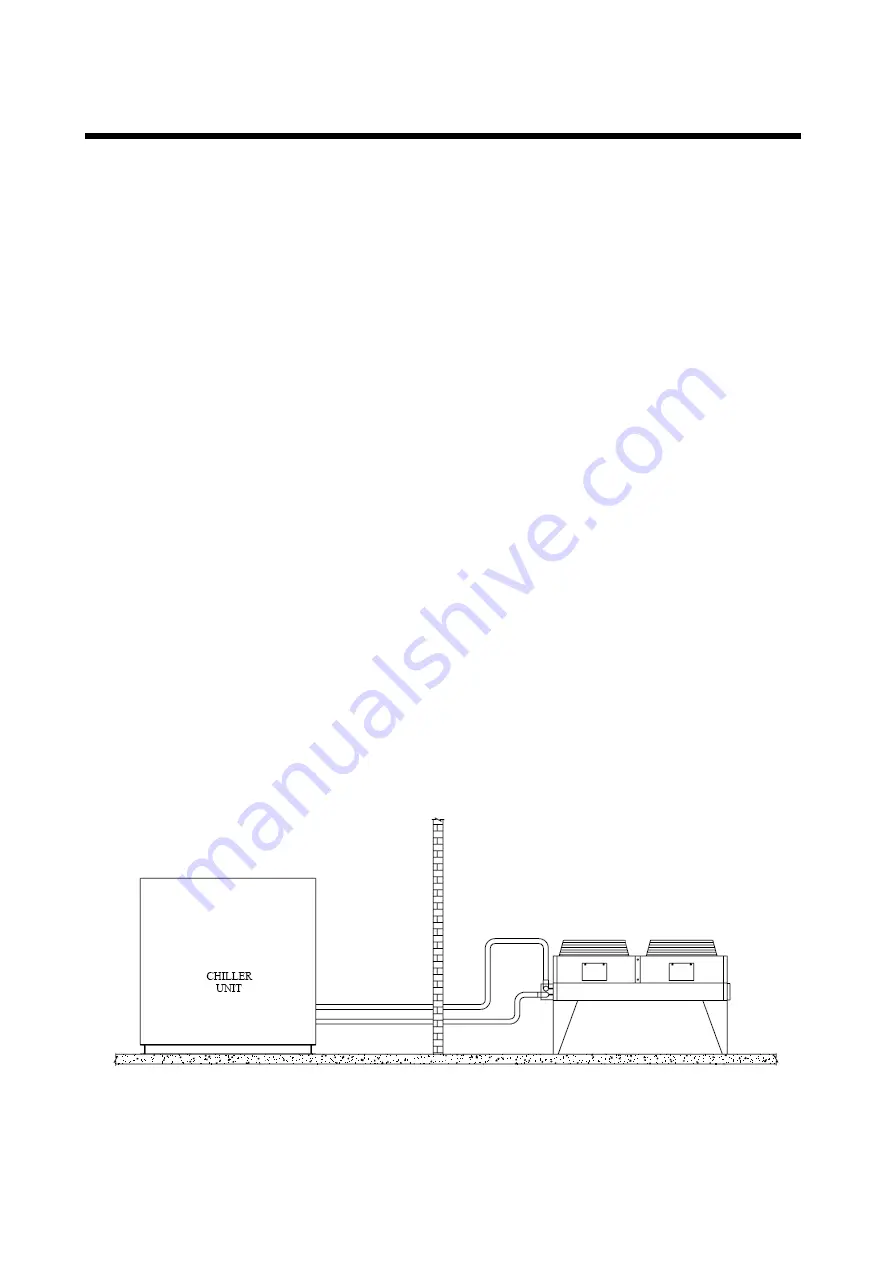
D-EIMWC00208-16EN - 13/48
Guidelines for remote condenser application
Design of remote condenser application, and, in particular, sizing of piping and piping path, is a responsibility of plant
designer. This paragraph is only focused to give suggestion to plant designer, this suggestions have to be weighted with
references to application peculiarities.
For remote condenser application, such as aircooled or evaporative condensers, the chillers are shipped with holding
Nitrogen
charge. It is important that the unit be kept tightly closed until the remote condenser is installed and piped to the
unit.
Chillers are supplied with filter drier, moisture indicator and expansion valve factory mounted as standard.
It is the contractor’s responsibility to install the interconnection piping, leak test it and the entire system, evacuate the
system and supply the refrigerant charge.
All piping must be conformed to the applicable local and state codes.
Use refrigerant grade copper tubing only and isolate the refrigeration lines from building structures to prevent transfer of
vibration.
It is important that the discharge lines be looped at the condenser and trapped at the compressor to prevent refrigerant
and oil from draining into the compressors; looping the discharge line also provide greater flexibility.
Do not use a saw to remove end caps. This might allow copper chips to contaminate the system. Use a tube cutter or
heat to remove caps. W hen sweating copper joints it is important to flow dry nitrogen through the system prior to
charging with refrigerant. This prevents scale formation and the possible formation of an explosive mixture of HFC134a
and air. This will also prevent the formation of toxic phosgene gas, which occurs when HFC134a is exposed to open
flame.
Soft solders are not to be used. For coppertocopper joints use a phoscopper solder with 6% to 8% silver content. A high
silver content brazing rod must be used for coppertobrass or coppertosteel joints. Only use oxyacetylene brazing.
After the equipment is correctly installed, leak tested and evacuated, it can be charged with R134a refrigerant and
started under the supervision of Daikin authorized technician.
Charge will be added until the liquid line sight glass is clear, with no bubbles flowing into the expansion valve. Total
refrigerant charge will depend on the used remote condenser and volume of refrigerant piping
Refrigerant piping design
The system can be configured in any of the main arrangements as shown in Figures 6, 7 and 8. The configuration and its
associated elevation, along with the total distance between the chiller and the aircooled cond enser are important factors
in determining the liquid line and discharge line sizes. This will also affect the field refrigerant charges. Consequently,
there are physical limits that must not be violated if the system is to operate as designed.
1.
The total distance between the chiller and the aircooled condenser should not exceed 60 equivalent meters
2.
Liquid line risers must not exceed 5 meters in height from the condenser liquid line connection.
3.
Discharge line risers cannot exceed an elevation difference greater than 30 actual meters.
Fig. 6 Condenser Located with No Elevation Difference
Содержание EWWD170~600G-SS
Страница 14: ...D EIMWC00208 16EN 14 48 Fig 7 Condenser Located above Chiller Unit Fig 8 Condenser Located below Chiller Unit...
Страница 21: ...D EIMWC00208 16EN 21 48 Fig 10 Refrigeration cycle EWWD G SS EWWD G XS 23 5 bar...
Страница 22: ...D EIMWC00208 16EN 22 48 Fig 11 Refrigeration cycle EWWD G SS EWWD G XS Partial Heat recovery 23 5 bar...
Страница 23: ...D EIMWC00208 16EN 23 48 Fig 12 Refrigeration cycle EWLD G SS OPTIONAL 23 5 bar...
Страница 45: ...D EIMWC00208 16EN 45 48...
Страница 46: ...D EIMWC00208 16EN 46 48...
Страница 47: ...D EIMWC00208 16EN 47 48...