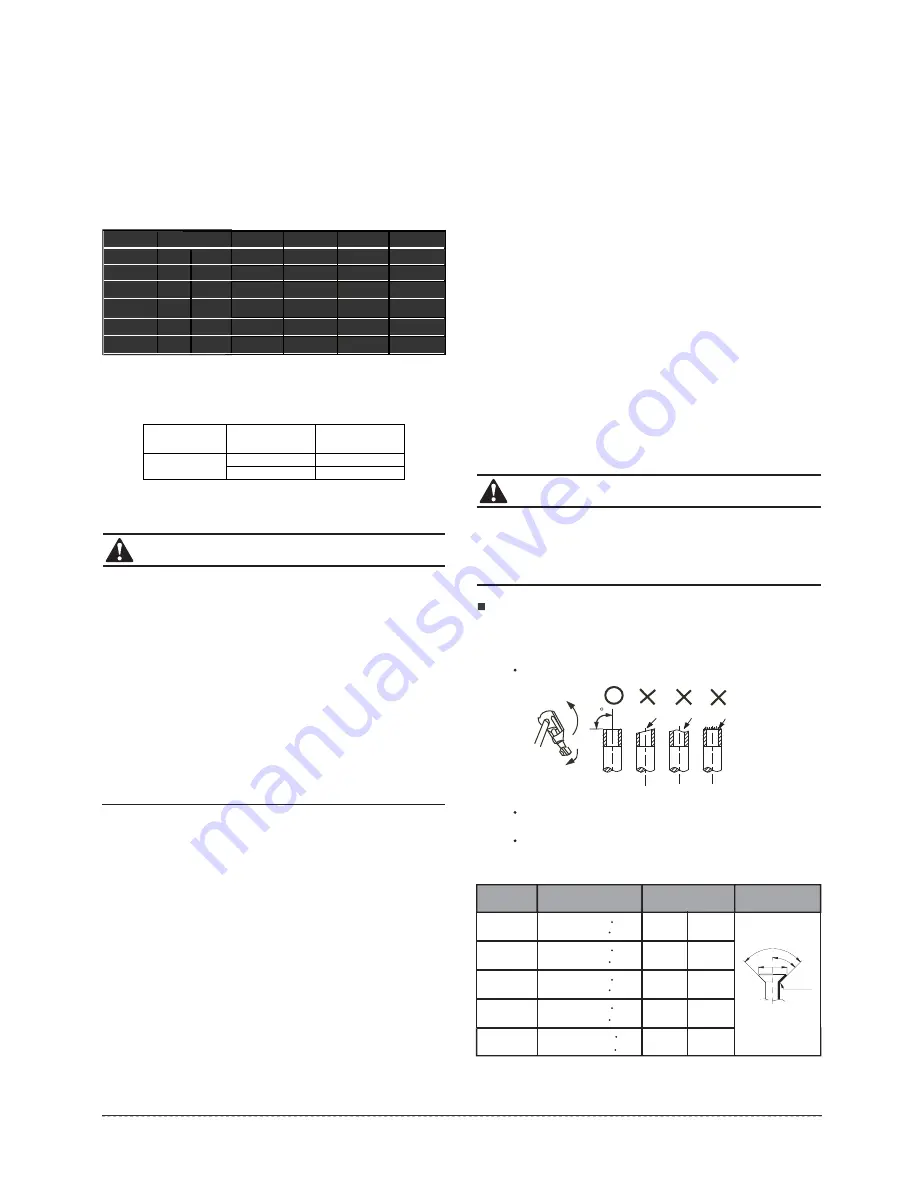
CAUTION
8. INSTALL THE CONNECTING PIPE
Check whether the height drop between the indoor unit
and outdoor unit, the length of refrigerant pipe, and the
number of the bends meet the following requirements:
All field piping must be provided by a licensed
refrigeration technician and must comply with the
relevant local and national codes.
Do not let air, dust, or other impurities fall in the pipe
system during the time of installation.
The connecting pipe should not be installed until the
indoor and outdoor units have been fixed already.
Keep the connecting pipe dry, and do not let moisture in
during installation.
The Procedure of Connecting Pipes
8.1
Table 8-1
CAUTION
How to connect the pipes
Drill a hole in the wall (suitable just for the size of the wall
conduit), then set on the fittings such as the wall conduit and
its cover.
Bind the connecting pipe and the cables together tightly with
binding tapes.
Pass the bound connecting pipe through the wall conduct
from outside. Be careful of the pipe allocation to do on
damage to the tubing.
Connect the pipes. Refer to "How to Connect the pipes" for
details.
Expel the air with a vacuum pump. Refer to "How to expel the
air with a vacuum pump" for details.
open the stop values of the outdoor unit to make the
refrigerant pipe connecting the indoor unit with the outdoor
unit in fluent flow.
Check the leakage. Check all the joints with the leak detector
or soap water.
Cover the joints of the connecting pipe with the soundproof /
insulating sheath (fittings), and bind it well with the tapes to
prevent leakage.
Execute heat insulation work completely on both sides of
the gas piping and the liquid piping. Otherwise, this can
sometimes result in water leakage.
1
2
3
5
6
7
4
Be sure to with insulating materials cover all the exposed
parts of the flare pipe joints and refrigerant pipe on the
liquid-side and the gas-side. Ensure that there is no gap
between them.
Incomplete insulation may cause water condensation.
Flaring
1
Cut a pipe with a pipe cutter.
(refer to Fig.8-1)
Ta b le 8-2
Ø6.4
8.3 8.3
Ø9.5
12.0 12.4
Ø12.7
15.4 15.8
Ø15.9
Ø19.1
18.6 19.0
22.9 23.3
R0.4~0.8
45
°±
2
90
°
±
4
A
Insert a flare nut into a pipe and flare the pipe.
Refer to Table 8-2 for the dimension of flare nut spaces.
Fig.8-1
Pipe gauge
Tightening torque
Flare dimensin A
Flare shape
90
Lean crude burr
11
installation manual
min max
(mm)
14.2
~
17.2 N m
(144
~
176 kgf cm)
32.7
~
39.9 N m
(333
~
407 kgf cm)
49.5
~
60.3 N m
(504
~
616 kgf cm)
61.8
~
75.4 N m
(630
~
770 kgf cm)
97.2
~
118.6 N m
(990
~
1210 kgf cm)
Csapacit
Btu/h
12k
18k
24k
36k
48k
Ptipe size
GAS
LIQUID
12'
12'
(Ø12.7)
12'
(Ø12.7)
58''
(Ø16.0)
58''
(Ø16.0)
58''
(Ø16.0)
38''
(Ø9.52)
38''
(Ø9.52)
38''
(Ø9.52)
14''
(Ø6.35)
(Ø6.35)
14''
Ptipe size
Standard
length
Max.
Elevation
Standard
length
Max.
Lenth
Additional
refrigerant
(ft)
(ft)
(ft)
(oz/ft)
25
25
25
25
25
98
98
82
66
33
213
164
98
82
213
213
0.320
0.160
0.160
0.320
0.320
Some systems require additional charging depending on pipe lengths. The standard pipe length
varies according to local regulations. In North America, the standard pipe length is 7.5m (25ft).
The additional refrigerant to be charged can be calculated using the following formula:
Diameter of liquid pipe
(mm)
Φ6.35mm
(
1/4 in
)
Φ9.52 (3/8 in)
Formula
V=15g/m×(L-7.5)
V=30g/m×(L-7.5)
V=0.16oz/ft x (L-25ft)
V=0.32oz/ft x (L-25ft)