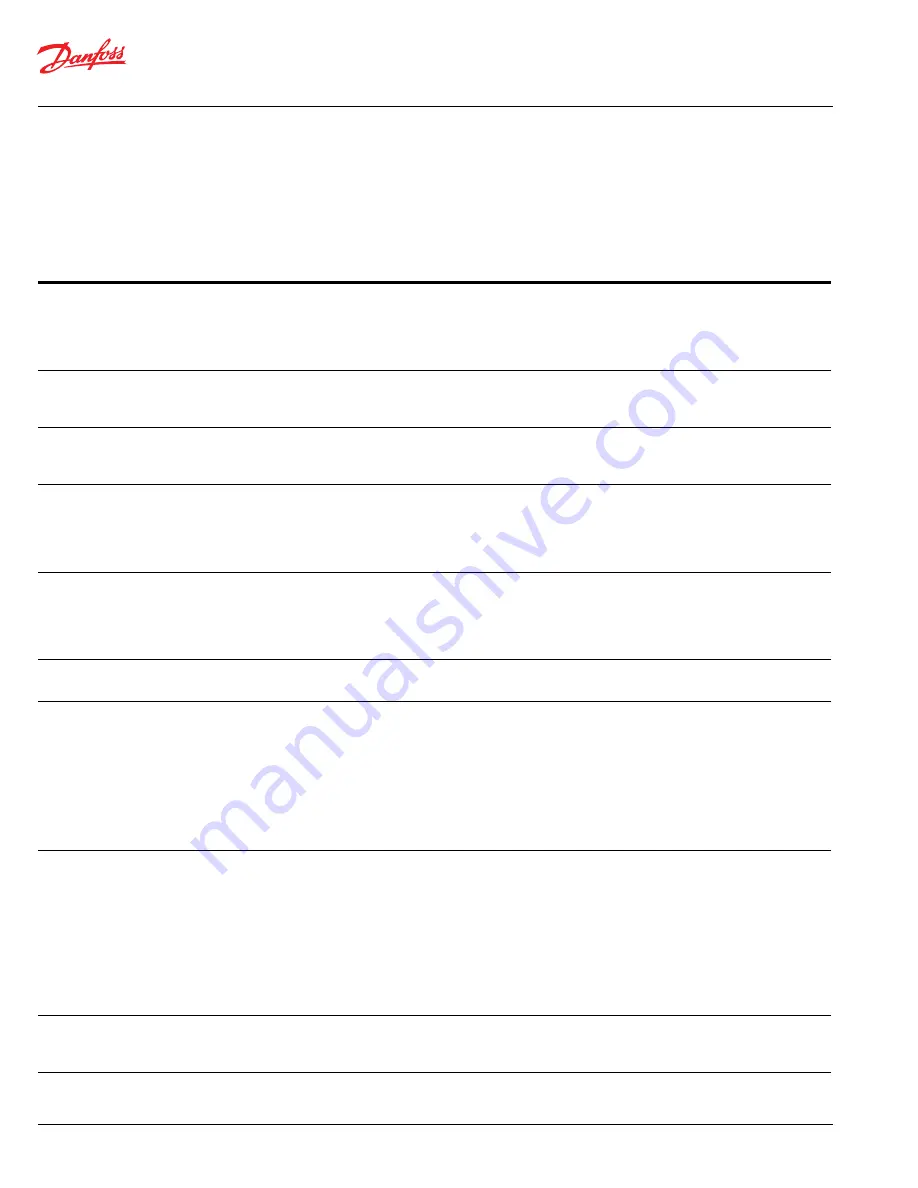
© Danfoss
FT1380 Crimp Machine Operator’s Manual
10 | © Danfoss FT1380 Crimp Machine Operator’s Manual | 2022.12.
AQ435955684211en-000101
Troubleshooting Tips
Remember:
The electric motor only runs during the crimping process. The motor energizes when the crimp switch is pressed and de-energizes when the
crimp switch is released or when the crimp cycle is completed. While retracting, the hydraulic dump valve is energized. When the valve is energized, oil
flow is directed from the pump to the cylinder. When the valve is de-energized, oil flows from the cylinder back to the reservoir.
If the symptom appears to be solely pump or cylinder related, refer to the ENERPAC Repair Parts Sheets.
Any electrical checks must be performed by a qualified electrician.
Symptom
Possible
Cause Corrective Action
Pump will not start
•
No power or wrong voltage
•
Make sure that the unit is plugged in.
•
Make sure that the power source is on.
•
Make sure that the power voltage is correct.
•
Check for loose wires on the circuit board.
•
Check for loose wires on the CRIMP switch.
Motor stalls under load
•
Low voltage
•
Verify that the branch circuit conforms to the electrical
schematics on Page 13 of this manual.
•
Remove any extension cords.
Electric valve will not operate
•
No power or wrong voltage
•
Low voltage
•
Check for loose wires on the circuit board.
•
Check for loose wires on the CRIMP switch.
•
Make sure that the power voltage is correct.
Pump fails to build pressure
•
External leak in system
•
Internal leak in pump
•
Internal leak in valve
•
Internal leak in system component
•
Wipe away spilled oil, and locate the source of leak. If
the hose assembly is leaking, tighten or replace it. If
the pump or cylinder is leaking, refer to the ENERPAC
Repair Parts Sheets. Slight oil seepage of the cylinder
is normal.
Pump builds less than full pressure
•
Relief valve set low
•
External system leak
•
Internal leak in pump
•
Internal leak in valve
•
Internal leak in system component
•
Refer to the ENERPAC Repair Parts Sheets for possible
adjustment or leakage repair.
Pump builds full pressure, but cylinder
does not move
•
Tie rods may be binding
•
Flow to cylinder blocked
•
Replace the tie rods.
•
Refer to the ENERPAC Repair Parts Sheets.
Cylinder will not return
•
Valve malfunction
•
Restricted/blocked
•
Tie rods may be binding
•
Die cage may be binding
•
Refer to the ENERPAC Repair Parts Sheet for valve or
cylinder repair.
•
Replace the tie rods.
•
Check the die cage and crimp ring for damage, and
repair or replace them if necessary.
•
Lubricate the die cage per the maintenance
procedures on Page 9.
•
Lubricate the tie rod bushings per the maintenance
procedures on Page 9.
Crimp diameters change
•
Incorrect hose/fitting combination
•
Incorrect die cage
•
Die cage or crimp insert damage
•
Transducer is loose
•
Loose crimp machine components
•
External damage to crimp machine
•
Insufficient lubrication on dies
•
Verify the correct hose/fitting combination.
•
Verify the correct die cage.
•
Repair or replace the damaged components.
•
Tighten the transducer and brackets, and then
recalibrate them if necessary.
•
Tighten any loose bolts or screws.
•
Lubricate the die cage per the maintenance
procedures on Page 9.
•
Lubricate the tie rod bushings per the maintenance
procedures on Page 9.
DISPLAY blinks
•
Loose or broken wires
•
Tighten any wires that may have become loose on
the circuit board, pump electrical enclosure, or CRIMP
switch.