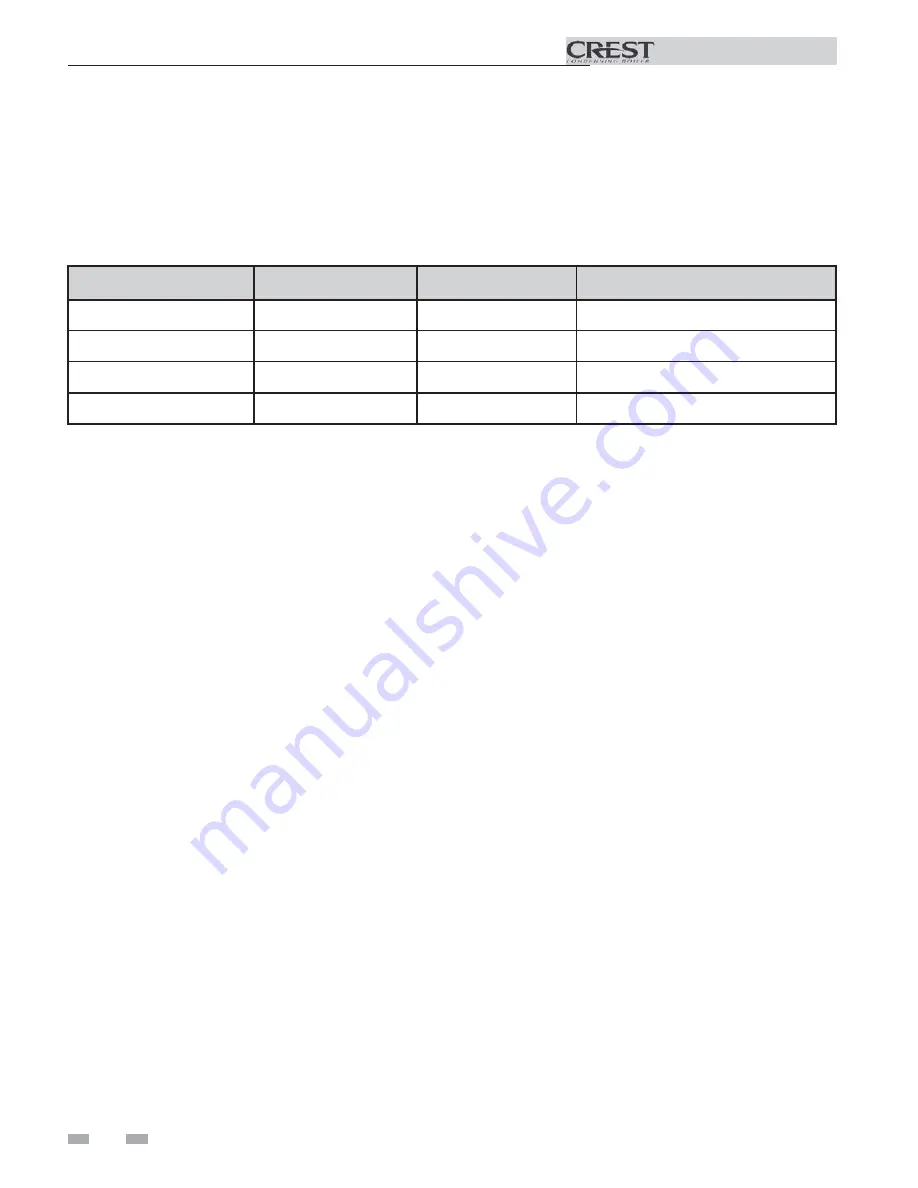
16
5
Unit Operation
Cascade
In order to operate the Crest boiler in Cascade with ModBus
communications, confi gure the leader boiler per the demand
confi gurations in this manual. Connect the remaining boilers
in the cascade through the normal cascade communications
wiring. Cascade control can then be accomplished
automatically through the leader boiler.
Please note that with ModBus communication connected to
only the leader boiler, total Cascade information can be seen
through the communications link. If you wish to see all the
individual temperatures of each unit in the Cascade, each unit
will have to have a ModBus communication board. However,
each unit can be monitored without the need to control each
one individually.
DHW with remote control:
This installation may or may not have the hot water generator in close proximity to the boiler. Its sensors and thermostat values
are only available through the ModBus communication bus.
To ensure that the Crest boiler can properly respond to a call for hot water generation the following holding registers must be
set in addition to other commands:
Holding Registers
Defi nition
Bit Value (HEX)
Action
40001
Confi guration
00 4A
Set Confi guration to read 40002, 4 & 5
40002
Coils
00 08
Enables Tank Tstat
(00 00 disables unit)
40004
Tank Setpoint
0# ##
Sets Setpoint
40005
Tank Temperature
0# ##
Passes tank temp from remote sensor
For proper hexadecimal conversion of rate percentage, please refer to the Rate and Temperature Conversion section on page 17
of this manual.
NOTE:
To ensure proper operation re-send the confi guration bits to holding register 40001 prior to issuing a command.
Monitoring Only
All Crest boilers are equipped with the ModBus communication
board and can be set up to operate with its own internal controls.
If necessary, ModBus can be confi gured as a monitoring device
by polling the ModBus board for the read only variables.
ModBus Instructions