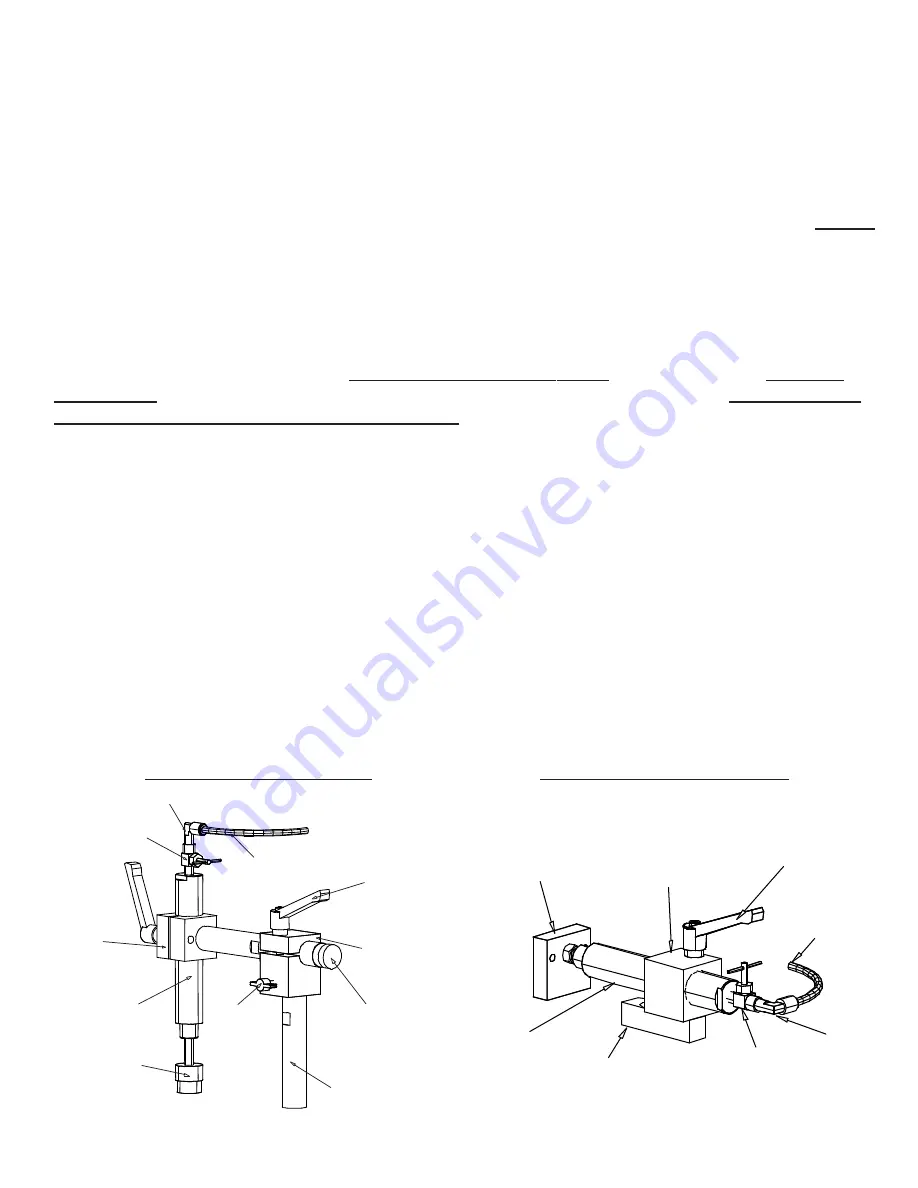
Hand Operated Machines and Cutting Speed:
The blade is rotating at approximately 3700 RPM. When moving the blade through the material, the blade must
NEVER
be allowed to
dwell in the work. If fine finishes are required:
1. Use a sharp blade.
Do Not Force the Cutting Action,
causing the motor to stall.
2. Use a
constant, even pressure
when cutting through material.
Spring Return:
Each sawhead is equipped with a drawbar return spring. The function of the spring is to return the sawhead to the
rest position upon release of the handle.
Do not adjust the spring pressure.
If the spring breaks,
Replace It
Immediately!
Make sure spring is attached properly (see Diagram “D” on Page No. 8) and
Never use a hand
operated machine without the return spring in place.
Clamping and Work Slippage:
The work must never be allowed to move or vibrate as it is being cut. When the work is positioned against a stop,
it
must be clamped
either by hand holding or by pneumatic air clamps.
Never allow unclamped work between
the blade and the stop, as the blade can grab the material and throw it, thereby causing damage to the
blade, the machine, and possibly harming the operator.
CTD offers both Horizontal and Vertical Clamps. The Horizontal Clamp pushes the material backwards against the
rear fence and is mounted in the keyways of the base. A Vertical Clamp holds the material down, against the table base, and
is mounted through and on top of the fence bracket. Both clamps are offered as optional extras and are highly recommended.
If you purchased your machine with an Air Downfeed of the saw, the clamps are actuated prior to activating saw head by
depressing the Foot Valve. An Anti-Tie Down, Two Hand Control drives down the sawhead. If clamps are purchased using
a hand operated machine, then the clamps will move into position by pulling the saw head down slightly. This releases the
Automatic Valve (AV) to supply air to the clamps.
Be careful not to overtighten clamp cylinder bracket
on the
cylinder. This will cause irregular function of the cylinder.
200R Vertical Clamp Assembly
200R Horizontal Clamp Assembly
-9-
1/4” elbow fitting
B3P61
shut off
valve
200M22
vert. cyl.
brkt.
2B3P20
3” stroke
air cyl.
2B3P20C
vert. clamp
pad
200BIP22
wing nut
VC
1/4” red polyflo line
200B7P19
adjustable
lock handle
200M21
vert. clamp
adjustment
brkt.
200M20B
horiz. bar adj.
for vert. clamp
200M20C
vert. clamp
support bar
2BM28
horiz. clamp
pad
200B3P21
3” stroke
air cyl.
200M27
horiz. clamp
key
B3P61
shut off
valve
1/4” elbow fitting
1/4” red polyflo line
200B7P19
adjustable
lock handle
200M22
vert. cyl.
brkt.
4. Turn mitre locking handle to center position, and the spring loaded pin & handle will automatically engage into
preset angle settings. The preset angle settings are 45
°
, 30
°
, 22 ½
°
, 15
°
, 0
°
on both sides of the centerline or zero
point.
Do not let the spring loaded mitre locking pin & handle engage in several degree settings as
you rotate the mitre base disc. This will cause excess wear on preset angle settings.
5. For all angles that are not preset, follow instructions under #1 to lock handle in the open position.
Simply align degree quadrant on disc with zero mark on base and tighten down intermediate mitre lock handle
located in base.
Содержание CM325R
Страница 8: ...WiringDiagrams...
Страница 9: ......
Страница 21: ...19 LEFT OPPOSITE 200 SERIES RIGHT SAW ASSEMBLY...
Страница 23: ...21 200 Series Right Blade Guard Assy Left Opposite REAR VIEW...
Страница 26: ...24 Air Feed System Exploded View...
Страница 27: ...25 CM325R Left Saw Assembly Right Opposite...
Страница 29: ...27 CM325R Left Base Assy Right Opposite...
Страница 30: ...M25HC Base Assembly Exploded View 28...
Страница 31: ...200HC Series Blade Guard Assembly 29...
Страница 33: ...Notes...