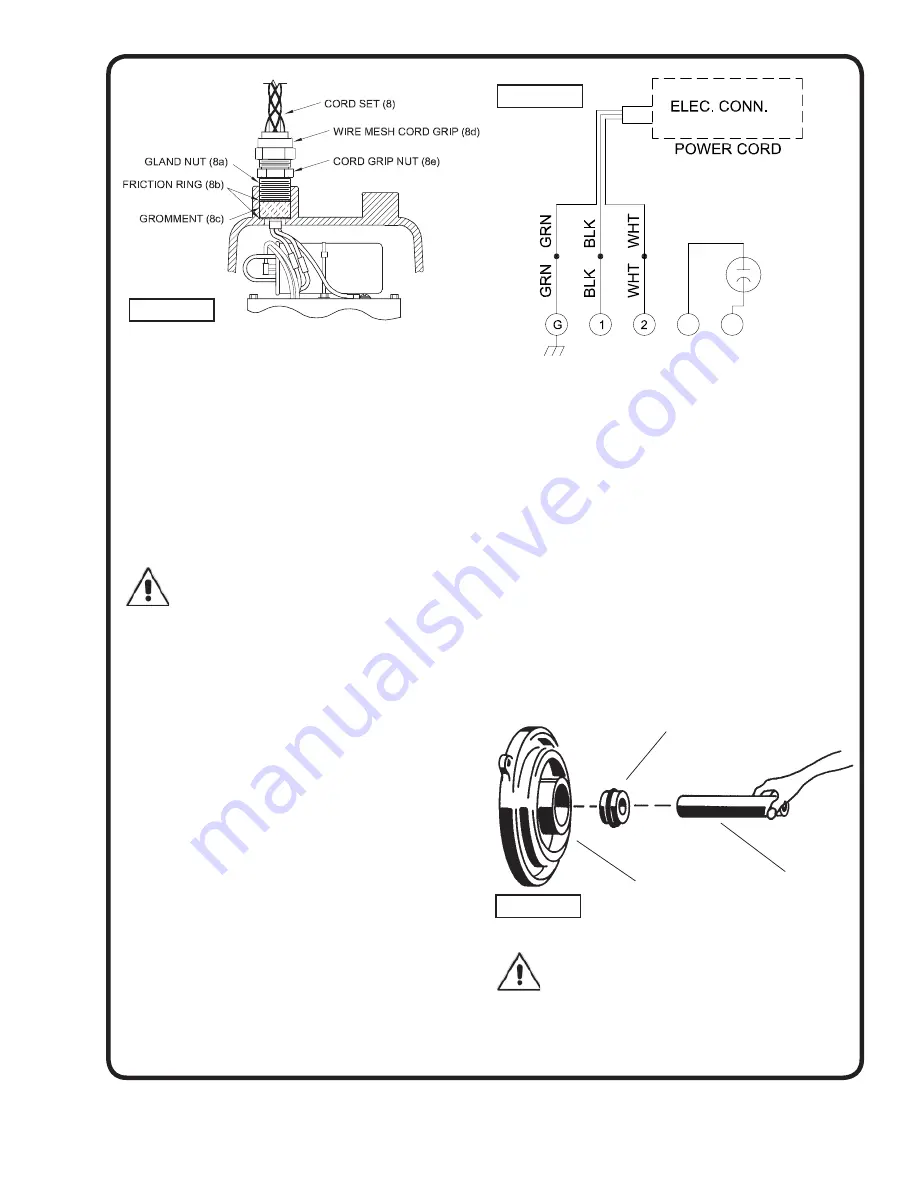
9
Loosen motor screws and pull motor (1) straight up and off
seal plate (2). Inspect all parts for signs of wear and check
motor resistance values. Check capacitor (6) with an Ohm
meter by grounding the capacitor by placing a screwdriver
across both terminals and then removing the screwdriver.
Connect Ohm meter (set on high scale) to terminals, if
needle moves to infi nity (
∞
) then drifts back, the capacitor
is good. If needle does not move or moves to infi nity (
∞
)
and does not drift back, replace capacitor (6).
Bearings -
Disassemble motor as per section F-3.1.
Remove snap ring (5) with snap ring pliers and pull motor
(1) and lower bearing (4) straight off of seal plate (2).
Inspect all parts for signs of wear and replace as needed.
CAUTION: - Handle seal parts with extreme
care. DO NOT scratch or mar lapped surfaces.
All parts must be clean before reassembly.
F-3.2) Replacing Bearing:
When replacing bearing, be careful to not damage the rotor
or shaft threads. Press the old bearing off the shaft with
an arbor press or gear puller. Clean the shaft thoroughly.
Apply adhesive compound to shaft and press new bearing
on, pushing only on the inner race, until it seats against
shoulder of shaft (see fi g.8).
F-3.3) Reassembly:
Make sure shaft seal (3) is clean and in proper position as
per section F-4.2 before reassembling rotor and bearing.
Slide lower bearing and rotor shaft squarely into the seal
plate (2) until bearing seats on the bottom. Insert snap
ring (5) into seal plate with fl at edge against outer race of
bearing. Place motor stator squarely onto seal plate (2) and
tighten motor screws. Install o-ring (11) onto seal plate (2).
Slide the gland nut, friction rings and grommet onto cord
set (see Figure 5) and slip cord through motor housing (12).
Connect motor wires per Figure 6. Place motor housing (12)
squarely onto seal plate while pulling excess cord through
hole. Tighten socket head screws (13) into motor housing.
Slide the friction rings (8b), grommet (8c) and gland nut
(8a) into motor housing and tighten gland nut to 17.5 ft. lbs.
Attached cord grip nut (8e) and wire mesh cord grip (8d)
onto gland nut (8a) and tighten. Refi ll with cooling oil as per
paragraph F-1.3.
F-4) Shaft Seal Service
F-4.1) Dissassembly and Inspection:
Disassemble pump motor as per section F-3.1. Inspect
seal for signs of wear such as uneven wear pattern on the
stationary member or chips and scratches on either sealing
face. Do not interchange seal components. Replace entire
seal if damage occurs.
F-4.2) Replacing Shaft Seal:
When replacing the shaft seal (3), remove used rotating
member (3c), spring (3b), and spring retainer (3a) from
motor shaft. Press used stationary member (3d) from the
seal plate (2). At reassembly, clean seal cavity thoroughly
and apply a light coat of oil. Lightly oil the rubber ring
(DO
NOT use grease)
and press the stationary member fi rmly
into the seal plate using a seal pusher (See Parts List-
Seal Tool Kit), nothing but pusher to come in contact with
seal face (see Fig. 7). Insert so that the fi nished surface
is up and the grooved surface is against the seal plate.
Make sure the stationary member is in straight and that the
rubber ring is not out of it’s groove.
DO NOT HAMMER ON THE SEAL PUSHER - IT
WILL DAMAGE THE SEAL FACE.
FIGURE 5
FIGURE 6
Seal Pusher
Seal Plate
Stationary Member
(3d) Polished Face Out
FIGURE 7
Содержание Barnes SE411HT
Страница 12: ...12 FIGURE 10 ...
Страница 16: ...Notes ...