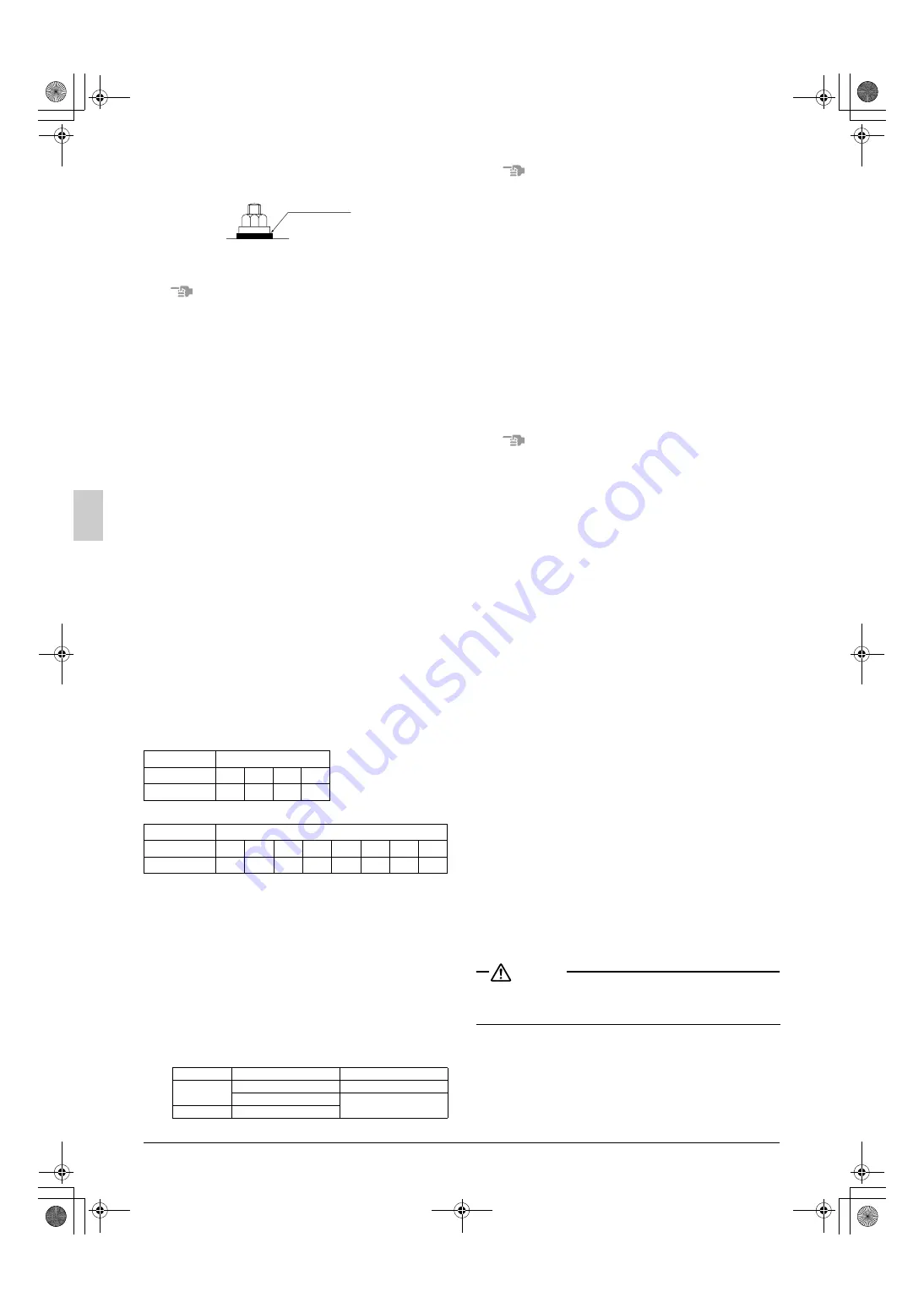
5
English
•
For anti-corrosion type use nuts with resin washers. If the paint on
nut connections comes off, the anti-corrosion effect may
decrease.
6.
REFRIGERANT PIPING
Note
•
All field piping must be installed by a licensed refrigeration tech-
nician and must comply with relevant local and national regula-
tions.
•
After piping work is complete, do not under any circumstances
open the shutoff valve until “7. FIELD WIRING” and “10. CHECK-
ING OF DEVICE AND INSTALLATION CONDITIONS” are com-
plete.
•
Do not use flux when brazing the refrigerant piping. Use the phos-
phor copper brazing filler metal (BCuP-2: JIS Z 3264/B-Cu93P-
710/795: ISO 3677) which does not require flux.
(Flux has extremely harmful influence on refrigerant piping sys-
tems. For instance, if the chlorine based flux is used, it will
cause pipe corrosion or, in particular, if the flux contains fluo-
rine, it will damage the refrigerant oil.)
6-1 Selection of piping material and Refrigerant
branching kit
•
Use only pipes which are clean inside and outside and which do
not accumulate harmful sulfur, oxidants, dirt, cutting oils, mois-
ture, or other contamination. (Foreign materials inside pipes
including oils for fabrication must be 30mg/10m or less.)
