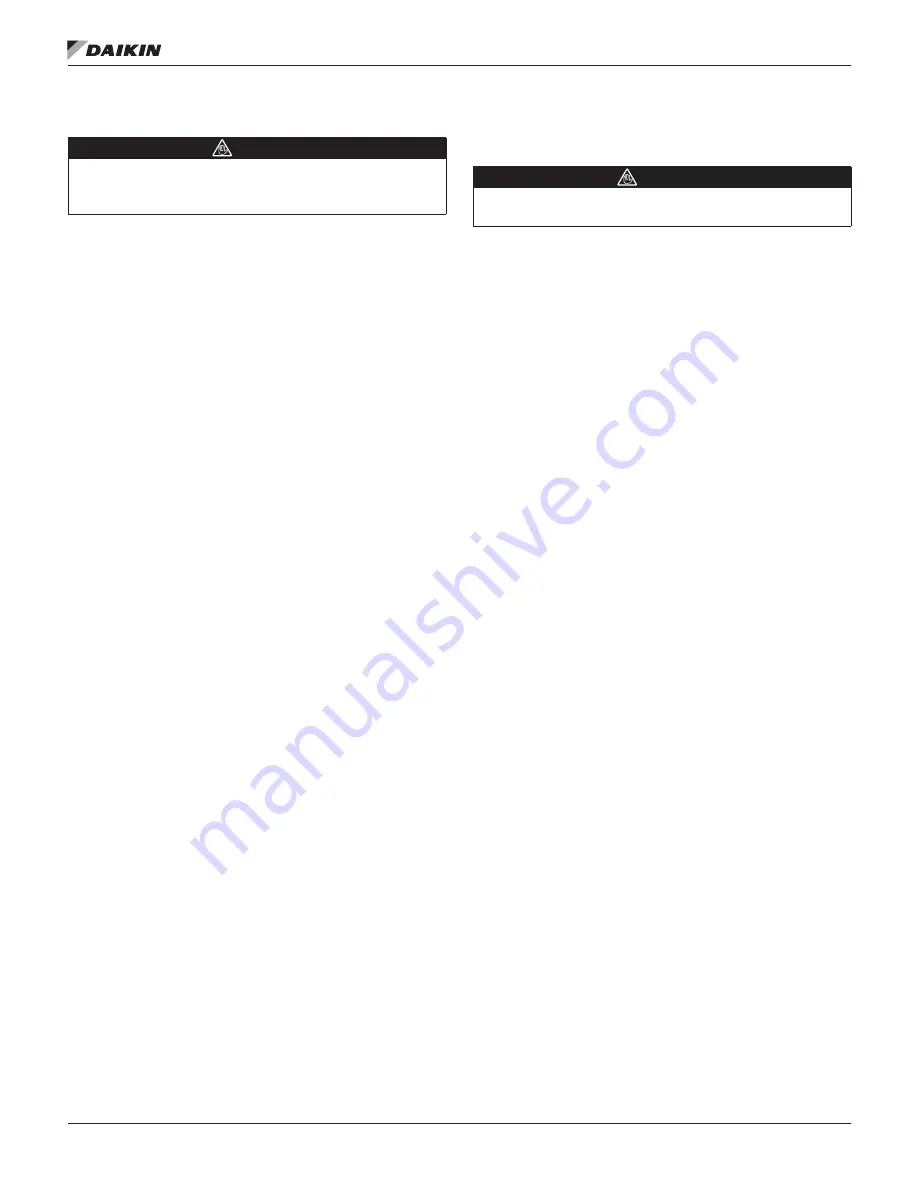
IM 893-10 • ROOFPAK SINGLEZONE UNITS 136 www.DaikinApplied.com
M
aInTenanCe
Refrigerant Charge
WARNING
Potential severe loss of charge may occur if the high refrigerant
pressure switch is repla ed before reclaiming the refrigerant.
Replace switch after reclaiming refrigerant.
