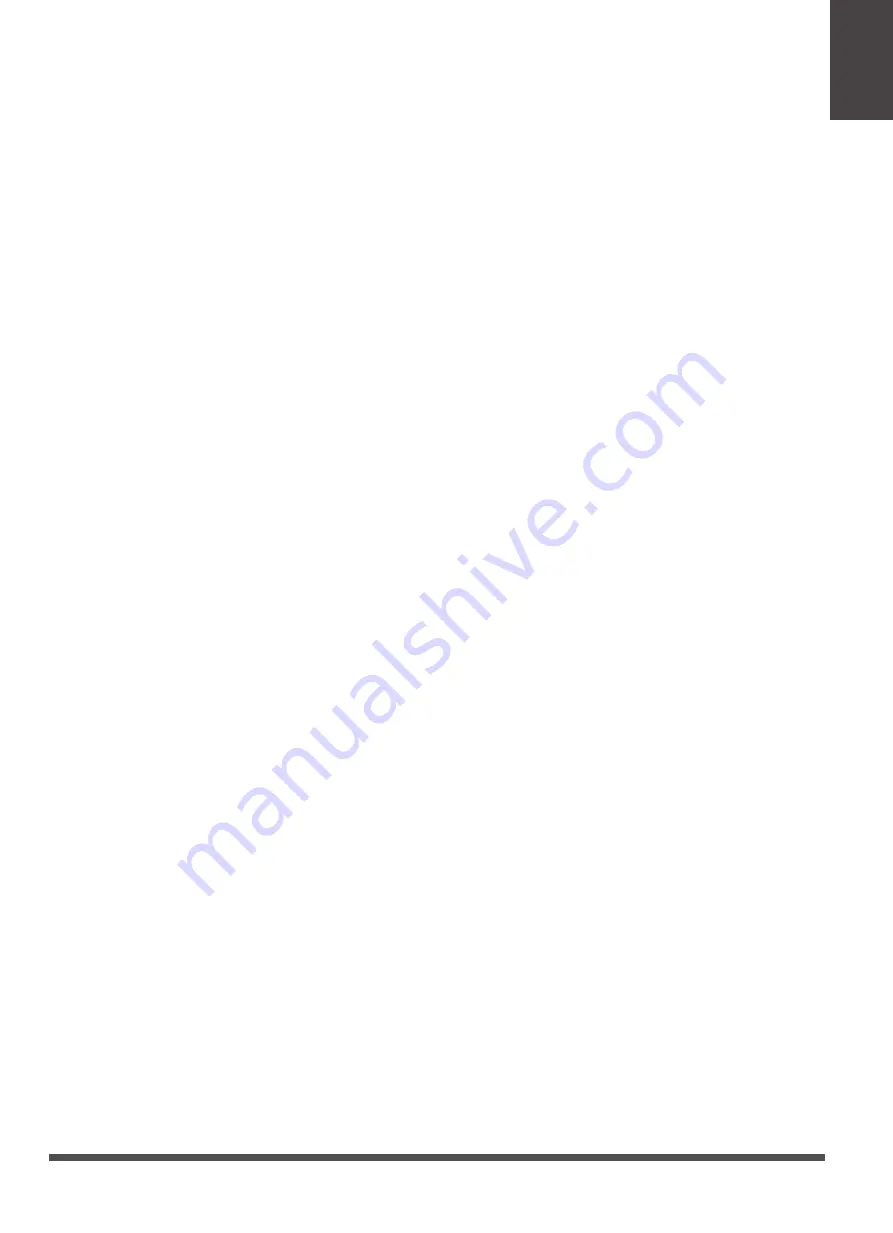
Safety
Precautions
Page 9
and shall be calibrated to the refrigerant employed and the appropriate percentage of gas (25 %
maximum) is confirmed. Leak detection fluids are suitable for use with most refrigerants but the use of
detergents containing chlorine shall be avoided as the chlorine may react with the refrigerant and
corrode the copper pipe-work. If a leak is suspected, all naked flames shall be removed/ extinguished.
If a leakage of refrigerant is found which requires brazing, all of the refrigerant shall be recovered from
the system, or isolated (by means of shut off valves) in a part of the system remote from the leak.
