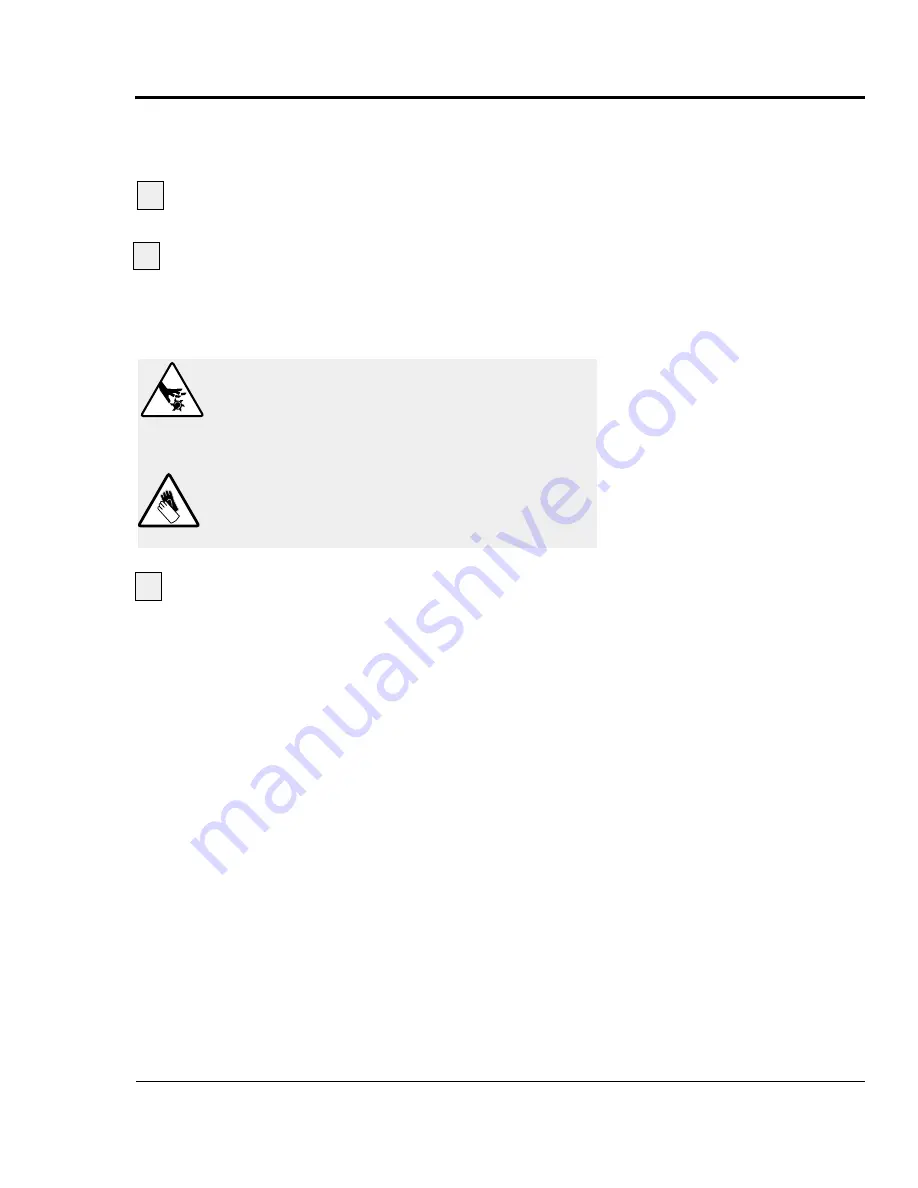
The home position proximity switch should be 0.010 inch
from the 5/16 inch thread rod on the cutter head for proper
operation.
Open the flywheel clear guard window.
Locate the 5/16 inch thread rod on the cutter
head.
It should be 0.010 inch from the proximity switch
sensor when it passes that location. If necessary, loosen
the jam nuts, readjust the distance, and re-tighten the jam
nuts.
If the proximity switch does not sense
the cutter
head after this adjustment, remove the switch and test it
outside the cutter. Replace if necessary.
A
DJUSTING THE
P
ROXIMITY
S
WITCHES
DANGER: Sharp blades!
Always wear cut-resistant gloves when the cut-
ting chamber is open and when handling
blades. Never open cutting chamber without
locking out the cutter power.
Most injuries caused by knife blades occur
when the cutter has been turned off. Handle
blades with care at all times.
1
2
3
T
ROUBLESHOOTING
6-13
UGE059/1003
SC-5 SURE CUT Servo Knife Cutter