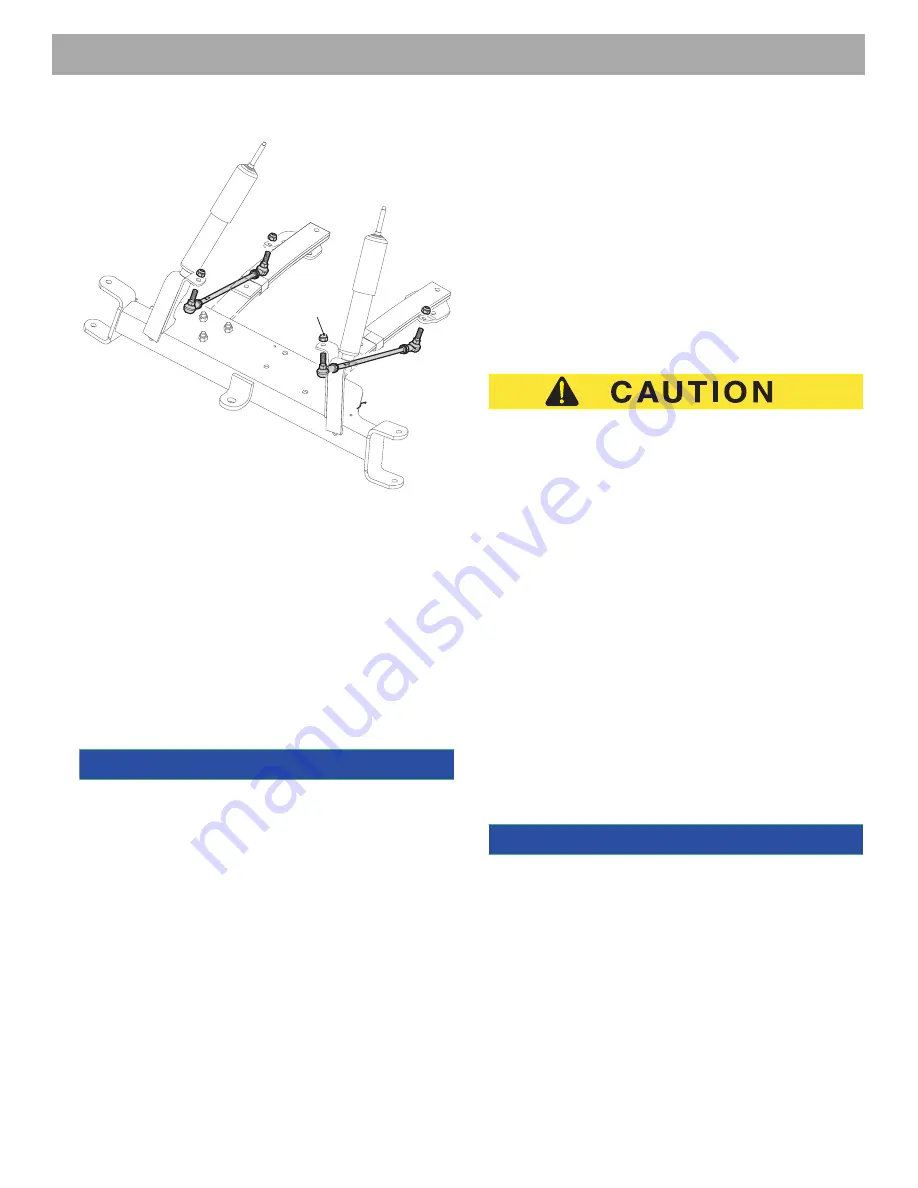
Page H-7
Repair and Service Manual
B
B
FRONT SUSPENSION AND STEERING
Read all of Section B and this section before attempting any procedure. Pay particular attention to Notices, Cautions, Warnings and Dangers.
Fig. 7 Axle Linkage Rod Replacement
Front Spring Replacement
Tool List
Qty.
Jack Stands ................................................................. 4
Ratchet ........................................................................ 1
Socket, 3/4" ................................................................. 1
Socket, 5/8" ................................................................. 1
Wrench, 5/8"................................................................ 1
Torque Wrench ft. lbs................................................... 1
Tape Measure.............................................................. 1
Failure of a single spring will result in overstressing the other
spring; therefore, replace front springs as a set.
The following procedure will replace one spring at a
time.
Loosen front wheels. Lift and support front of vehicle
per SAFETY section. In addition, support front axle with
jack stands. Remove front wheels.
To detach driver side spring:
Fully loosen the two rack and pinion unit lock nuts (15),
one near the bellows and one on the rear side of the
rack and pinion unit, until only one thread is engaged
(Ref. Fig. 6). Remove the lock nut (15) and washer (14)
from the long bolt (20) and discard lock nut. The rack
and pinion unit is now loose.
Remove the two 1 3/4" long bolts (18) and lock nuts
(19) securing driver side spring to axle and discard lock
nuts (19).
Hold nut (21) with wrench and loosen long bolt (20).
Note location of washer (22) and thread long bolt out as
far as possible to remove the washer, nut and spacer
(23). Then pull long bolt and spring plate (24) from axle
and spring. Retain above items (20 - 24) for assembly
at their original locations.
Pull upper driver side of floor mat out of plastic trim
retainer and away from floor. Locate and remove hard-
ware (25 - 27) securing rear of spring (17) to vehicle
frame and discard lock nuts (27).
To prevent stress and possible damage to the rack and
pinion unit, the driver side spring must be mounted to
the axle with the hardware (20 - 23) installed in its orig-
inal location (Ref. Fig. 6).
Driver side spring installation is the reverse order of
disassembly making sure to install the long bolt (20),
spring plate (24), spacer (23), nut (21) and washer (22)
in their original locations. Use new lock nuts (15, 19,
27) to secure the rack and pinion unit (16), two short
bolts (18) and rear bolts (25).
To detach passenger side spring:
Remove the hardware (18, 19, 24, 28) securing the
front of the passenger side leaf spring (17) to the axle
(3) and discard lock nuts (19) (Ref. Fig. 6).
Pull upper passenger side of floor mat out of plastic trim
retainer and away from floor. Locate and remove hard-
ware (25 - 27) securing rear of spring (17) to vehicle
frame and discard lock nuts (27).
Using new lock nuts (19, 27), install passenger side
spring in the reverse order of disassembly.
After the springs are replaced, the axle will need to be aligned
to the frame. Unless the axle has been replaced, wheel align-
ment will not be affected; however, it is always good practice
to check wheel alignment any time the front-end components
are replaced or adjusted.
When front springs are replaced, the front axle must be
aligned to the frame. The distance from the center bolt
at rear of left spring to the center bolt at front of right
spring must be the same as the distance from the cen-
ter bolt at rear of right spring to the center bolt at front
of left spring (Ref. Fig. 8). Tighten the spring hardware
(21, 19, 27) first and rack and pinion unit hardware (15)
next to 35 - 50 ft. lbs. (50 - 70 Nm) torque.
Ball Joint Nut
NOTICE
NOTICE