The unit nameplate references proper charge for each RPS/
RDT refrigerant circuit in case a full charge must be added
to the unit. Verify these values using
.
for RFS/RCS units.
The micro-channel condenser requires much less charge than
traditional fin tube condensers. This means there is 35% less
charge to recover when servicing the refrigeration circuit, but
the condenser will not hold a high percentage of the charge.
The impact on service is as follows:
• Positive impact - the replacement refrigerant portion of
service cost will be less
• Positive impact - it takes less time to reclaim the entire
charge or the high side portion of the system.
• Negative impact - it takes more time to reclaim the low
side portion of the system because you cannot first
pumpdown most to the high side.
The micro-channel condenser coil design does not contain
the internal volume to support the pumpdown of the entire
unit charge into the condenser coil. To aid in the removal
of refrigerant from the system, a Schrader valve port with a
core has been provided on the liquid line, ahead of the liquid
line shut-off valve. The port is intended for connecting to a
suitable (and approved) storage container while using the
unit compressor(s) to pump liquid refrigerant into a storage
container.
The compressors can be isolated for servicing if the unit has
been ordered with the optional discharge and suction ball
valves. These service ball valves, ¼ʺ Schrader port—standard
option, aid with recovering, evacuating and charging when
servicing a compressor.
Cleaning Option E Coated Coils
WARNING
Prior to cleaning the unit, turn off and lock out the main power
switch to the unit and open all access panels.
The following cleaning procedures are recommended as part
of the routine maintenance activities for Option E Coated Coils.
Documented routine cleaning of Option E Coated Coils is
required to maintain warranty coverage.
Remove Surface Loaded Fibers
Surface loaded fibers or dirt should be removed prior to water
rinse to prevent further restriction of airflow. If unable to back
wash the side of the coil opposite that of the coils entering air
side, then surface loaded fibers or dirt should be removed with
a vacuum cleaner. If a vacuum cleaner is not available, a soft
non-metallic bristle brush may be used. In either case, the tool
should be applied in the direction of the fins. Coil surfaces can
be easily damaged (fin edges bent over) if the tool is applied
across the fins.
NOTE:
Use of a water stream, such as a garden hose,
against a surface loaded coil will drive the fibers and
dirt into the coil. This will make cleaning efforts more
difficult. Surface loaded fibers must be completely
removed prior to using low velocity clean water rinse.
Periodic Clean Water Rinse
A monthly clean water rinse is recommended for coils that are
applied in coastal or industrial environments to help to remove
chlorides, dirt and debris. An elevated water temperature (not
to exceed 130ºF) will reduce surface tension, increasing the
ability to remove chlorides and dirt. Pressure washer PSI must
not exceed 900 psig and the nozzel should remain at leat 1
foot from the coil to avoid damaging fin edges.
Routine Quarterly Cleaning of Option E Coated
Coil Surfaces
Quarterly cleaning is essential to extend the life of an Option
E Coated Coil and is required to maintain warranty coverage.
Coil cleaning shall be part of the unit’s regularly scheduled
maintenance procedures. Failure to clean an Option E Coated
Coil will void the warranty and may result in reduced efficiency
and durability in the environment.
For routine quarterly cleaning, first clean the coil with the
below approved coil cleaner (see approved products list
under
section). After cleaning
the coils with the approved cleaning agent, use the approved
chloride remover (
revitalize the unit.
Содержание RDT
Страница 60: ...IM 893 10 ROOFPAK SINGLEZONE UNITS 60 www DaikinApplied com Wiring Diagrams Figure 64 VFD Control SAF and RAF...
Страница 61: ...Wiring Diagrams www DaikinApplied com 61 IM 893 10 ROOFPAK SINGLEZONE UNITS Figure 65 VAV Control Inputs...
Страница 65: ...Wiring Diagrams www DaikinApplied com 65 IM 893 10 ROOFPAK SINGLEZONE UNITS Figure 67 Electric Heat Control...