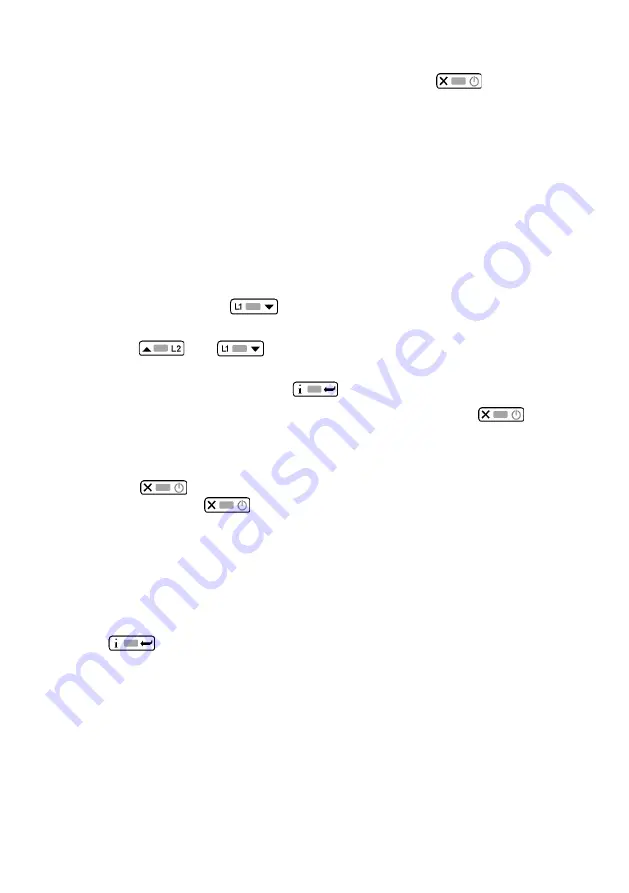
off when in programming mode. If approximately 25 seconds elapse while in
programming mode with out a key being pressed the CN-200D controller will activate
with the last preset parameters. Furthermore by pressing the key from any
condition the unit will revert back to Function mode.
7.6. Configuration
7.6.1. Enter Programming mode as described in paragraph 7.11 The available parameters in
the configuration menu are as shown in the table on pages 15 to 17.
7.6.2. Only channel 1 / output 1 is active on the CN-200D controller. Other available
parameters are disabled through the factory default settings.
Please Note:-
Should any of the parameters become altered accidentally, they may
be restored to their factory settings by programming the values shown on page 18.
7.7. Entering the Set point (Channel 1 only)
7.7.1. Press and release button . Observe the display shows 1SP and the LED L1
blinks and then the associated value.
Press the and to set the desired value (adjustment is within the
minimum SPL and maximum SPH limit).
To store the new value press button or wait 10 seconds.
To return to operational mode without saving the settings press the Exit /
standby button.
7.8. Stand-By
7.8.1. Press the button and wait for the 3 seconds. The word ‘OFF’ will be displayed.
To resume press the button once again for another 3 seconds and the display
will return to normal operation.
7.9. Keypad Lock
7.9.1. The keypad lock avoids undesired and potentially dangerous operation, which might
be attempted while the controller is in operation. In the INFO menu, set the parameter
to LOC=Yes to inhibit all of the function buttons. To resume normal operation of the
keypad, adjust the parameter setting to LOC=No. This is accessed by pressing
the and immediately releasing it.
7.10. Controller Auto-tuning in PID mode
Before commencing
7.10.1. In the setup mode (see configuration 7.6) set 1CM=PID; make sure that 1CH matches
the desired operation mode (1CH=REF for refrigeration control, 1CH=HEA for heating
control); then adjust set-point 1SP at the desired value.
13
Page 12 of 24 M6493 Issue 10.3
7.3.3. Proportional, Integral and Derivative Control.
A proportional controller continuously adjusts the power, so the heat input to
the process is approximately in balance with the process heat requirements
in order to maintain a stable temperature. The range of temperature over
which power is adjusted is from 0% to 100%. This temperature range is
called the ‘Proportional Band’. The proportional band is adjustable for
differing process conditions (zero proportional band returns the controller to
basic on / off control).
