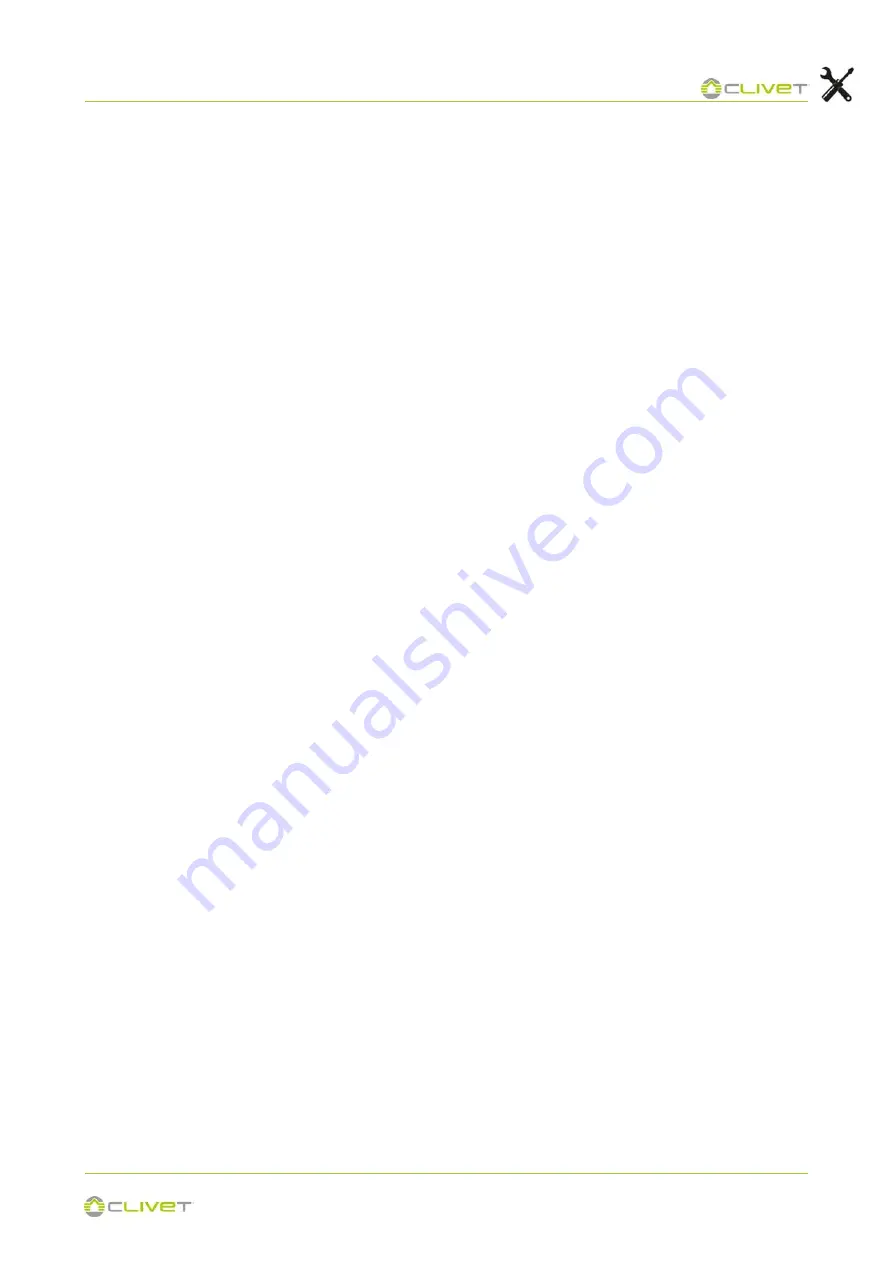
55
9 - MAINTENANCE
Ventilation must be maintained during operations.
Ventilation must disperse the released refrigerant
safely, preferably outdoors in the atmosphere.
