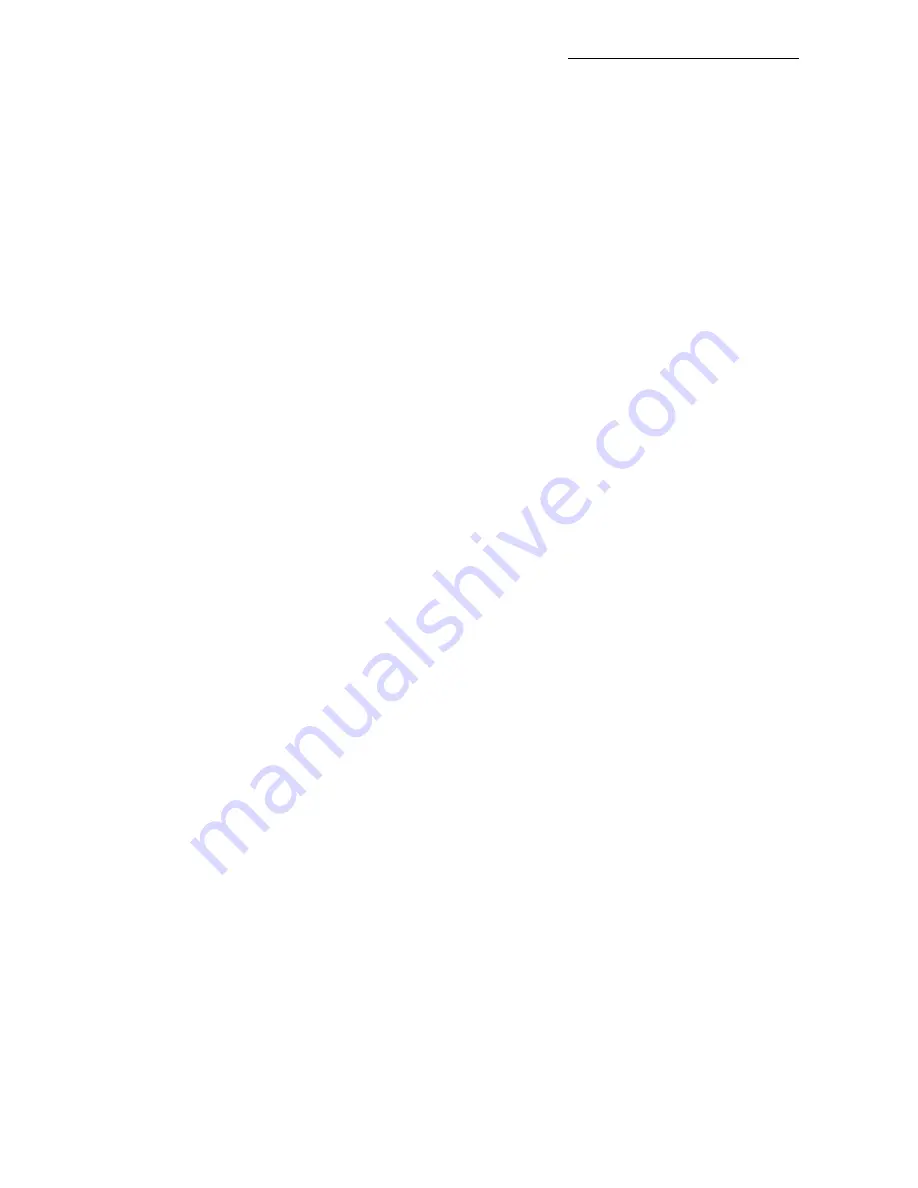
years. Fit 4 hi-torque digital servos (JR8411 or 8511/8611 or Futaba 9351 recommended) into
the cnc milled phenolic plate provided, as shown in photos P13 and 14. Mount the plate onto the
carbon/plywood main board using the rubber grommets and 2.9mm Ø x 13mm screws provided
in the same manner as the elevator servo set-up.
Assemble the pear-shaped phenolic servo output arms (provided) as shown, and glue to large
diameter plastic servo output discs. Rough up the surfaces of the discs and the phenolic well to
ensure good adhesion. Secure with at least two 2.2Ø x10mm screws through each, as shown.
Set all servos and arms at neutral using your R/C, and connect the 2 pairs of servos together
using the M3 ball links, clevises and locknuts provided. Adjust lengths of linkages carefully to
make sure that the servos are not fighting each other at neutral and full throws. Note the wash-
ers used on top of the M3 securing bolts to ensure that the ball-links cannot come off. See pho-
tos 13 and 14.
Servos:
The rudder is a huge surface on the Pitts - which definitely needs hi-torque power ser-
vos, and we highly recommend at least the digital JR/Graupner 8411’s or Futaba 9351’s for this
important surface.
Make up the closed loop wires for the rudder from the hardware supplied, with a loop at the front
that goes over the hooks on the output arms, and a quick-link with turnbuckle and locknut at the
rudder end. For security pass the closed loop cable through the supplied ‘crimping tubes’ 3 times
before squashing flat with large pliers. Note that the rudder cables should be ‘crossed’ over in
the fuselage (see photo P12). This photo also shows the 3mm balsa plate (supplied) that must
be glued across the back of the fuselage to keep the rudder cables separated from each other.
Make sure that the wires are tight, and check and adjust after the first few flights as the cables
straighten out. Even a small amount of slop will prevent your Pitts from perfect tracking, and may
allow flutter. Make sure that the cables cannot come out of the slots in the phenolic arms on the
servos with a small scrap of balsa glued across the slots as shown in the photos.
Wings
The wings are 95% finished at the factory, and have already been installed on your fuselage to
check alignment. They fit onto 30mm Ø aluminium alloy spar tubes. The bottom wings are
secured to the fuselage with a pair M6 plastic knurled nuts onto the aluminium anti-rotation pins.
The top wings have carbon anti-rotation pins that locate into the centre section, and are each
secured with one M6 x 50mm bolt that goes thru’ the slots in the underside of he wings into M6
blind nuts that are fitted into the centre section at the factory.
Servo choice:
We highly recommend using 2 hi-torque digital servos of at least 10kg torque (eg:
JR/Graupner 8411/8511/8611 or Futaba 9351) for each aileron as the surfaces are quite large.
The servo hatches are pre-cut in the wing, and supplied with matching servo covers and CNC
milled plywood servo mounts for the JR8511/8611 servos. Rough sand the inside surface of the
servo hatch covers and the milled plywood parts that make up the servo mounts to make sure
you have a good gluing surface.
Assemble the servo mounts from the milled plywood parts for each servo, using thin CA and a
90° square (see photo P16). Fix the servos into the mounts with the 2.9Ø x13mm screws sup-
plied in the kit, and place them on the hatch covers to check that the servo arms are in the cen-
Composite-ARF Pitts S12
9