Oxygen free nitrogen (OFN) shall then be purged through the system both before and during the
brazing process.
When breaking into the refrigerant circuit to make repairs or for any other purpose conventional
procedures shall be used. However, it is important that best practice is followed since flammability is a
consideration. The following procedure shall be adhered to:
Remove refrigerant; Purge the circuit with inert gas; Evacuate; Purge again with inert gas; Open the
circuit by cutting or brazing.
The refrigerant charge shall be recovered into the correct recovery cylinders. The system shall be flushed
with OFN to render the unit safe. This process may need to be repeated several times. Compressed air or
oxygen shall not be used for this task. Flushing shall be achieved by breaking the vacuum in the system
with OFN and continuing to fill until the working pressure is achieved, then venting to atmosphere, and
finally pulling down to a vacuum. This process shall be repeated until no refrigerant is within the system.
When the final OFN charge is used, the system shall be vented down to atmospheric pressure to enable
work to take place. This operation is absolutely vital if brazing operations on the pipe-work are to take
place. Ensure that the outlet for the vacuum pump is not close to any ignition sources and there is
ventilation available.
10.Detection of flammable refrigerants
The following leak detection methods are deemed acceptable for systems containing flammable
refrigerants. Electronic leak detectors shall be used to detect flammable refrigerants, but the sensitivity
may not be adequate, or may need re-calibration. (Detection equipment shall be calibrated in a
refrigerant-free area.) Ensure that the detector is not a potential source of ignition and is suitable for
the refrigerant used. Leak detection equipment shall be set at a percentage of the LFL of the refrigerant
11.Leak detection methods
Check that cabling will not be subject to wear, corrosion, excessive pressure, vibration, sharp edges or
any other adverse environmental effects. The check shall also take into account the effects of aging or
continual vibration from sources such as compressors or fans.
9.Cabling
12.Removal and evacuation
13.Charging procedures
In addition to conventional charging procedures, the following requirements shall be followed. Ensure
that contamination of different refrigerants does not occur when using charging equipment. Hoses or
lines shall be as short as possible to minimise the amount of refrigerant contained in them.
Cylinders shall be kept upright.
Ensure that the refrigeration system is earthed prior to charging the system with refrigerant.
Label the system when charging is complete (if not already).
Extreme care shall be taken not to overfill the refrigeration system. Prior to recharging the system it
shall be pressure tested with OFN. The system shall be leak tested on completion of charging but prior
to commissioning. A follow up leak test shall be carried out prior to leaving the site.
Under no circumstances shall potential sources of ignition be used in the searching for or detection
of refrigerant leaks. A halide torch (or any other detector using a naked flame) shall not be used.
Содержание CH-D014WDR20
Страница 19: ......
Страница 22: ...03 13 15 14 17 17 18 17 17 11 11 12 12 12...
Страница 23: ...Safety 3...
Страница 24: ...4 8 15 250...
Страница 25: ...5 R290 1 CO2 2 3...
Страница 26: ...6 R32 R290 4 R32 R290 2...
Страница 27: ...7 2 6 1 1 2 3 4 5 3 4 5 CO2 6 7...
Страница 28: ...8 8 1 2 9 7 8...
Страница 29: ...9 10 11 LFL 25 OFN 9 12 OFN OFN OFN 13...
Страница 30: ...10 15 16 14 80...
Страница 31: ...11...
Страница 32: ...24 5 C 41 F 32 C 90 F 30 RH 80 RH 20 40 5 C 41 F 5 C 41 F 12 1 1 1 20 40 20 20 40...
Страница 34: ...35 85 5 0 24 POWER 0 COMFORT 14 Bucket Full Light 30 3 3 3 ION 35 85 0 24 5 30 90 AS ES P2 P2 Eb...
Страница 35: ...15 250 Auto Stop Auto Start Auto Start Auto Stop 0 5 10 1 24 5 On Off 0 0 P2 1 1 P2 1 2 3...
Страница 36: ...16 8 Eb 8 Eb 1 4 15 2 5 16 ID M1 3 3 5 1...
Страница 37: ...17 0 C 32 F 13 2 1...
Страница 38: ...18 5 C 41 F ES AS P2 Eb 1Hz...
Страница 39: ......