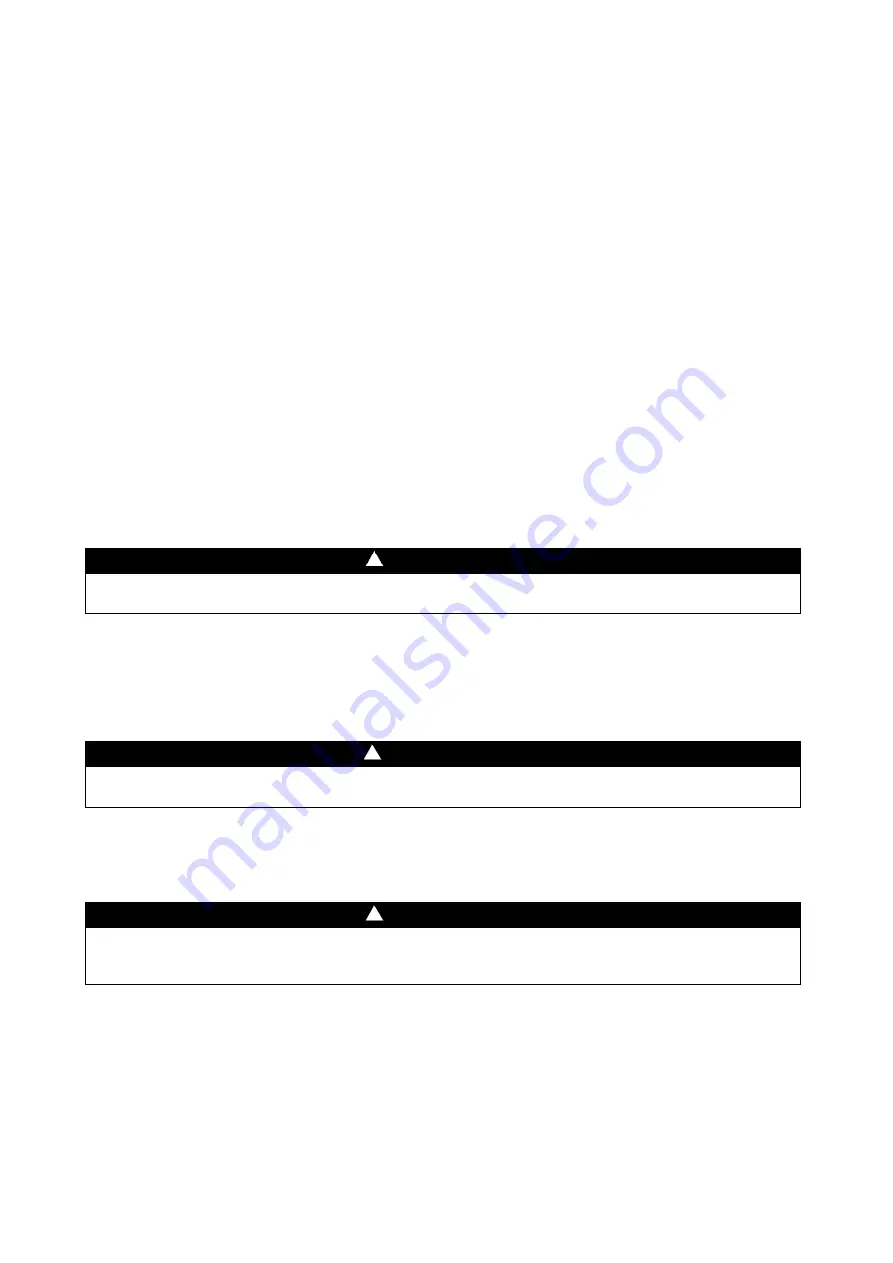
D-EIMWC00208-16EN - 35/48
1)
Monthly activities include alle the weekly ones
2)
The annual (or early season) activities include all weekly and monthly activities
3)
Machine operating values should be read on a daily basis thus keeping high observation standards
4)
Replace the oil filter when the pressure drop across it reaches 2.0 bar
5)
Check for any dissolved metals
6)
TAN (Total Acid Number) :
0.10 : No action
Between 0.10 and 0.19 : Replace antiacid filters and recheck after 1000
running hours. Continue to replace filters until the TAN is lower than 0.10.