Cooling equipment checks
Should a replacement be necessary, the new
components installed must be suitable for the
purpose envisaged and compliant with
specifications.
Always follow the manufacturer guidelines on
maintenance and assistance. In case of doubt,
contact the manufacturer technical office for
assistance.
The following checks must be preformed on
systems containing flammable refrigerants:
•
the quantity of the charge must comply with the
size of the room where the parts containing
refrigerant are installed;
•
the machine and ventilation intake function
correctly and are not obstructed;
•
If an indirect cooling circuit is used, the
secondary circuits must be checked to verify the
presence of refrigerants; the marking on the
equipment remains visible and readable;
•
Make sure markings and symbols are always
readable; cooling pipes or components must be
installed in a position that makes improbable
their exposure to substances that may corrode
the components containing refrigerant, unless
they are manufactured with material intrinsically
resistant to corrosion or suitably protected
against corrosion.
Electrical device checks
The reparation and maintenance of electric
components must include initial safety checks and
component inspection procedures.
In case of a fault that compromises safety, do not
perform any electrical connection to the circuit until
said fault is suitably resolved.
If it is not possible to repair the fault immediately
and electrical components need to remain
functioning, a temporary solution must be adopted.
This must be reported to the owner of the
equipment so as to keep all parties informed.
Initial safety checks must include:
•
that condensers are emptied. This operation
must be performed safely to avoid any sparks:
•
that electrical components and wiring are not
exposed during the charging, recovering or
venting phases;
•
That the earth conductor is continuous.
Area checks
Before working on systems containing flammable
refrigerants, perform safety checks to reduce the
risk of combustion to the minimum. Before
performing any reparation operations on the cooling
system, comply with the following warnings.
Work procedures
Operations must be performed following a
controlled procedure so as to reduce the risk of
flammable gases or vapours developing.
General work area
All the personnel in charge with maintenance
operations and other operators working in the local
area must be instructed and monitored as regards
the nature of the intervention.
Avoid working in tight spaces. The area surrounding
the working space must be cordoned off. Make sure
the area is secured by monitoring the flammable
material.
Check the presence of refrigerant
Both before and during operations, the area must
be monitored with a dedicated refrigerant detector
to make sure the technician is aware of the
presence of potentially-flammable environments.
Make sure the leak detection equipment is suitable
for use with flammable refrigerants and therefore
without sparks, suitably sealed or intrinsically safe.
Presence of the fire extinguisher
If hot interventions are not performed on cooling
equipment or connected components, suitable fire
fighting equipment must be kept at hand.
Keep a dry-powder or CO2 extinguisher near the
loading area.
No ignition source
It is absolutely forbidden to use ignition sources
that may lead to fire or explosion during operations
on the cooling system or on pipes that contain or
have contained flammable refrigerant.
All possible ignition sources, including cigarettes,
must be kept sufficiently away from the installation,
reparation, removal and disposal site as flammable
refrigerant may be released in the surrounding area.
Before starting operations, the area surrounding the
equipment must be inspected to guarantee the
absence of flammables or combustion risks.
“SMOKING IS FORBIDDEN” signs must be affixed.
Ventilated area
Before intervening on the system or performing any
hot intervention, make sure to be in an outdoor or
suitably ventilated area.
SAFETY WARNINGS FOR OPERATIONS ON UNITS CONTAINING R32
Содержание ELFOFresh EVO CPAN-YIN
Страница 1: ...Change living home MANUAL FOR INSTALLATION USE AND MAINTENANCE ELFOFresh EVO CPAN YIN Size2...
Страница 69: ...69 12 TECHNICAL DATE ELFOAir...
Страница 72: ...Filter Filter only on the intake grille ELFOFresh EVO ELFOPack ELFOFresh EVO ELFOPack...
Страница 73: ...Cover the plenum openings grilles with cardboard adhesive tape etc Remove caps...
Страница 74: ...74 NOTE...
Страница 75: ...75 NOTE...