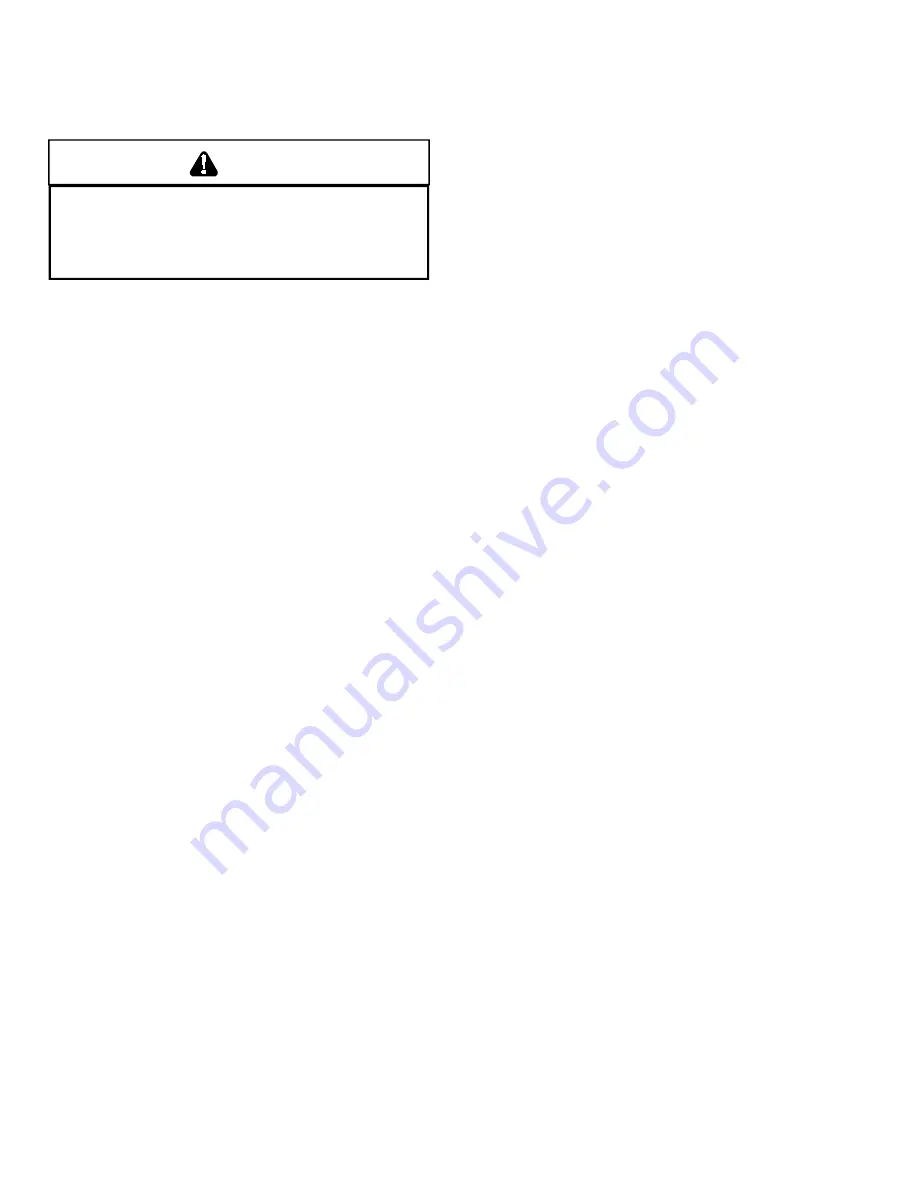
MAINTENANCE
56
Should the figure you calculated not fall within five (5) percent
of the nameplate rating of the unit, adjust the gas valve
pressure regulator or resize orifices.
A
LWAYS CONNECT A MONOMETER TO THE OUTLET TAP AT THE GAS
VALVE BEFORE ADJUSTING THE PRESSURE REGULATOR.
I
N NO CASE
SHOULD THE FINAL MANIFOLD PRESSURE VARY MORE THAN PLUS OR
MINUS .3 INCHES WATER COLUMN FROM 3.5 INCHES WATER COLUMN
FOR NATURAL GAS OR 10 INCHES WATER COLUMN FOR PROPANE GAS.
CAUTION
To adjust the pressure regulator on the gas valve, turn
down (clockwise) to increase pressure and input, and out
(counterclockwise) to decrease pressure and input.
Since normally propane gas is not installed with a gas meter,
clocking will be virtually impossible. The gas orifices used
with propane are calculated for 2500 BTU per cubic foot gas
and with proper inlet pressures and correct piping size, full
capacity will be obtained.
With propane gas, no unit gas valve regulator is used;
however, the second stage supply line pressure regulator
should be adjusted to give 10" water column with all other
gas consuming appliances running.
The dissipation of the heat transferred to the heat exchanger
is now controlled by the amount of air circulated over its
surface.
The amount (CFM) of air circulated is governed by the
external static pressure in inches of water column of duct
work, cooling coil, registers, etc., applied externally to the
unit versus the motor speed tap (direct drive) or pulley
adjustments of the motor and blower (belt drive).
A properly operating unit must have the BTU per hour input
and CFM of air, within the limits shown to prevent short cycling
of the equipment. As the external static pressure goes up,
the temperature rise will also increase. Consult the proper
tables for temperature rise limitation.