The temperature difference between the stabilised temperature and the set
point is called the ‘Offset’. The offset can be reduced by adjusting the integral
term of the PID controller. This is achieved using the integrative action time
and integrative action reset.
A derivative function can be combined with the proportional controller to
provide the controller with the ability to shift the proportional band either up to
or down to compensate for rapidly changing temperature (i.e. when an oven
door is opened or cooler fluid is introduced into a controlled vessel). The
derivative function increases the controller gain during temperature changes,
and can help to reduce overshoot on start-up.
Hence, a three-mode PID controller combines the proportional, integral and
derivative actions, to allow the set point temperature to be approached
relatively smoothly with minimal overshoot.
7.4. Front Panel Controls
The MC810B controller has four front panel keys as described below.
7.4.1. The
key is used to increase the value of the parameter shown on
the display or to scroll through the parameter menu.
7.4.2. The
key is used to decrease the value of the parameter shown on
the display or to scroll through the parameter menu.
7.4.3. The
key is a dual function key. It is used to display and store the
value of the selected parameter when in ‘Programming’ mode. When used with
the
it is used to display the ‘Setpoint’ value.
7.4.4. The
is an ‘Exit / Stand-by button. Press of 3 seconds to turn unit on
or off.
7.5. Operating Modes.
7.5.1. The MB810B has two modes of operation: Function mode and Programming
mode. The unit enters Function mode immediately following power up in auto
test phase. In Function mode the display shows the temperature measured by
the temperature sensing probe. The output power will also be switched on or off
as appropriate. If the output power is on, the amber neon indicator on the front
panel will be illuminated. The only parameter which can be altered in the
function mode is the set-point. See 7.7.1
7.5.2. In Programming mode, all the other parameters apart from set-point can be
altered. To gain access to the programming mode from Function mode, press
the keys
and
. Keep them pressed for five seconds. The
output power is always off when in programming mode. If approximately 25
seconds elapse while in programming mode with out a key being pressed the
Page 12 of 24 M6493 Issue 10.3
7.3.3. Proportional, Integral and Derivative Control.
A proportional controller continuously adjusts the power, so the heat input to
the process is approximately in balance with the process heat requirements
in order to maintain a stable temperature. The range of temperature over
which power is adjusted is from 0% to 100%. This temperature range is
called the ‘Proportional Band’. The proportional band is adjustable for
differing process conditions (zero proportional band returns the controller to
basic on / off control).
The temperature difference between the stabilised temperature and the set
point is called the ‘Offset’. The offset can be reduced by adjusting the integral
term of the PID controller. This is achieved using the integrative action time
and integrative action reset.
A derivative function can be combined with the proportional controller to
provide the controller with the ability to shift the proportional band either up to
or down to compensate for rapidly changing temperature (i.e. when an oven
door is opened or cooler fluid is introduced into a controlled vessel). The
derivative function increases the controller gain during temperature changes,
and can help to reduce overshoot on start-up.
Hence, a three-mode PID controller combines the proportional, integral and
derivative actions, to allow the set point temperature to be approached
relatively smoothly with minimal overshoot.
7.4. Front Panel Controls
The MC810B controller has four front panel keys as described below.
7.4.1. The
key is used to increase the value of the parameter shown on
the display or to scroll through the parameter menu.
7.4.2. The
key is used to decrease the value of the parameter shown on
the display or to scroll through the parameter menu.
7.4.3. The
key is a dual function key. It is used to display and store the
value of the selected parameter when in ‘Programming’ mode. When used with
the
it is used to display the ‘Setpoint’ value.
7.4.4. The
is an ‘Exit / Stand-by button. Press of 3 seconds to turn unit on
or off.
7.5. Operating Modes.
7.5.1. The MB810B has two modes of operation: Function mode and Programming
mode. The unit enters Function mode immediately following power up in auto
test phase. In Function mode the display shows the temperature measured by
the temperature sensing probe. The output power will also be switched on or off
as appropriate. If the output power is on, the amber neon indicator on the front
panel will be illuminated. The only parameter which can be altered in the
function mode is the set-point. See 7.7.1
7.5.2. In Programming mode, all the other parameters apart from set-point can be
altered. To gain access to the programming mode from Function mode, press
the keys
and
. Keep them pressed for five seconds. The
output power is always off when in programming mode. If approximately 25
seconds elapse while in programming mode with out a key being pressed the
Page 12 of 24 M6493 Issue 10.3
7.3.3. Proportional, Integral and Derivative Control.
A proportional controller continuously adjusts the power, so the heat input to
the process is approximately in balance with the process heat requirements
in order to maintain a stable temperature. The range of temperature over
which power is adjusted is from 0% to 100%. This temperature range is
called the ‘Proportional Band’. The proportional band is adjustable for
differing process conditions (zero proportional band returns the controller to
basic on / off control).
