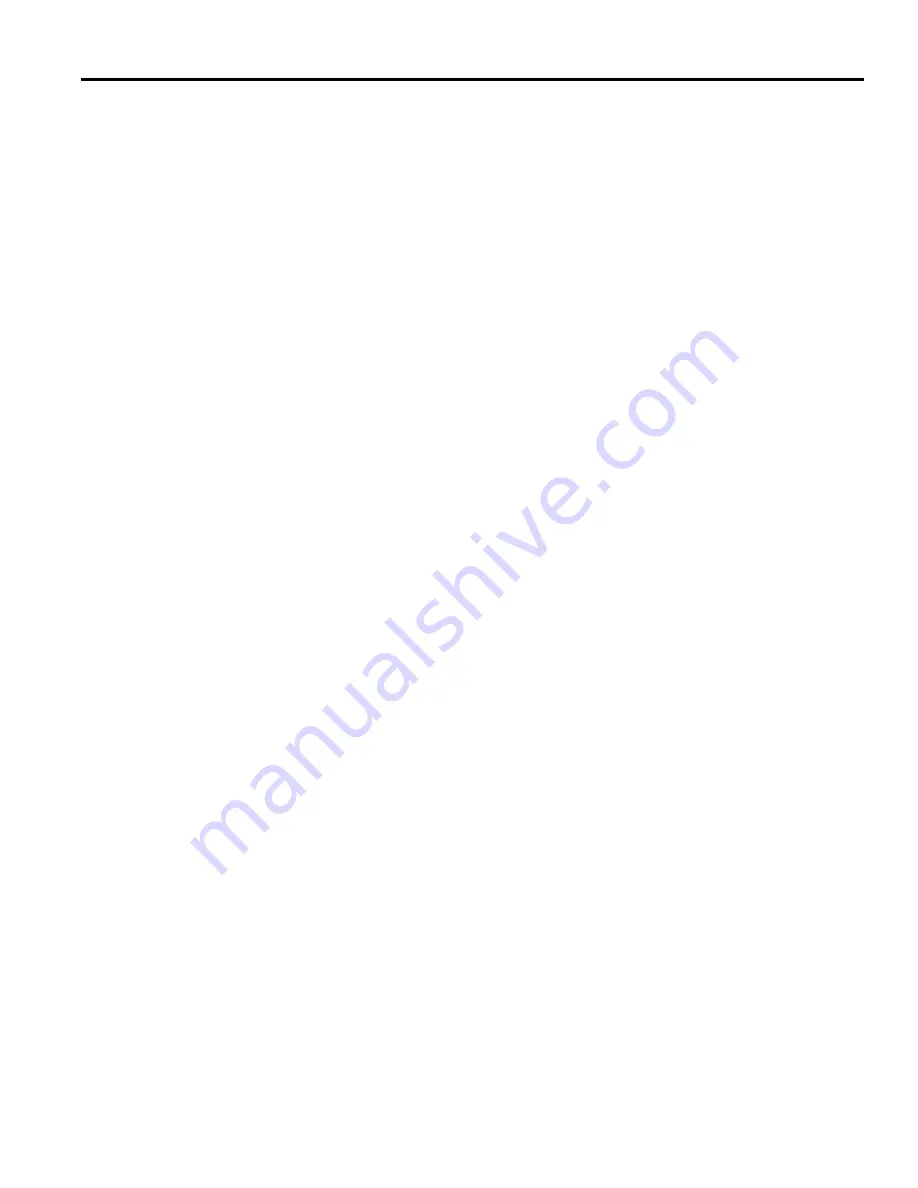
SPRAYER OPERATION 6
27
Electric Boom Lift.
• Check both actuator mounting bolts for tightness
and for wing down position parallel to ground
position, adjust according to set-up instructions.
• Check control harness fuse (30 amp rating).
• Check control console toggle switch for play and
proper operation.
• Check harness connectors at control box and at
each actuator.
Hose Reel.
• Check supply hose, from pressure side of pump to
the swivel inlet on reel drum, for cracks, kinks, or
leaks.
• Lubricate the reel swivel at the grease zerk (if
equipped).
• Check reel to tank hardware for tightness and
evidence of leaks. Gasket sealer and fender
washers should be used if not present (refer to the
mounting instructions that come with the
accessory).
• If electric rewind option is used, check battery and
harness connections (40 amp circuit breaker
should also be installed).
Foam Marker.
• Inspect solution tank for leaks and cracks.
• Check cap assembly for cracks and leaks.
• Check fuse in control harness (10 amp rating).
• Be sure to use only SDI Foam Concentrate with
the foam marker accessory. Use of other brands
will cause adverse performance.
• Activate power switch to the left then to the right
positions and verify corresponding solenoid
operation (you will hear a click) the compressor will
start and if there is fluid in the container, liquid
should flow to the feed tube on corresponding
solenoid and foam generator cone junction tube.
• If solenoid clicks but foam liquid doesn't move
through foam generator cone feed tubes, check
each feed line check valve located just before each
solenoid inlet. Clean as needed.
• Check supply fasteners on boom tubes for proper
tightness and position. They should be positioned
so they do not interfere with the tips or nozzle
check valves. The loom (black ribbed cover) should
run along the top of the boom tube and fastened
with nylon cable ties.
• Check foam generator cone position. It should be
at the end of the boom wing and clear the spray
pattern distribution area. Keep cones out of spray
by tilting up (required for rainbow style tips).
6.5
SPRAYER TANK ADDITIVES _________________________________________________
Dye Markers - Avoid heavy, thick dye markers and only
add dyes into a full mixing tank, Do not add to an empty
tank.
Due to pigment granules and/or by-products, the use of
dyes can lead to mechanical seal problems. Because of
the high speed of the impeller seal and the heat that is
generated, the pigments can scale up the ceramic seal
surface. This will cause the seals to leak (pump appears
broken). Frequent rinsing between smaller tank loads
(batches) can reduce the leakage at the seals. Also,
using less dye than recommended, but enough to still
see a color (marker) change, can result in better
performance.
Spray Liquid Viscosity - the addition of certain WP
(Wettable Powders), WDG (Water Dispersers Granular)
or EC (Emulsified Concentrate) chemicals, etc. may
cause the viscosity (thickness) of the water to increase.
This can sometimes affect the calibration of the spray
nozzle out-put at pre-calibration water numbers. Consult
Chemical Supplier for recommended modifications to
your system.
Содержание Spraytek DS175
Страница 35: ...NOTES 7 35 7 NOTES...