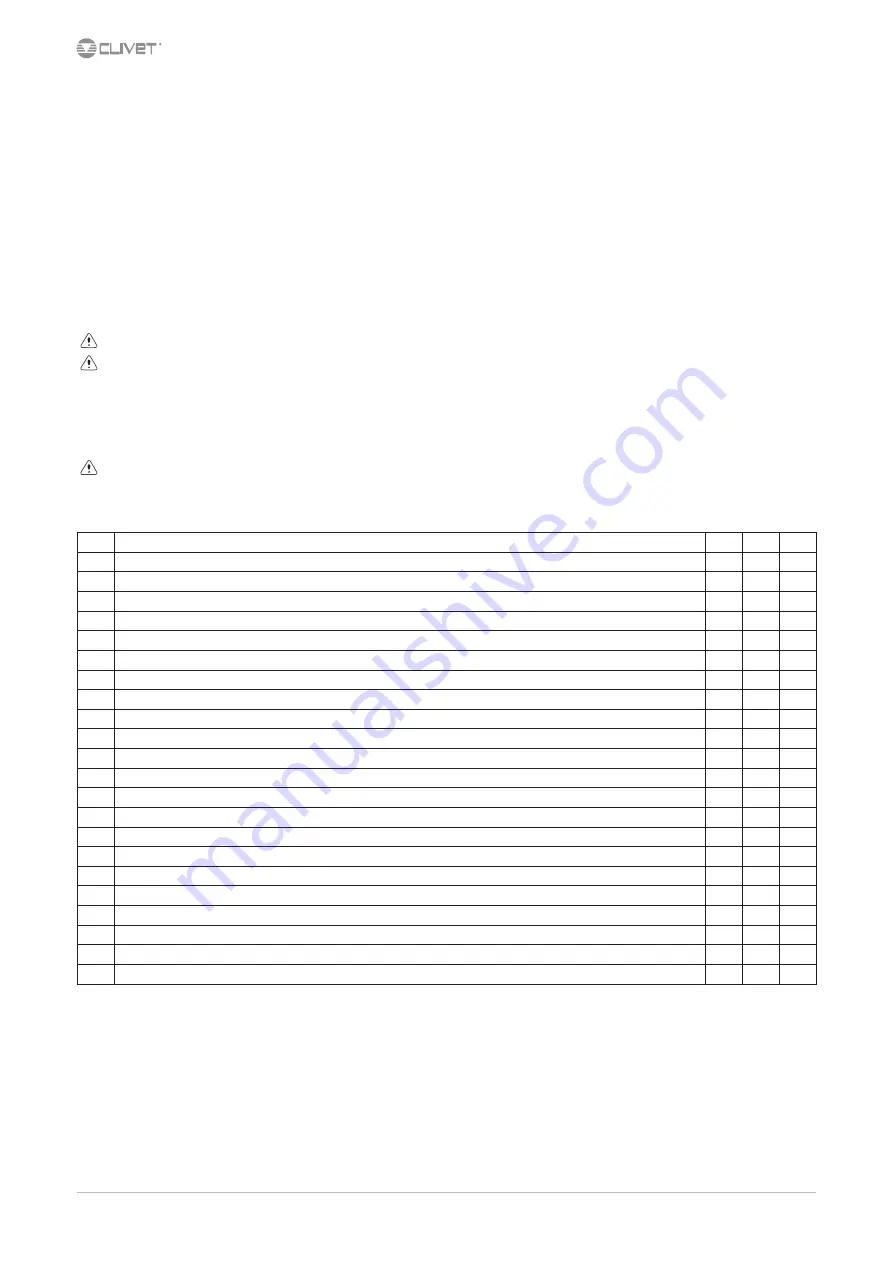
40
WSAN-XSC3 90.4-240.4
8 Maintenance
8.1 General description
Maintenance must be done by authorized centres or by qualified personnel.
The maintenance allows to:
•
maintain the unit efficiency
•
increase the life span of the equipment
•
assemble information and data to understand the state of the unit efficiency and avoid possible damages
Before checking, please verify the following:
•
the electrical power supply line should be isolated at the beginning
•
the unit isolator is open, locked and equipped with the suitable warning
•
make sure no tension is present
After turning off the power, wait at least 5 minutes before accessing to the electrical panel or any other electrical component.
Before accessing check with a multimeter that there are no residual stresses.
8.2 Inspections frequency
Perform an inspection every 6 months minimum.
The frequency, however, depends on the use.
In the event of frequent use it is recommended to plan inspections at shorter intervals:
•
frequent use (continuous or very intermittent use, near the operating limits, etc)
•
critical use (service necessary)
√
intervention frequency (months)
1
6
12
1
presence corrosion
X
2
panel fixing
X
3
fan fixing
X
4
coil cleaning
X
5
water filter cleaning
X
6
water: quality, ph, weight of glycol (%)
X
7
check the exchanger efficiency
X
8
circulating pumps
X
9
check of the fixing and the insulation of the power lead
X
10
check of the earthing cable
X
11
electric panel cleaning
X
12
capacity contactor status
X
13
termina closing, cable insulation integrity
X
14
voltage and phase unbalancing (no load and on-load)
X
15
absorptions of the single electrical loads
X
16
test of the compressor crankcase heaters
X
17
Checking for leaks
*
18
survey of the refrigerant circuit operating parameters
X
19
safety valve
*
20
protective device test: pressure switches, thermostats, flow switches etc..
X
21
control system test: setpoint, climatic compensations, capacity stepping, water / air flow-rate variations
X
22
control device test: alarm signalling, thermometers, probes, pressure gauges etc..
X
* Refer to the local regulations; and ensure correct adherance. Companies and technicians that effect interventions of installation, maintenance/re-
pairs, leak control and recovery must be CERTIFIED as expected by the local regulations. The leak control must be effected with annual renewal.
Содержание WSAN-XSC3 100.4
Страница 44: ...44 WSAN XSC3 90 4 240 4 8 17 Compressor replacement ...
Страница 45: ...WSAN XSC3 90 4 240 4 45 8 18 Exchanger replacement ...
Страница 47: ...WSAN XSC3 90 4 240 4 47 ...
Страница 48: ...48 WSAN XSC3 90 4 240 4 ...
Страница 49: ...WSAN XSC3 90 4 240 4 49 ...
Страница 63: ...Page intentionally left blank ...