The temperature difference between the stabilised temperature and the set
point is called the ‘Offset’. The offset can be reduced by adjusting the integral
term of the PID controller. This is achieved using the integrative action time
and integrative action reset.
A derivative function can be combined with the proportional controller to
provide the controller with the ability to shift the proportional band either up to
or down to compensate for rapidly changing temperature (i.e. when an oven
door is opened or cooler fluid is introduced into a controlled vessel). The
derivative function increases the controller gain during temperature changes,
and can help to reduce overshoot on start-up.
Hence, a three-mode PID controller combines the proportional, integral and
derivative actions, to allow the set point temperature to be approached
relatively smoothly with minimal overshoot.
7.4. Front Panel Controls
The MC810B controller has four front panel keys as described below.
7.4.1. The
key is used to increase the value of the parameter shown on
the display or to scroll through the parameter menu.
7.4.2. The
key is used to decrease the value of the parameter shown on
the display or to scroll through the parameter menu.
7.4.3. The
key is a dual function key. It is used to display and store the
value of the selected parameter when in ‘Programming’ mode. When used with
the
it is used to display the ‘Setpoint’ value.
7.4.4. The
is an ‘Exit / Stand-by button. Press of 3 seconds to turn unit on
or off.
7.5. Operating Modes.
7.5.1. The MB810B has two modes of operation: Function mode and Programming
mode. The unit enters Function mode immediately following power up in auto
test phase. In Function mode the display shows the temperature measured by
the temperature sensing probe. The output power will also be switched on or off
as appropriate. If the output power is on, the amber neon indicator on the front
panel will be illuminated. The only parameter which can be altered in the
function mode is the set-point. See 7.7.1
7.5.2. In Programming mode, all the other parameters apart from set-point can be
altered. To gain access to the programming mode from Function mode, press
the keys
and
. Keep them pressed for five seconds. The
output power is always off when in programming mode. If approximately 25
seconds elapse while in programming mode with out a key being pressed the
Page 12 of 24 M6493 Issue 10.3
7.3.3. Proportional, Integral and Derivative Control.
A proportional controller continuously adjusts the power, so the heat input to
the process is approximately in balance with the process heat requirements
in order to maintain a stable temperature. The range of temperature over
which power is adjusted is from 0% to 100%. This temperature range is
called the ‘Proportional Band’. The proportional band is adjustable for
differing process conditions (zero proportional band returns the controller to
basic on / off control).
The temperature difference between the stabilised temperature and the set
point is called the ‘Offset’. The offset can be reduced by adjusting the integral
term of the PID controller. This is achieved using the integrative action time
and integrative action reset.
A derivative function can be combined with the proportional controller to
provide the controller with the ability to shift the proportional band either up to
or down to compensate for rapidly changing temperature (i.e. when an oven
door is opened or cooler fluid is introduced into a controlled vessel). The
derivative function increases the controller gain during temperature changes,
and can help to reduce overshoot on start-up.
Hence, a three-mode PID controller combines the proportional, integral and
derivative actions, to allow the set point temperature to be approached
relatively smoothly with minimal overshoot.
7.4. Front Panel Controls
The MC810B controller has four front panel keys as described below.
7.4.1. The
key is used to increase the value of the parameter shown on
the display or to scroll through the parameter menu.
7.4.2. The
key is used to decrease the value of the parameter shown on
the display or to scroll through the parameter menu.
7.4.3. The
key is a dual function key. It is used to display and store the
value of the selected parameter when in ‘Programming’ mode. When used with
the
it is used to display the ‘Setpoint’ value.
7.4.4. The
is an ‘Exit / Stand-by button. Press of 3 seconds to turn unit on
or off.
