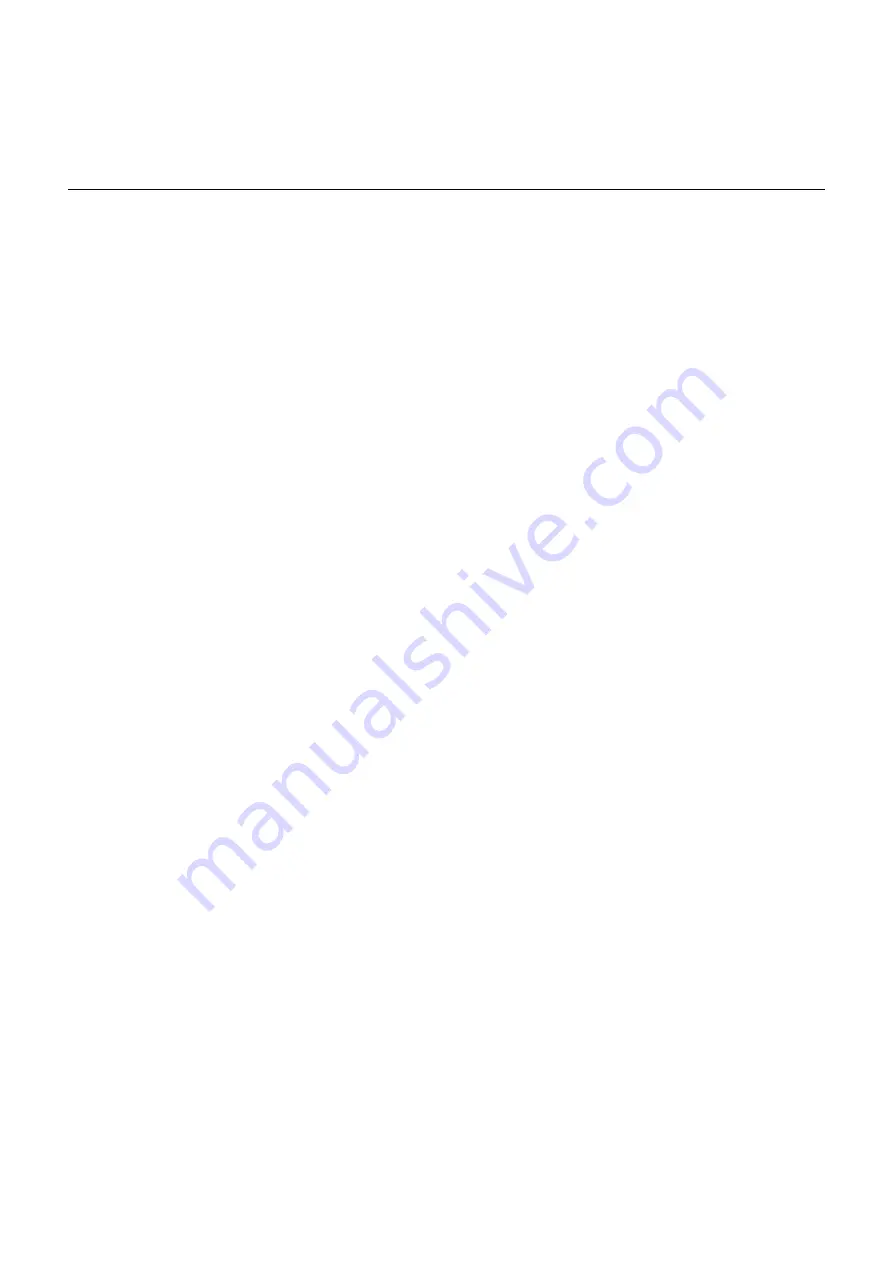
04/2008 - Art. Nr. 13 021 970A
12
Start up
Unit control
Firing
Setting and checking of safety devices
Checking the operating sequence
• Open the fuel hand-operated 1/4 turn
valve and close it again immediately.
• Switch the burner on.
• Select the ON position on the control
panel.
• Close the thermostatic circuit.
• Unlock the control and safety unit and
check to see that it functions properly.
The programme must proceed as
follows:
- preventilation: 20s,
- electrode firing: 3s,
- opening of the valves,
- closing of the valves,
within no more than 3s after their
opening,
- Burner shutdown due to a lack of gas
pressure or locking of the control and
safety unit due to flame extinguishing.
If a doubt arises, repeat the above
test.
The firing can take place only after the
operating sequence has been checked
(this operation is of prime importance).
