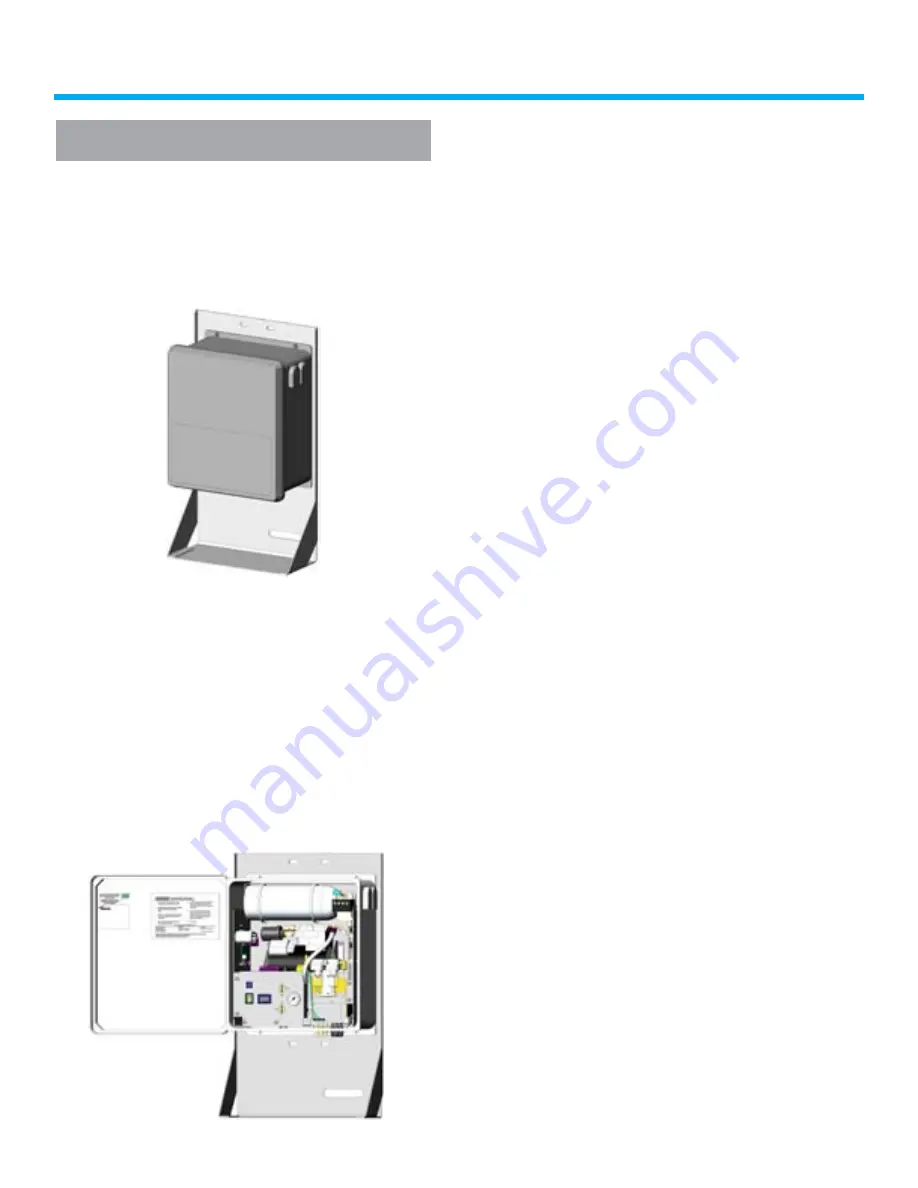
ODPMT200 Series DryLine® Dehydrator User Manual
3
This manual contains the information you need
to install, operate and maintain your ODPMT200
Series DryLine™ dehydrator. Please take the
time to read this manual before attempting to
operate or service the unit.
ODPMT200 Series dehydrators provide dry air
for pressurizing small (up to 40 cubic feet, or
560 liters, in volume) antenna and transmission
line systems. The dehydrators produce -49ºF
(-45ºC) dewpoint dry air at an output rate of 0.2
cubic feet (1.4 liters) per minute.
Each dehydrator consists of an electrically-
driven air compressor, a membrane dryer
assembly, an automatic transmission line
pressure sensing system and a low-pressure
alarm output housed in a rigid metal chassis.
They are designed to mount to a slab floor.
Optional brackets are available for pole
mounting capability. Their front panels feature
a pressure gauge, an indicating on/off switch, a
resettable circuit breaker, and a run time meter.
For easy serviceability, power connections,
alarm output connections and all filter elements
are accessible from the front of the unit.
The ODPMT200 maintains transmission line
pressures at 5.0 lb/in2 (34 kPa). It is intended
for standard microwave antenna applications
and any other transmission line pressurization
requirement that supports a relatively high
pressure limit.
ODPMT200 Theory of operation.
The ODPMT200 series of DryLine™
dehydrators, while similar in moisture removal
technology, operates differently than the rest of
the DryLine™ series of dehydrators. In order to
provide a constant supply of dry air to small air
volume systems, and to maintain an acceptable
moisture level in the product air stream, a high-
pressure reservoir tank is needed. This reservoir
tank is connected to a pressure regulator and
orifice to yield a fixed output pressure of 5.0 psig
and a nominal flow rate of 0.2 CFM. In addition
to supplying the output air, the reservoir tank
also provides the dry air for the feedback loop.
The feedback loop is necessary to maintain the
dryness of the membrane cartridge.
During normal operation, the bleed air in the
feedback loop will cause the pressure to drop in
the internal reservoir tank, and the ODPMT200
compressor will cycle automatically. These
cycles will take place regardless of the system
volume or condition of the transmission line the
dehydrator is connected to. The rate of these
cycles, however, will vary. During the purge
cycle, the dehydrator will cycle approximately
every 2 to 4 minutes while showing 0 psig on
the pressure gauge and providing a constant 0.2
SCFM of dry air.
When connected to a very tight system, or
the output is capped, the dehydrator will
cycle approximately every 60 to 90 minutes
and maintain 5.0 psig system pressure while
providing close to 0 CFM of dry air. A system
that leaks will have a cycle time somewhere in
between, depending on the severity of the leaks.
Содержание DryLine ODPMT200 Series
Страница 14: ...ODPMT200 Series DryLine Dehydrator User Manual 14 Figure 3 Schematic With All Options ...
Страница 15: ...ODPMT200 Series DryLine Dehydrator User Manual 15 Figure 4 Alarm s ...
Страница 18: ...ODPMT200 Series DryLine Dehydrator User Manual 18 This page was left blank ...
Страница 20: ...ODPMT200 Series DryLine Dehydrator User Manual 20 This page was left blank ...