7.5. Operating Modes.
7.5.1. The MB810B has two modes of operation: Function mode and Programming
mode. The unit enters Function mode immediately following power up in auto
test phase. In Function mode the display shows the temperature measured by
the temperature sensing probe. The output power will also be switched on or off
as appropriate. If the output power is on, the amber neon indicator on the front
panel will be illuminated. The only parameter which can be altered in the
function mode is the set-point. See 7.7.1
7.5.2. In Programming mode, all the other parameters apart from set-point can be
altered. To gain access to the programming mode from Function mode, press
the keys
and
. Keep them pressed for five seconds. The
output power is always off when in programming mode. If approximately 25
seconds elapse while in programming mode with out a key being pressed the
Page 12 of 24 M6493 Issue 10.3
7.3.3. Proportional, Integral and Derivative Control.
A proportional controller continuously adjusts the power, so the heat input to
the process is approximately in balance with the process heat requirements
in order to maintain a stable temperature. The range of temperature over
which power is adjusted is from 0% to 100%. This temperature range is
called the ‘Proportional Band’. The proportional band is adjustable for
differing process conditions (zero proportional band returns the controller to
basic on / off control).
The temperature difference between the stabilised temperature and the set
point is called the ‘Offset’. The offset can be reduced by adjusting the integral
term of the PID controller. This is achieved using the integrative action time
and integrative action reset.
A derivative function can be combined with the proportional controller to
provide the controller with the ability to shift the proportional band either up to
or down to compensate for rapidly changing temperature (i.e. when an oven
door is opened or cooler fluid is introduced into a controlled vessel). The
derivative function increases the controller gain during temperature changes,
and can help to reduce overshoot on start-up.
Hence, a three-mode PID controller combines the proportional, integral and
derivative actions, to allow the set point temperature to be approached
relatively smoothly with minimal overshoot.
7.4. Front Panel Controls
The MC810B controller has four front panel keys as described below.
7.4.1. The
key is used to increase the value of the parameter shown on
the display or to scroll through the parameter menu.
7.4.2. The
key is used to decrease the value of the parameter shown on
the display or to scroll through the parameter menu.
7.4.3. The
key is a dual function key. It is used to display and store the
value of the selected parameter when in ‘Programming’ mode. When used with
the
it is used to display the ‘Setpoint’ value.
7.4.4. The
is an ‘Exit / Stand-by button. Press of 3 seconds to turn unit on
or off.
7.5. Operating Modes.
7.5.1. The MB810B has two modes of operation: Function mode and Programming
mode. The unit enters Function mode immediately following power up in auto
test phase. In Function mode the display shows the temperature measured by
the temperature sensing probe. The output power will also be switched on or off
as appropriate. If the output power is on, the amber neon indicator on the front
panel will be illuminated. The only parameter which can be altered in the
function mode is the set-point. See 7.7.1
7.5.2. In Programming mode, all the other parameters apart from set-point can be
altered. To gain access to the programming mode from Function mode, press
the keys
and
. Keep them pressed for five seconds. The
output power is always off when in programming mode. If approximately 25
seconds elapse while in programming mode with out a key being pressed the
Page 12 of 24 M6493 Issue 10.3
7.3.3. Proportional, Integral and Derivative Control.
A proportional controller continuously adjusts the power, so the heat input to
the process is approximately in balance with the process heat requirements
in order to maintain a stable temperature. The range of temperature over
which power is adjusted is from 0% to 100%. This temperature range is
called the ‘Proportional Band’. The proportional band is adjustable for
differing process conditions (zero proportional band returns the controller to
basic on / off control).
The temperature difference between the stabilised temperature and the set
point is called the ‘Offset’. The offset can be reduced by adjusting the integral
term of the PID controller. This is achieved using the integrative action time
and integrative action reset.
A derivative function can be combined with the proportional controller to
provide the controller with the ability to shift the proportional band either up to
or down to compensate for rapidly changing temperature (i.e. when an oven
door is opened or cooler fluid is introduced into a controlled vessel). The
derivative function increases the controller gain during temperature changes,
and can help to reduce overshoot on start-up.
Hence, a three-mode PID controller combines the proportional, integral and
derivative actions, to allow the set point temperature to be approached
relatively smoothly with minimal overshoot.
7.4. Front Panel Controls
The MC810B controller has four front panel keys as described below.