Warning:
The firing can take place when all the
conditions listed above are fulfilled,
especially the field pre-setting of the
fuel valve.
• Connect a microammeter (scale 0 to
500µA DC) in place of the ionisation
bridge
• Disconnect the 4-pole plug (stage two
regulating thermostat).
• Open the fuel valves.
• Close the thermostatic circuit.
• Unlock the control and safety unit.
The burner will ignite in stage one.
Assess the ignition quality.
• Wait 8 seconds and then reconnect
the 4-pole plug.
The burner will operate in stage two.
• Check the combustion (CO and CO
2
index) as soon as the flame is
apparent.
• Read the ionisation current value
(ranging from 15 to 25µA).
• Measure the gas flow stage on the
meter.
• Adjust the gas flow stage by acting
upon the pressure controller.
• Adjust the air flow rate by actuating
servomotor cam
I
.
- Increase the stage two air flow rate by
increasing the value read on the
graduated cylinder for cam
I
.
The effect is direct.
- Reduce the stage two air flow rate by
decreasing the value read on the
graduated cylinder for cam
I
.
Disconnect the 4-pole plug for a
moment and then reconnect it. Cam
I
will take up its new position.
• Optimize the firing quality and the
combustion results by acting upon
- The setting of valve MB ZRDLE
instant flow stage.
• Make plug key
B
rotate in a cw
direction toward
arrow -:
the flow stage decreases and vice
versa and the firing is more flexible.
- The setting of secondary air at
dimension
Y
.
• Make plug
A
rotate in a cw direction
toward
arrow -:
the CO
2
index decreases and vice
versa. Modifying dimension Y may
involve the adjustment of the air flow
stage.
• Check the combustion.
Comply with the smoke temperature
value recommended by the boiler
manufacturer to obtain the required
effective output.
• Shut down the burner.
• Disconnect the 4-pole plug.
• Place stage one back in operation.
• Check the combustion: CO and CO
2
indices.
Do not do anything else to the settings
for reading
Y
and the instantaneous flow
rate.
• Read the ionisation current.
• Measure the gas flow rate at the
meter.
• Adjust the gas flow rate by actuating
crown
D
.
• Adjust the air flow rate by actuating
servomotor cam
IV
.
- Increase the stage one air flow rate by
increasing the value read on the
graduated cylinder for cam
IV
.
Connect the 4-pole plug for a moment
and then disconnect it. Cam
IV
will
take up its new position.
- Reduce the air flow rate by decreasing
the value read on the graduated
cylinder for cam
IV
. The effect is
direct.
• Retighten the valve’s locking screw.
• Shut down the burner.
• Connect the 4-pole plug.
• Restart the burner.
Assess its operation :
upon ignition, when changing from one
stage to another, and when either
increasing or decreasing the power.
• Check the tightness of the gas
manifold connections with the burner
in service by using a suitable foaming
agent. No leakage must be detected.
• Check the safety devices.
Setting and checking of safety
devices
Gas pressure switch
• Set it to the minimum distribution
pressure.
The burner is in service.
• Slowly close the fuel hand-operated
1/4 turn valve.
The burner must cease to function due
to a lack of gas pressure.
• Open the hand-operated 1/4 turn valve
again.
The burner restarts automatically.
The pressure switch is set.
Air pressure switch
The burner is in service at firing flow
stage.
• Detect the air pressure switch
switching off point (locking).
• Multiply the value read by 0.9 to obtain
the setting point.
• Restart the burner.
• Gradually plug the burner air inlet.
• Check to see that the CO index
remains below 10,000ppm before
locking the unit.
Otherwise, increase the setting value of
the air pressure switch and repeat the
test.
• Disconnect the gas measuring
instruments.
• Close the pressure taps.
• Unlock the unit.
The burner is in service.
• Check the tightness.
• Disconnect the two wires on the
microammeter simultaneously.
The unit must be locked immediately.
• Replace the ionisation bridge.
• Replace the covers.
• Unlock the unit.
The burner is in service.
• Check the tightness between the
flange and the boiler front wall.
• Check the combustion under
operating conditions (doors closed,
etc.) and the circuit tightness.
• Record the results on the relevant
documents and give them to the
agent.
• Switch the burner to AUTO.
• Provide all the data required for proper
operation.
• Affix the boiler house plate so that it be
apparent.
Содержание C43 GX207/8
Страница 2: ...04 2008 Art Nr 13 021 970A 2 ...
Страница 39: ...04 2008 Art Nr 13 021 970A 39 ...