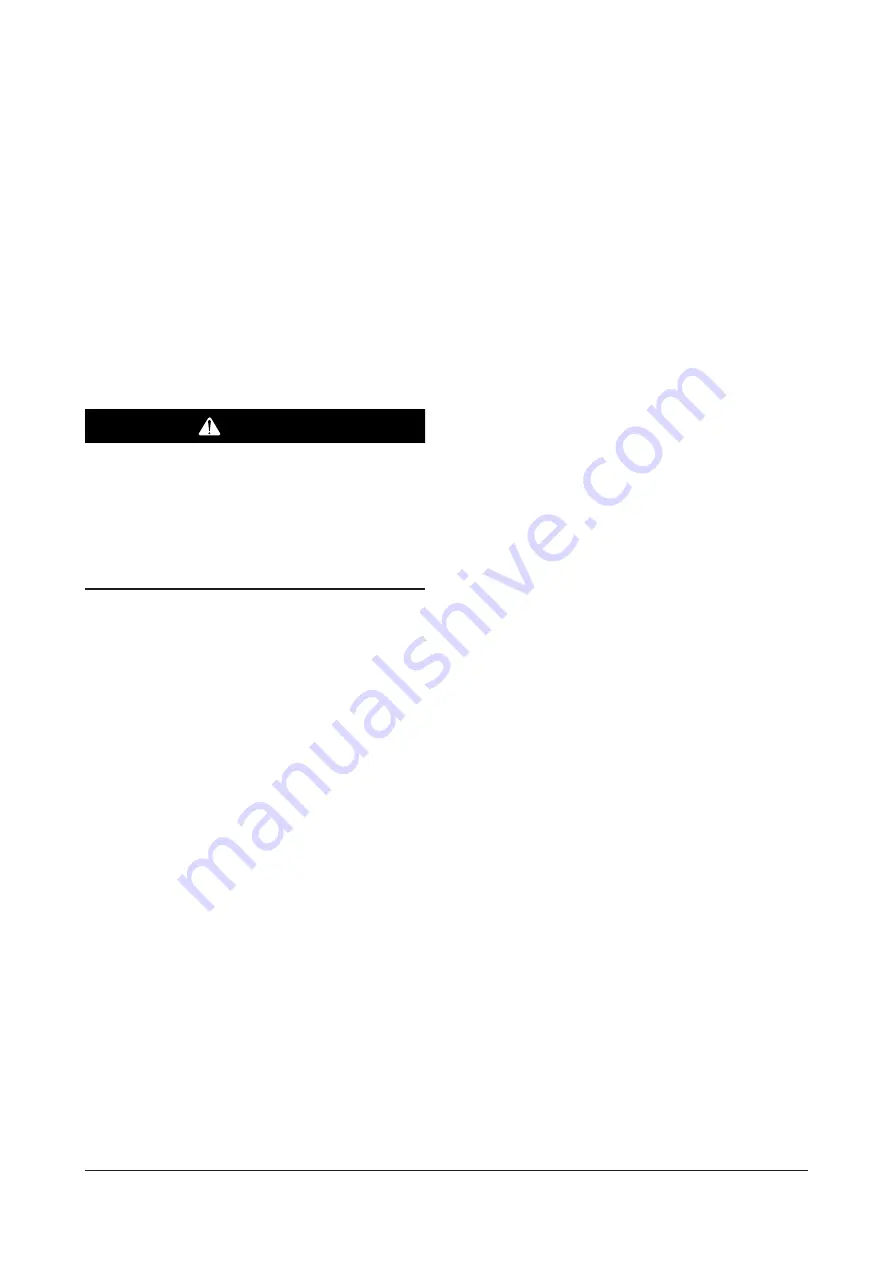
Disassembly And Assembly
General
During disassembly, particular attention should be given
to identification of parts for reassembly. Spools are
selectively fitted to valve bodies and must be returned to
the same bodies from which they were removed,
Valve sections must be reassembled in the same
order. Figure IDCS015B is an exploded view showing
the proper relationship for reassembly. Reference is
made to these figures in the procedures which follow.
Unit Removal
1. Thoroughly clean the exterior of the valve and the
area around the valve to prevent contamination of
the system during removal.
2. Loosen mounting bolts that hold valve to mounting
surface. Be ready to catch fluid retained inside
lines and valve.
3. Remove valve from mounting surface and set it on
a clean work bench.
Unit Disassembly
NOTE : All parts within the unit must be kept clean
during the overhaul process. Handle each part with
great care. The close tolerance of the parts makes
this requirement very important. Clean all parts that
are removed from the unit with a commercial cleaning
solvent that is compatible with the system fluid.
Compressd air may be used in the cleaning process,
however, it must be filtered to remove water and
other contamination. Be sure the unit is not subjected
to pressure. Disconnect and cap all lines and
disconnect linkage to the spool.
Attaching Parts
1. Remove the four nuts (1) and four tie studs (2).
2. Separate the valve sections, being careful not to
destroy or lose spacers.
3. Remove retainer (3), seals (4) and O-rings(5).
Flow Control Checks
1. Remove flow control check springs (6) and ball(s)
(7).
End Caps
1. Unscrew two screws (8) holding dust cover (9),
retainer (10) and sleeve (11).
2. Remove the O-ring (12) from the sleeve.
Operating Spool
1. Slide the spool (13) out of its bore.
2. Remove the quad seals (14) from the valve body
around the spool bore.
3. Remove the wiper seal (15).
NOTE : Do not remove the centering spring (16) or
the retainers (17) unless it is necessary to replace
them.
Check Valve
1. Remove the retainer ring (18) and screw out plug
stop adjuster (19) from the valve body.
2. Remove the back-up ring (20) and O-ring (21).
3. Remove the spring (22) and ball (23) from the
valve body.
25 of 29
New Hydraulic Systems
Disassembly and Assembly
Before breaking a circuit connection, make certain
that power is off and system pressure has been
released. Lower all vertical cylinders, discharge
accumulators, and block any load whose
movement could generate pressure. Plug all
removed units and cap all lines to prevent the entry
of dirt into the system
WARNING
Содержание D20S-2
Страница 8: ......
Страница 13: ......
Страница 24: ...27 of 29 New Hydraulic Systems Disassembly and Assembly IDCS015B...