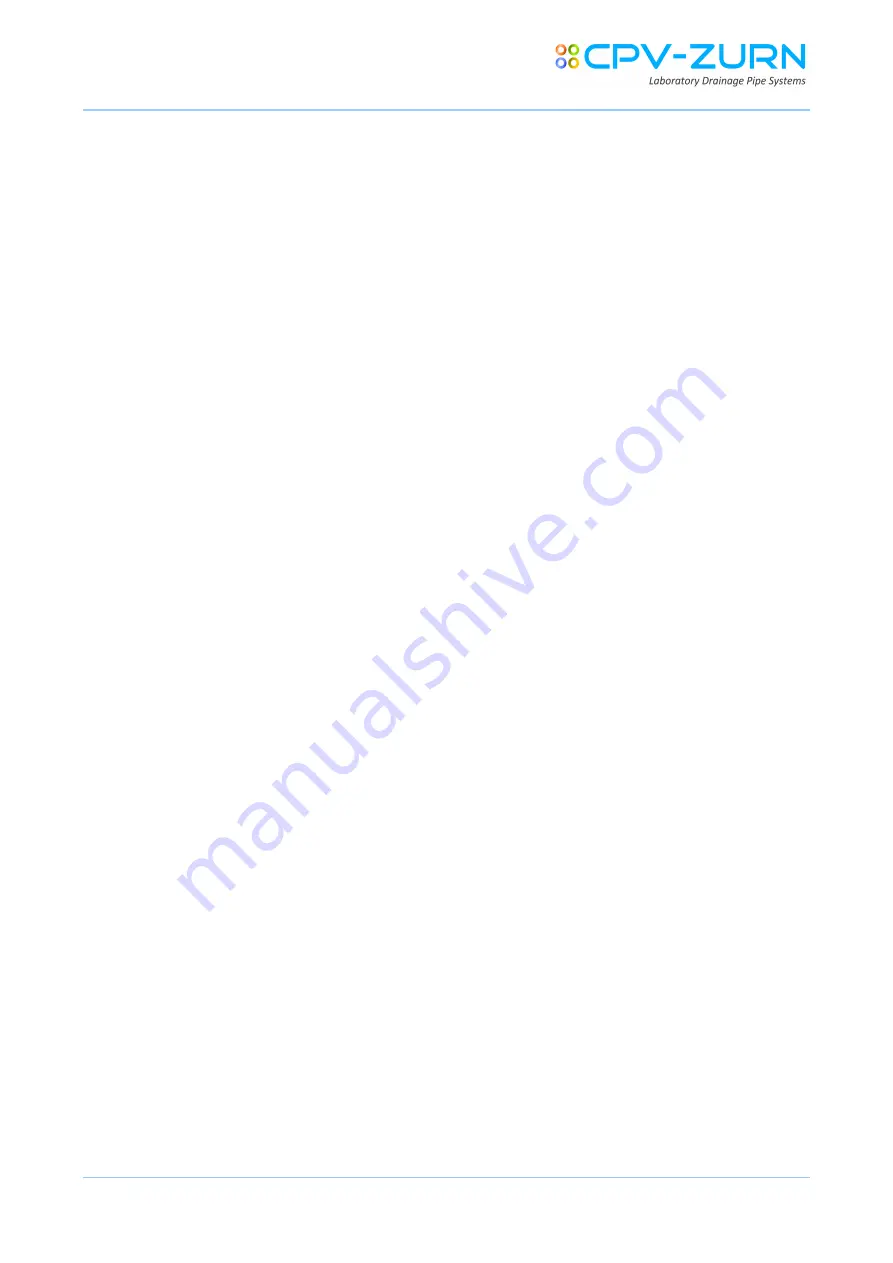
Electrofusion Welder
26/07/2011
www.LaboratoryDrainage.co.uk
Pg 15
SWUD
Update the software.
The internal software can be upgraded. Copy the new software (supplied
by Advance Welding) onto a USB memory pen and plug it into the USB
connector on the side of the box. Enter the password. When prompted
press the A key to accept. The software will now be updated. When
completed the screen will show “Success!”. Unplug the welding unit from
the power supply to complete the process.
DLEN
Set download to plain text.
The data download will be a Common Separated Variable (csv) file, with a
.xls extension. This can either be viewed in the Advance Welding Data
Download Manager or in Microsoft Excel.
DLEY
Set download to encrypted.
The data download will be an encrypted file, with a .pfd extension. This
can only be viewed in the Advance Welding Data Download Manager.
AWHD
Download all welds, including non-logged.
This password will download all welds, including those done when the
unit was not set to data logging mode. All visible and hidden welds are
downloaded. The hidden, non-logged welds, will show blank in the
operator input fields.
Other passwords are available for authorised repair centres. These
include calibration, changing owner details and setting/showing the
distributor selling data.
Содержание Zurn
Страница 1: ...Electrofusion Welder ...
Страница 28: ......