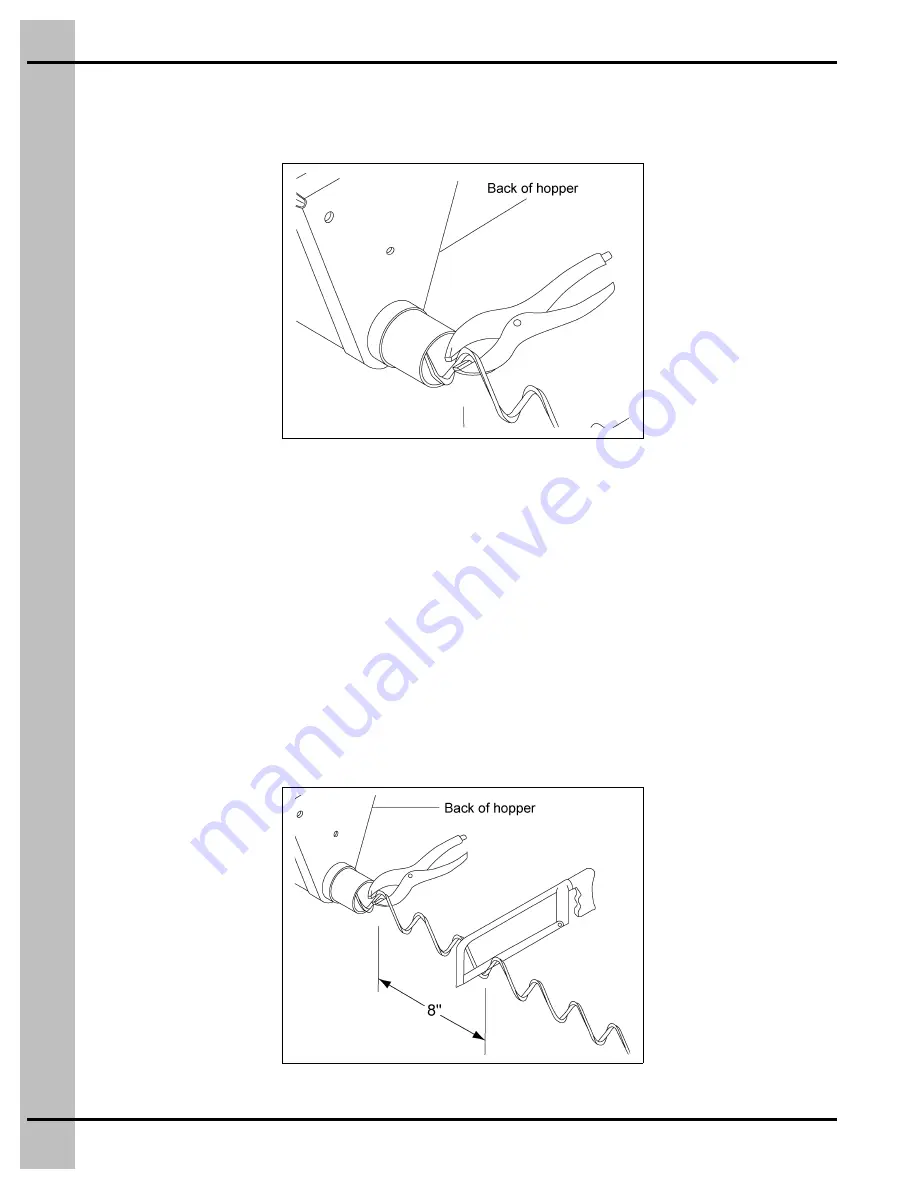
7. Installation
56
PNEG-250
Pan Feeders
13. Pull the auger out from the back of the hopper an additional 8" (20.3 cm), and clamp at that point
with a pair of locking pliers.
14. Allow the pliers to rest against the boot to hold the auger in place.
Figure 7CK
If the auger is allowed to spring back, the bearing race may crack. The auger will pull itself and the
bearing plate assembly into the correct position. Do not overtighten the U-clamp, or distortion of the
auger tube may result. Rapid cooling will cause hardening and embrittlement. The auger must be
smooth to prevent feed buildup and premature tube wear.
15. Cut the auger at the mark which allowed proper stretch.
16. Leave the pliers in place against the boot.
17. Insert the idler shaft assembly into the auger and thread the auger through the U-bolt up to
1/2" (1.27 cm) from the bearing.
18. Tighten the U-bolt securely.
19. Slowly release tension on the auger.
20. Reattach the bearing cap and the U-clamp, and tighten them securely.
Figure 7CL
Содержание Hi-Lo
Страница 1: ...PNEG 250 Hi Lo and PRO 1 Pan Feeder Installation and Operation Manual PNEG 250 Date 12 02 09 ...
Страница 2: ...2 PNEG 250 Pan Feeders ...
Страница 36: ...7 Installation 36 PNEG 250 Pan Feeders Program Chart Figure 7AZ ...
Страница 37: ...7 Installation PNEG 250 Pan Feeders 37 Figure 7BA ...
Страница 38: ...7 Installation 38 PNEG 250 Pan Feeders Figure 7BB ...
Страница 39: ...7 Installation PNEG 250 Pan Feeders 39 Figure 7BC ...
Страница 40: ...7 Installation 40 PNEG 250 Pan Feeders Figure 7BD ...
Страница 41: ...7 Installation PNEG 250 Pan Feeders 41 Figure 7BE ...
Страница 60: ...7 Installation 60 PNEG 250 Pan Feeders Figure 7CQ ...
Страница 80: ...9 Parts List 80 PNEG 250 Pan Feeders Hi Lo End Control and Drive Mount 7100113 ...
Страница 82: ...9 Parts List 82 PNEG 250 Pan Feeders Micro Switch Center House Control Pan 7101534 ...
Страница 84: ...9 Parts List 84 PNEG 250 Pan Feeders Micro Switch End Control Pan 7101482 ...
Страница 90: ...9 Parts List 90 PNEG 250 Pan Feeders Feed Level Control Switch 7051400 ...
Страница 92: ...9 Parts List 92 PNEG 250 Pan Feeders Flex Flo Hopper Level Control Assembly ...
Страница 94: ...9 Parts List 94 PNEG 250 Pan Feeders Flex Flo Level Control Switch FLX 3802 ...
Страница 96: ...9 Parts List 96 PNEG 250 Pan Feeders Winching and Miscellaneous Accessories ...
Страница 98: ...9 Parts List 98 PNEG 250 Pan Feeders Winching and Miscellaneous Accessories Continued ...
Страница 102: ...9 Parts List 102 PNEG 250 Pan Feeders Winch Assembly Parts ...
Страница 106: ...9 Parts List 106 PNEG 250 Pan Feeders Switch Box E170 A1007 ...
Страница 108: ...108 PNEG 250 Pan Feeders 10 Wiring Diagram Rooster Power Winch Wiring Diagram ...