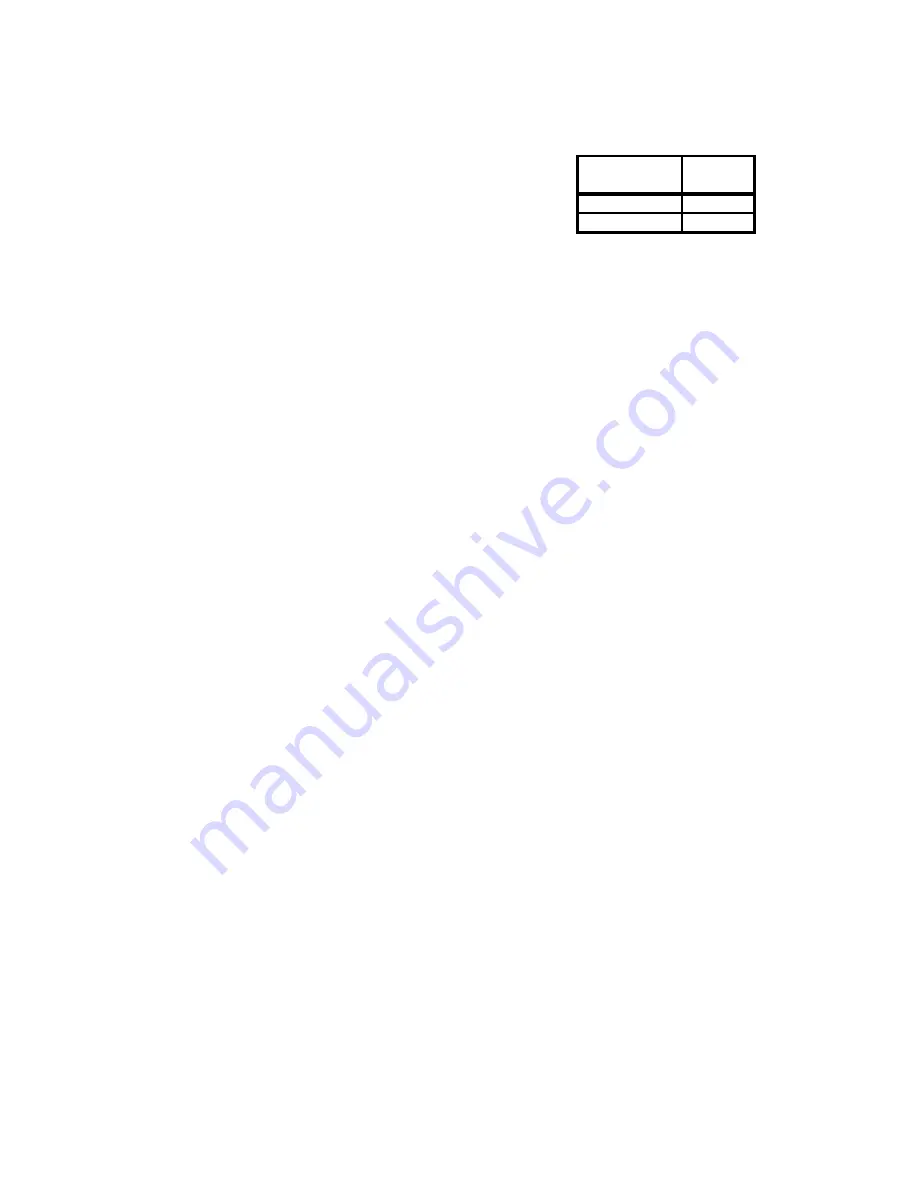
7
FINAL CHARGE ADJUSTMENT
The outdoor temperature must be 60°F or higher. Set the room
thermostat to COOL, fan switch to AUTO, and set the tempera-
ture control well below room temperature.
After system has stabilized per startup instructions, check sub-
cooling and superheat as detailed in the following section.
EXPANSION VALVE SYSTEM
NOTE:
The expansion valve bulb must be in place on the suction
line and insulated.
Expansion Valve Indoor Coils:
Outdoor Temperature Over 60ºF.
When the outdoor tempera-
ture is above 60ºF, charge the system with the room thermostat
set in the “Cooling” mode and the fan operating in the “Auto”
position.
Outdoor Temperature Below 60ºF.
When the outdoor tempera-
ture is below 60ºF, charge the system with the room thermostat
set in the “Heat” mode and the fan operating in the “Auto” posi-
tion.
System Charging Cooling Mode.
At stabilized cooling conditions
and with an outdoor temperature of 60°F or higher, the system
should have from 9°F to 13°F subcooling. For a proper subcooling
reading, measure the refrigerant pressure and temperature at the
outdoor unit’s liquid line service valve. If you have less than 9°F
subcooling, add charge. If you have more than 13°F subcooling,
remove charge.
While reaching the proper subcooling level it is important to know
the discharge line temperature. This temperature should be at
least 80ºF over ambient or unit is flooding back to compressor.
System Charging Heating Mode.
Measure the hot gas discharge
at the compressor to check the system charge in heat mode.
1. Allow the system to operate for at least 20 minutes.
2. Attach and insulate an electronic thermometer to the hot
gas discharge line mid way between the compressor and the
reversing valve.
Note:
The thermometer is to be well insu-
lated to prevent ambient influences.
3. Adjust the charge to maintain a clear sight glass.
4. Allow the compressor to operate for about 10 additional min-
utes and measure the hot gas discharge temperature.
5. Using an additional electronic thermometer, measure the
ambient.
6. Adjust the charge until the hot gas temperature equals 105
º
F
+ ambient (+ or – 5
º
F). Remove charge to increase the tem-
perature.
NOTE:
When adjusting the charge, allow the compressor to
operate for about 10 minutes before taking readings.
NOTE:
Subsequent opening and replace of the cap will require
only 1/2 to 1 hex flat. See the table below for the torque required
for an effective seal on the valve bonnet (1/6 turn past finger tight.
TUBING SIZE
TORQUE
(ft-lbs)
5/8
14
1 3/8
16
After closing the valve bonnet, perform a final refrigerant leak test
on the valves and sweat connections. Return the room thermo-
stat to the desired settings.
DEFROST CONTROL ADJUSTMENTS
This heat pump uses a Time/Temperature method for defrost. A
thermal sensor electrically set to “Normally Open” is wired to the
electronic defrost control located in the control box. The thermal
sensor attached to the condenser coil determines the outdoor coil
temperature.
Both coil temperature and compressor “run time” determine de-
frosting of the outdoor coil. Adjustments to the defrost timing se-
lection can be changed from the 60 minute factory setting to ei-
ther 30 or 90 minutes by moving the jumper on the defrost con-
trol. For the system to initiate a defrost, the following statements
must be true:
•
The Defrost Sensor is closed, and
•
The compressor “run time” is equal to the timing selection
on the defrost board.
During defrost the following actions occur:
1. The reversing valve is energized and the heat pump oper-
ates in the cooling mode.
2. The airhandler auxiliary heat (if equipped) is activated.
3. The condenser fan motor is shut-off.
If the defrost cycle has not terminated after ten (10) minutes the
control will override the defrost sensor and revert to a heating
mode.
The defrost control has test pins which can be useful when trouble-
shooting in the heating mode. These test pins accelerate the com-
pressor run time counter. The suggested method for accessing
this feature is:
1. Run unit in heat mode.
2. Check unit for proper charge.
NOTE:
Bands of frost indicate low refrigerant charge.
3. Shut off power to unit.
Содержание DZ11TA Series
Страница 10: ...10 THIS PAGE LEFT INTENTIONALLY BLANK ...