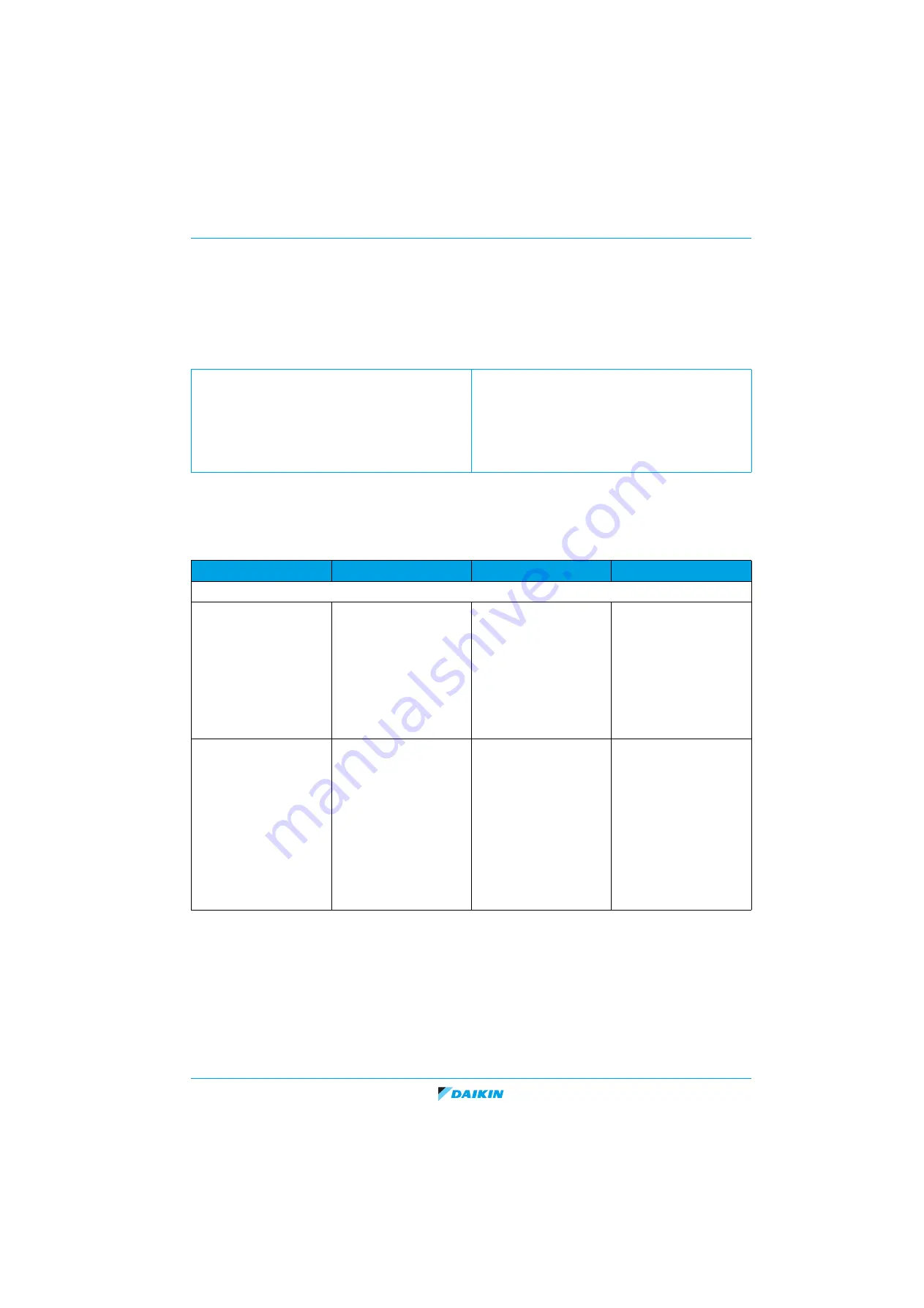
ESIE15-08B
|
Part 2. Troubleshooting
3. Symptom based troubleshooting
19/07/16
Page 49
Daikin Altherma Monobloc CA
3. Symptom based troubleshooting
By deeply analysing the system's components and logic, Daikin offers enhanced symptom based troubleshooting. To provide the
best troubleshooting efficiency, the related root cause categories for each symptom are ranked. The following ranking is used:
software control functions, end user related, parameter settings, installation related, component (mechanical or electrical) issues
and system design related. This ranking was obtained by a combination of checking speed and the probability of occurrence.
Overview of symptom based error situations:
3.1. Capacity shortage - General
Valid for both space heating and domestic hot water capacity shortage.
Capacity shortage - General ...........................................................49
Capacity shortage - Space heating .................................................51
Capacity shortage - Domestic hot water operation .........................53
The system does not start/operate .................................................54
Inaccurate temperature control (for both domestic hot water and
space heating operation) ................................................................55
Water leakage or water release via the water pressure relieve valve
........................................................................................................56
Power consumption too high ..........................................................57
Increased sound level - water pump .............................................. 58
Increased sound level - compressor .............................................. 58
Tapping water related..................................................................... 59
Compressor related ....................................................................... 60
Pump related.................................................................................. 62
User interface (no or strange display) ............................................ 62
Outdoor unit is iced up (defrost problem)....................................... 63
Energy metering is 'wrong' ............................................................. 63
Water volume/flow related.............................................................. 64
Possible failures
Root cause
Check
Corrective action
Root cause category: software control
Compressor (M1C) frequency
limited - high discharge tem-
perature protection function
active.
In case the discharge temper-
ature is higher than 105°C the
compressor frequency will be
reduced. When the discharge
temperature is lower than
105°C the frequency can
increase again.
Activation of the protection
function can be caused by var-
ious reasons, therefore we
recommend to check the fol-
lowing:
•
Check refrigerant charge
•
Check expansion valve for
correct operation (see
page 97).
• Check
discharge
thermistor (see page 88).
Based on the diagnosis exe-
cute one of the following
actions:
• Correct
the
refrigerant
charge.
•
Replace expansion valve
(see page 131).
• Replace
discharge
thermistor (see page 124).
Compressor (M1C) frequency
limited - high pressure protec-
tion function active.
In case high pressure is higher
than 38 barg the compressor
frequency will be reduced.
When the pressure drops
below 36 barg the compressor
frequency can increase again.
Activation of the protection
function can be caused by var-
ious reasons, therefore we
recommend to check the fol-
lowing:
• Check
pressure
sensor
(see page 94).
•
Check high pressure side
plate type heat exchanger
(see page 77) for good
water flow and heat
exchange.
• Check
the
refrigerant
charge.
Based on the diagnosis exe-
cute one of the following
actions:
• Replace
pressure
sensor
(see page 130).
•
Optimize the water flow
through the high pressure
side plate type heat
exchanger.
• Correct
the
refrigerant
charge.