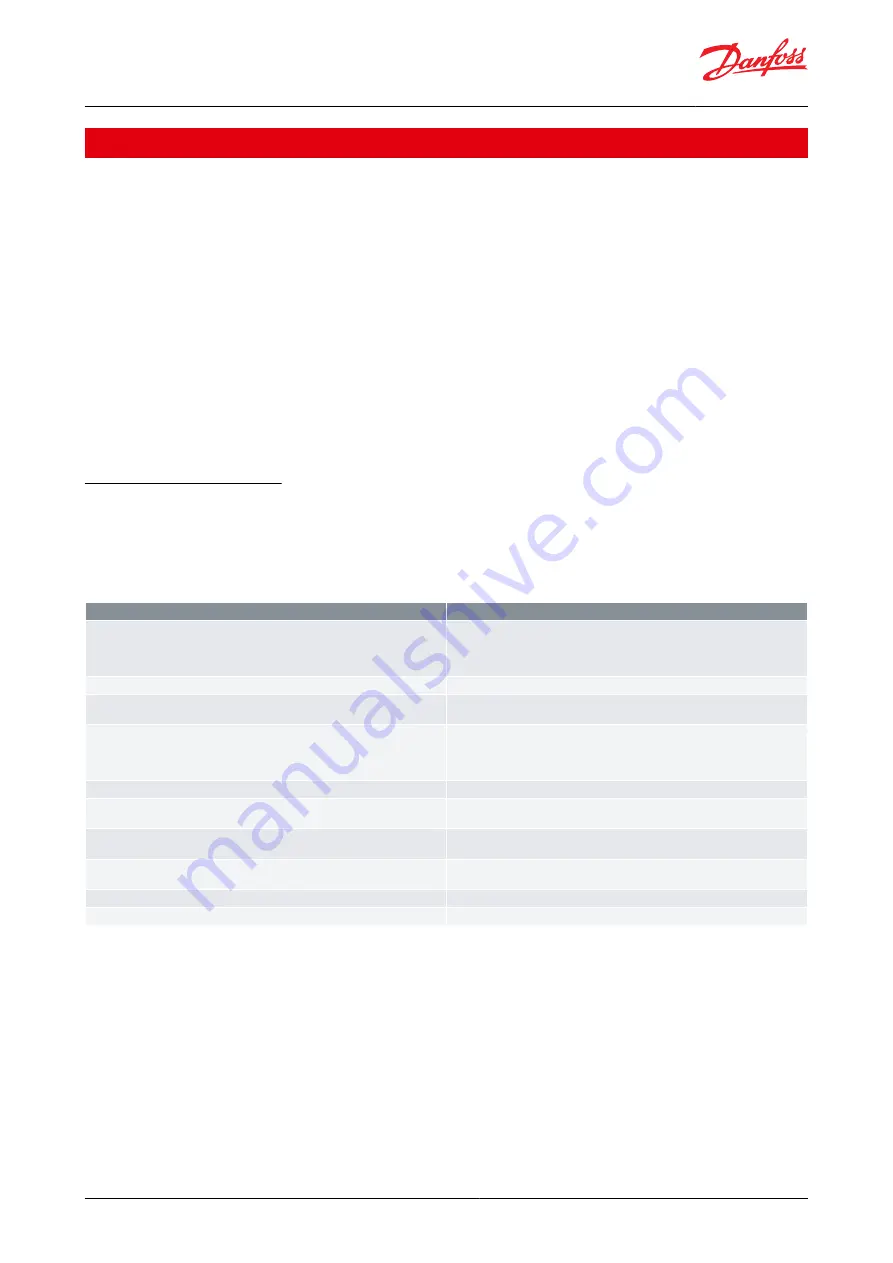
Configuration
This section represents a guide on how to configure the EIM 365 series controller for various application. Also, the
configuration for other features, like startup, defrost and protection are also explained. The parameters are given in
a form of a parameter table, where the most important parameters in a mode are shown and described.
The EIM 365 controller has a default configuration to be operated via Modbus and to rely on a constant connection
to the master controller of the system it is located within. In this configuration the master controller reads the
readout registers from the EIM 365 and uses the parameters to change the control behavior of the EIM 365 (see
Parameter list).
The following control modes are available:
• Superheat control
• Manual Control
• Defrost
• Te Control for dehumidifying
• Protection features
Superheat Control Mode
For superheat control, one temperature sensor S2, and one pressure sensor Pe are needed. The actual superheat is
calculated based on these two sensor readings, and the controller will adjust the OD of the valve to bring the
superheat to the desired reference. If superheat is too low the flow in the expansion is decreased and superheat will
be higher and vice versa
Table 6: Quick Guide for setting the controller in Superheat control mode
Features
Description
EnablingRegulation control ON/Off switch (optional)
HwMainSwitch= 1 (default is 0, i.e S4 sensor)
Forstandalone configuration it is recommended to enable Regulation control
ON/Off switch in order to control start/ stop regulation when needed, otherwise
the controller will start regulating when controller is powered up.
Select Refrigerant
O30= 1 - 42 (default value is 20 i.e R407C)
Select startup method
Startup mode:
1: fixed OD, 2: P-control
Select superheat reference calculation method
n21 SH mode:
1: MSS; 2: LoadAp
Note: EIM can be set to Fixed SH mode by using LoadAp and setting Max SH =
Min SH
Select valve setting
n03=Valve type
Define pressure sensor rangein bar absolute (x10)
o20 = Min. Transducerpressure
o21 =Max.Transducer pressure
Define min/max superheat
N09= max. superheat
n10= min. superheat
Define MOP (optional)
n11= maximum operating pressure (default is 12.5 bar absolute, max. 200 = MOP
off)
Set force opening of the valve (optional)
Start OD% (n17 )Start Up time (n15)
To start the superheat control
Set r12= ON
NOTE:
Make sure that r12 = 0 (OFF) for changing the settings.
Configuring the superheat control
The superheat controller is a PI controller, The time constant for the superheat control can be changed by setting
“Tn SH”.The alpha value is the design time constant and should be in reasonable proximity to the time constant of
theevaporator. A large alpha value means a slow reaction, a small alpha value means a fast reaction.If the superheat
drops below “n22 SH close”, the controller will close the valve faster to avoid the risk of liquid in the compressors
suction line.
In superheat mode the controller will control the superheat to be stable and closer to the superheat reference. The
Superheat reference is calculated based on following different methods:
Superheat controller, type EIM 365 (PV01)
© Danfoss | Climate Solutions | 2022.09
BC415322248492en-000101 | 12