7.4.1. The
key is used to increase the value of the parameter shown on
the display or to scroll through the parameter menu.
7.4.2. The
key is used to decrease the value of the parameter shown on
the display or to scroll through the parameter menu.
7.4.3. The
key is a dual function key. It is used to display and store the
value of the selected parameter when in ‘Programming’ mode. When used with
the
it is used to display the ‘Setpoint’ value.
7.4.4. The
is an ‘Exit / Stand-by button. Press of 3 seconds to turn unit on
or off.
7.5. Operating Modes.
7.5.1. The MB810B has two modes of operation: Function mode and Programming
mode. The unit enters Function mode immediately following power up in auto
test phase. In Function mode the display shows the temperature measured by
the temperature sensing probe. The output power will also be switched on or off
as appropriate. If the output power is on, the amber neon indicator on the front
panel will be illuminated. The only parameter which can be altered in the
function mode is the set-point. See 7.7.1
7.5.2. In Programming mode, all the other parameters apart from set-point can be
altered. To gain access to the programming mode from Function mode, press
the keys
and
. Keep them pressed for five seconds. The
output power is always off when in programming mode. If approximately 25
seconds elapse while in programming mode with out a key being pressed the
Page 12 of 24 M6493 Issue 10.3
7.3.3. Proportional, Integral and Derivative Control.
A proportional controller continuously adjusts the power, so the heat input to
the process is approximately in balance with the process heat requirements
in order to maintain a stable temperature. The range of temperature over
which power is adjusted is from 0% to 100%. This temperature range is
called the ‘Proportional Band’. The proportional band is adjustable for
differing process conditions (zero proportional band returns the controller to
basic on / off control).
The temperature difference between the stabilised temperature and the set
point is called the ‘Offset’. The offset can be reduced by adjusting the integral
term of the PID controller. This is achieved using the integrative action time
and integrative action reset.
A derivative function can be combined with the proportional controller to
provide the controller with the ability to shift the proportional band either up to
or down to compensate for rapidly changing temperature (i.e. when an oven
door is opened or cooler fluid is introduced into a controlled vessel). The
derivative function increases the controller gain during temperature changes,
and can help to reduce overshoot on start-up.
Hence, a three-mode PID controller combines the proportional, integral and
derivative actions, to allow the set point temperature to be approached
relatively smoothly with minimal overshoot.
7.4. Front Panel Controls
The MC810B controller has four front panel keys as described below.
7.4.1. The
key is used to increase the value of the parameter shown on
the display or to scroll through the parameter menu.
7.4.2. The
key is used to decrease the value of the parameter shown on
the display or to scroll through the parameter menu.
7.4.3. The
key is a dual function key. It is used to display and store the
value of the selected parameter when in ‘Programming’ mode. When used with
the
it is used to display the ‘Setpoint’ value.
7.4.4. The
is an ‘Exit / Stand-by button. Press of 3 seconds to turn unit on
or off.
7.5. Operating Modes.
7.5.1. The MB810B has two modes of operation: Function mode and Programming
mode. The unit enters Function mode immediately following power up in auto
test phase. In Function mode the display shows the temperature measured by
the temperature sensing probe. The output power will also be switched on or off
as appropriate. If the output power is on, the amber neon indicator on the front
panel will be illuminated. The only parameter which can be altered in the
function mode is the set-point. See 7.7.1
7.5.2. In Programming mode, all the other parameters apart from set-point can be
altered. To gain access to the programming mode from Function mode, press
the keys
and
. Keep them pressed for five seconds. The
output power is always off when in programming mode. If approximately 25
seconds elapse while in programming mode with out a key being pressed the
Page 12 of 24 M6493 Issue 10.3
7.3.3. Proportional, Integral and Derivative Control.
A proportional controller continuously adjusts the power, so the heat input to
the process is approximately in balance with the process heat requirements
in order to maintain a stable temperature. The range of temperature over
which power is adjusted is from 0% to 100%. This temperature range is
called the ‘Proportional Band’. The proportional band is adjustable for
differing process conditions (zero proportional band returns the controller to
basic on / off control).
The temperature difference between the stabilised temperature and the set
point is called the ‘Offset’. The offset can be reduced by adjusting the integral
term of the PID controller. This is achieved using the integrative action time
and integrative action reset.