•
Use the following items for the refrigerant piping.
Material
: Jointless phosphor-deoxidized copper pipe
Size
: See “6-5 Example of connection” to determine the cor-
rect size.
Thickness
: Select a thickness for the refrigerant piping which
complies with national and local laws.
Refrigerant pipe (Gas pipe and Liquid pipe) and refrigerant
branch must meet the condition of design pressure 3.3MPa.
If it is not possible to confirm, use the refrigerant branch kit
selected with “6-5 Example of connection”.
Existing pipes must meet the condition of design pressure
3.3MPa.
Specifically, to confirm that there are no corrosion and the pipe
thickness must not be less than the smallest thickness below.
Temper grade (O type, 1/2H type) in the table indicate the
material types specified in JIS H 3300.
(unit: mm)
* In case of bending 3×D or more (D: O.D. of refrigerant pipe)
(unit: mm)
•
For piping work, follow the maximum tolerated length, difference
in height, and length after a branch indicated in the
“6-5 Example
of connection”
.
•
A refrigerant branching kit (sold separately) is needed for piping
branches and connection of piping between outdoor unit (in case
of multi system).
Use only separately sold items selected specifically according to
the refrigerant branch kit selection in the
“6-5 Example of con-
nection”
.
6-2 Protection against contamination
when installing pipes
Protect the piping to prevent moisture, dirt, dust, etc. from
entering the piping.
Note
Exercise special caution to prevent dirt or dust when passing pip-
ing through holes in walls and when passing pipe edges to the
exterior.
6-3 Pipe connection
•
Be sure to perform nitrogen permutation or nitrogen blow
when brazing.
(Refer to figure 10)
Brazing without performing nitrogen permutation or nitrogen
blow into the piping will create large quantities of oxidized film
on the inside of the pipes, adversely affecting valves and com-
pressors in the refrigerating system and preventing normal
operation.
(Refer to figure 10)
1.
Refrigerant pipe
2.
Location to be brazed
3.
Nitrogen
4.
Taping
5.
Handy valve
6.
Regulator
•
The pressure regulator for the nitrogen released when doing
the brazing should be set to 0.02 MPa (about 0.2kg/cm
2
:
Enough to feel a slight breeze on your cheek).
Note
Do not use anti-oxidants when brazing the pipe joints.
Residue can clog pipes and break equipment.
6-4 Connecting the refrigerant piping
1.
Direction to bring out the pipes
The local interunit piping can be connected either forward or to
the sides (taken out through the bottom) as shown in the figure 11.
(When passing out through the bottom, use the knock hole in the
bottom frame.)
(Refer to figure 11)
1.
Left-side connection
2.
Front connection
3.
Right-side connection
Precautions when knocking out knock holes
•
Open knock hole in the base frame by drilling the 4 concave
around it with a 6mm bit.
(Refer to figure 12)
(Refer to figure 12)
1.
Knock hole
2.
Drill
3.
Concave section
•
Be sure to avoid damaging the casing
•
After knocking out the holes, we recommend you remove any
burrs and paint them using the repair paint to prevent rusting.
•
When passing electrical wiring through the knock holes, protect
the wiring with a conduit or bushings, making sure not to damage
the wiring.
2.
Removing Pinch Piping
•
When connecting refrigerant piping to an outdoor unit, remove
the pinch piping.
(Refer to figure 13)
•
Pinch piping should be removed using the procedure in the fig-
ure 13.
(Refer to figure 13)
1.
Shutoff valve (liquid side · gas side)
2.
Service port
3.
Pinch piping
4.
Procedure 1:
Confirm the shutoff valve is closed.
5.
Procedure 2:
Connect a charge hose to the service port of the liquid
side and gas side shutoff valves and remove the gas
from the pinch piping.
6.
Procedure 3:
After removing the gas from the pinch piping, dissolve
the brazing using a burner and remove the pinch piping.
CAUTION
After removing the gas, remove the pinch piping.
Any gas remaining inside may blow off the pinch piping when you dis-
solve the brazing, causing damage.
3.
Connecting refrigerant piping to outdoor units
<In case of single system: Q8~16 type>
(Refer to figure 14)
1.
If connected to the front
2.
When connected at lateral side (bottom)
3.
Remove the shutoff valve cover to connect.
Temper grade
O type
outer diameter
φ
6.4
φ
9.5
φ
12.7
φ
15.9
smallest thickness 0.4*
0.5*
0.7*
0.9*
Temper grade
1/2H type
outer diameter
φ
19.1
φ
22.2
φ
25.4
φ
28.6
φ
31.8
φ
34.9
φ
38.1
φ
41.3
smallest thickness
0.6
0.6
0.7
0.8
0.9
1.0
1.1
1.1
Place
Installation period
Protection method
Outdoor
More than a month
Pinch the pipe
Less than a month
Pinch or tape the pipe
Indoor
Regardless of the period
Resin washers
01_EN_3P226891-13Q.fm Page 5 Thursday, December 2, 2010 10:15 AM