0.19 : Change oil, replace oil filter and filter dryer. Verify at regular
intervals.
7)
Safety valves
Check that the lid and seal have not been tampered with.
Check that the discharge socket of the safety valves is not obstructed by any objects, rust or ice.
Check the manufacturing date shown on the safety valve. Replace the valve every 5 years a nd make sure it is
compliant with the current regulations in terms of the installation of the unit.
8)
Clean the pipes of the exchanger mechanically and chemically if the following occur: drop in the condenser
water capacity, drop in the differential temperature between inlet and outlet water, high temperature
condensation.
Replacement of filter dryer
It is strongly advised that the filter dryer cartridges be replaced in the event of a considerable pressure drop across the
filter or if bubbles are observed through the liquid sight glass while the subcooling value is within the accepted limits.
Replacement of the cartridges is advised when the pressure drop across the filter reaches 50 kPa with the compressor
under full load.
The cartridges must also be replaced when the humidity indicator in the liquid sight glass changes colour and shows
excessive humidity, or when the periodic oil test reveals the presence of acidity (TAN is too high).
Procedure to replace the filter dryer cartridge
ATTENTION
Ensure proper water flow through the evaporator during the entire servicing period. Interrupting the water flow during
this procedure would cause the evaporator to freeze, with consequent breakage of internal piping.
1.
Shut down the relevant compressor by turning the Q1 or Q2 switch to Off.
2.
Wait until the compressor has stopped and close the valve located on the liquid line.
3.
Once the compressor has stopped, place a label on the compressor startup switch, to prevent undesired
startups.
4.
Close the compressor suction valve (if any).
5.
Using a recovery unit, remove surplus refrigerant from the liquid filter until atmospheric pressure is reached.
The refrigerant must be stored in a suitable and clean container.
IMPORTANT
To protect the environment, do not release removed refrigerant into the atmosphere. Always use a recovery and
storage device.
6.
Balance internal pressure with external pressure by pressing the vacuum pump valve installed on the filter
cover.
7.
Remove the filter dryer cover.
8.
Remove the filter elements.
9.
Install the new filter elements in the filter.
ATTENTION
Do not start the machine before the cartridge has been correctly inserted in the filter dryer. The unit manufacturer will
accept no responsibility for any damage to persons or property caused during unit functioning if the filter dryer
cartridges have not been correctly inserted.
10.
Replace the cover gasket. Do not allow any mineral oil onto the filter gasket so as not to contaminate the
circuit. Use only compatible oil for this purpose (POE).
11.
Close the filter cover.
12.
Connect the vacuum pump to the filter and pull vacuum to 230 Pa.
13.
Close the vacuum pump valve.
14.
Recharge the filter with the refrigerant recovered during emptying.
15.
Open the liquid line valve.
16.
Open the suction valve (if any).
17.
Start the compressor by turning switch Q1 or Q2.
Содержание EWWD170~600G-SS
Страница 14: ...D EIMWC00208 16EN 14 48 Fig 7 Condenser Located above Chiller Unit Fig 8 Condenser Located below Chiller Unit...
Страница 21: ...D EIMWC00208 16EN 21 48 Fig 10 Refrigeration cycle EWWD G SS EWWD G XS 23 5 bar...
Страница 22: ...D EIMWC00208 16EN 22 48 Fig 11 Refrigeration cycle EWWD G SS EWWD G XS Partial Heat recovery 23 5 bar...
Страница 23: ...D EIMWC00208 16EN 23 48 Fig 12 Refrigeration cycle EWLD G SS OPTIONAL 23 5 bar...
Страница 45: ...D EIMWC00208 16EN 45 48...
Страница 46: ...D EIMWC00208 16EN 46 48...
Страница 47: ...D EIMWC00208 16EN 47 48...