A derivative function can be combined with the proportional controller to
provide the controller with the ability to shift the proportional band either up to
or down to compensate for rapidly changing temperature (i.e. when an oven
door is opened or cooler fluid is introduced into a controlled vessel). The
derivative function increases the controller gain during temperature changes,
and can help to reduce overshoot on start-up.
Hence, a three-mode PID controller combines the proportional, integral and
derivative actions, to allow the set point temperature to be approached
relatively smoothly with minimal overshoot.
7.4. Front Panel Controls
The MC810B controller has four front panel keys as described below.
7.4.1. The
key is used to increase the value of the parameter shown on
the display or to scroll through the parameter menu.
7.4.2. The
key is used to decrease the value of the parameter shown on
the display or to scroll through the parameter menu.
7.4.3. The
key is a dual function key. It is used to display and store the
value of the selected parameter when in ‘Programming’ mode. When used with
the
it is used to display the ‘Setpoint’ value.
7.4.4. The
is an ‘Exit / Stand-by button. Press of 3 seconds to turn unit on
or off.
7.5. Operating Modes.
7.5.1. The MB810B has two modes of operation: Function mode and Programming
mode. The unit enters Function mode immediately following power up in auto
test phase. In Function mode the display shows the temperature measured by
the temperature sensing probe. The output power will also be switched on or off
as appropriate. If the output power is on, the amber neon indicator on the front
panel will be illuminated. The only parameter which can be altered in the
function mode is the set-point. See 7.7.1
7.5.2. In Programming mode, all the other parameters apart from set-point can be
altered. To gain access to the programming mode from Function mode, press
the keys
and
. Keep them pressed for five seconds. The
output power is always off when in programming mode. If approximately 25
seconds elapse while in programming mode with out a key being pressed the
Page 12 of 24 M6493 Issue 10.3
7.3.3. Proportional, Integral and Derivative Control.
A proportional controller continuously adjusts the power, so the heat input to
the process is approximately in balance with the process heat requirements
in order to maintain a stable temperature. The range of temperature over
which power is adjusted is from 0% to 100%. This temperature range is
called the ‘Proportional Band’. The proportional band is adjustable for
differing process conditions (zero proportional band returns the controller to
basic on / off control).
The temperature difference between the stabilised temperature and the set
point is called the ‘Offset’. The offset can be reduced by adjusting the integral
term of the PID controller. This is achieved using the integrative action time
and integrative action reset.
A derivative function can be combined with the proportional controller to
provide the controller with the ability to shift the proportional band either up to
or down to compensate for rapidly changing temperature (i.e. when an oven
door is opened or cooler fluid is introduced into a controlled vessel). The
derivative function increases the controller gain during temperature changes,
and can help to reduce overshoot on start-up.
Hence, a three-mode PID controller combines the proportional, integral and
derivative actions, to allow the set point temperature to be approached
relatively smoothly with minimal overshoot.
7.4. Front Panel Controls
The MC810B controller has four front panel keys as described below.
7.4.1. The
key is used to increase the value of the parameter shown on
the display or to scroll through the parameter menu.
7.4.2. The
key is used to decrease the value of the parameter shown on
the display or to scroll through the parameter menu.
7.4.3. The
key is a dual function key. It is used to display and store the
value of the selected parameter when in ‘Programming’ mode. When used with
the
it is used to display the ‘Setpoint’ value.
7.4.4. The
is an ‘Exit / Stand-by button. Press of 3 seconds to turn unit on
or off.
7.5. Operating Modes.
7.5.1. The MB810B has two modes of operation: Function mode and Programming
mode. The unit enters Function mode immediately following power up in auto
test phase. In Function mode the display shows the temperature measured by
the temperature sensing probe. The output power will also be switched on or off
as appropriate. If the output power is on, the amber neon indicator on the front
panel will be illuminated. The only parameter which can be altered in the
function mode is the set-point. See 7.7.1
7.5.2. In Programming mode, all the other parameters apart from set-point can be
altered. To gain access to the programming mode from Function mode, press
the keys
and
. Keep them pressed for five seconds. The
output power is always off when in programming mode. If approximately 25
seconds elapse while in programming mode with out a key being pressed the