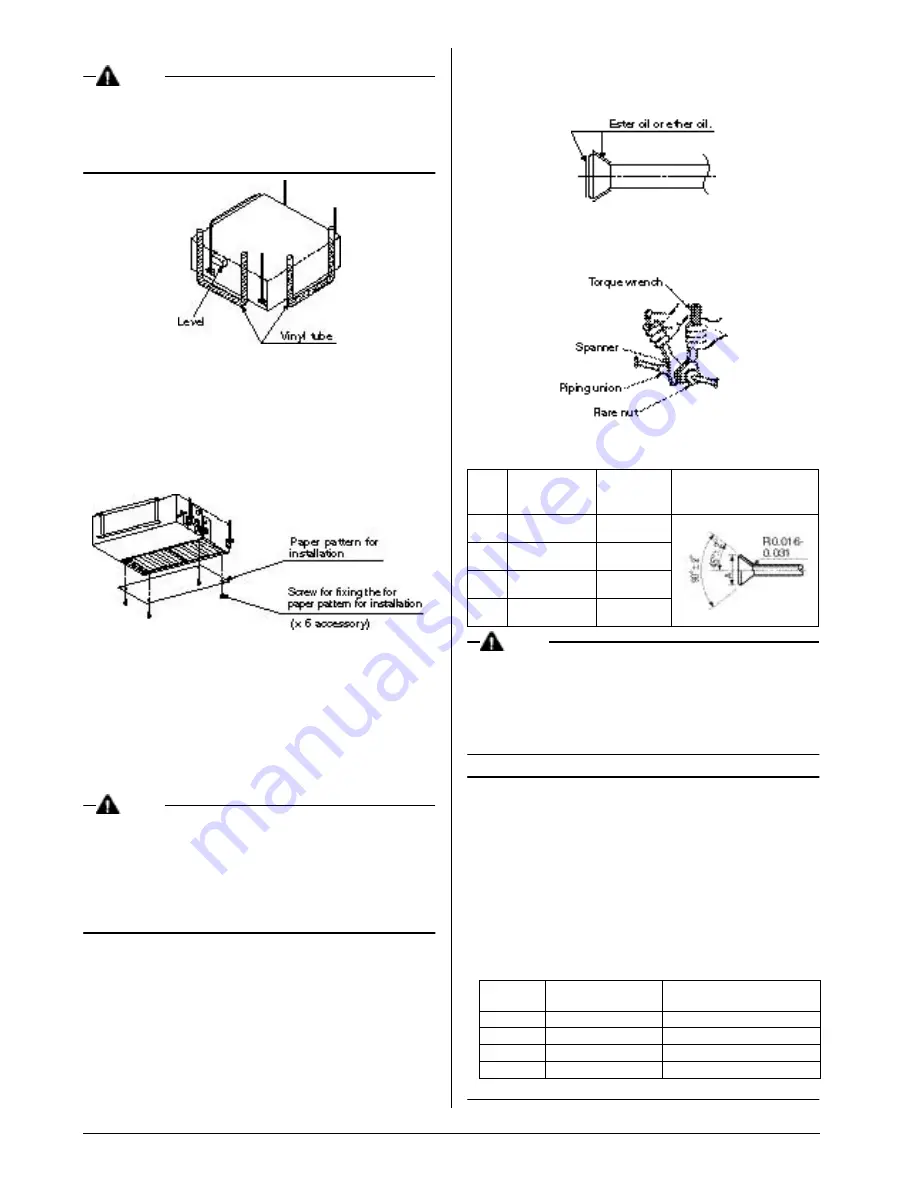
13
(2) Check the unit is horizontally level.
NOTE
• The indoor unit is equipped with a built-in drain pump
and float switch. At each of the unit’s 4 corners, verify
that it is level by using a level or a water-filled vinyl tube.
(If the unit is inclined against condensate flow, the float
switch may malfunction and cause water to drip.)
(3) Tighten the upper nut.
(4) Fix the paper pattern for installation.
• The paper pattern for installation corresponds with the
measurements of the ceiling opening. Consult the builder
for details.
• Attach the paper pattern for installation to the unit with the
screws as shown in the drawing.
The paper pattern for installation is marked for 3 types of ceil-
ing openings. Read the notations carefully when installing.
6. REFRIGERANT PIPING WORK
6-1
GENERAL INSTRUCTIONS
• For refrigerant piping of outdoor units, see the installation man-
ual attached to the outdoor unit.
• Before refrigerant piping work, check which type of refriger-
ant is used. Proper operation is not possible if the types of
refrigerant are not the same.
• The outdoor unit is charged with refrigerant.
NOTE
• Use a pipe cutter and flare suitable for the type of refrigerant.
• To prevent dust, moisuture or other foreign matter from infil-
trating the tube, either pinch the end or cover it with tape.
• Do not allow anything other than the designated refrigerant
to get mixed into the refrigerant circuit, such as air, etc. If any
refrigerant gas leaks while working on the unit, ventilate the
room thoroughly right away.
6-2
Connecting the refrigerant piping
• When connecting the flare nut, coat the flare both inside and
outside with ester
oil
or
ether
oil and initially tighten by hand 3
or 4 turns before tightening firmly.
• To prevent flare nut cracking and gas leaks, be sure to use
both a spanner and torque wrench together, as shown in the
drawing below, when connecting or disconnecting pipes to/
from the unit.
• Refer to the Table 3 for the dimensions of flare nut spaces.
• Refer to the Table 3 to determine the proper tightening torque.
Table 3
NOTE
• Apply ester oil or ether oil around the flare portions before
connecting.
• The flare nuts used must be those included with the main
body.
• Over-tightening may damage the flare and cause a refriger-
ant leakage.
Not recommendable but in case of emergency
You must use a torque wrench but if you are obliged to
install the unit without a torque wrench, you may
follow the installation method mentioned below.
After the work is finished, make sure to check that
there is no gas leak.
When you keep on tightening the flare nut with a spanner,
there is a point where the tightening torque
suddenly increases. From that position, further tighten the
flare nut the angle shown below:
Table 4
Pipe
size
Tightening torque
(ft.lbf)
Flare
dimensions
A (in.)
Flare shape (in.)
φ
1/4”
10.4 – 12.7
0.342-0.358
φ
3/8”
24.1 – 29.4
0.504-0.520
φ
1/2”
36.5 – 44.5
0.638-0.654
φ
5/8”
45.6 – 55.6
0.760-0.776
Pipe size
Further tightening
angle
Recommended arm length of
tool (in.)
φ
1/4”
60 to 90 degrees
Approx. 5 7/8
φ
3/8”
60 to 90 degrees
Approx. 7 7/8
φ
1/2”
30 to 60 degrees
Approx. 9 13/16
φ
5/8”
30 to 60 degrees
Approx. 11 13/16