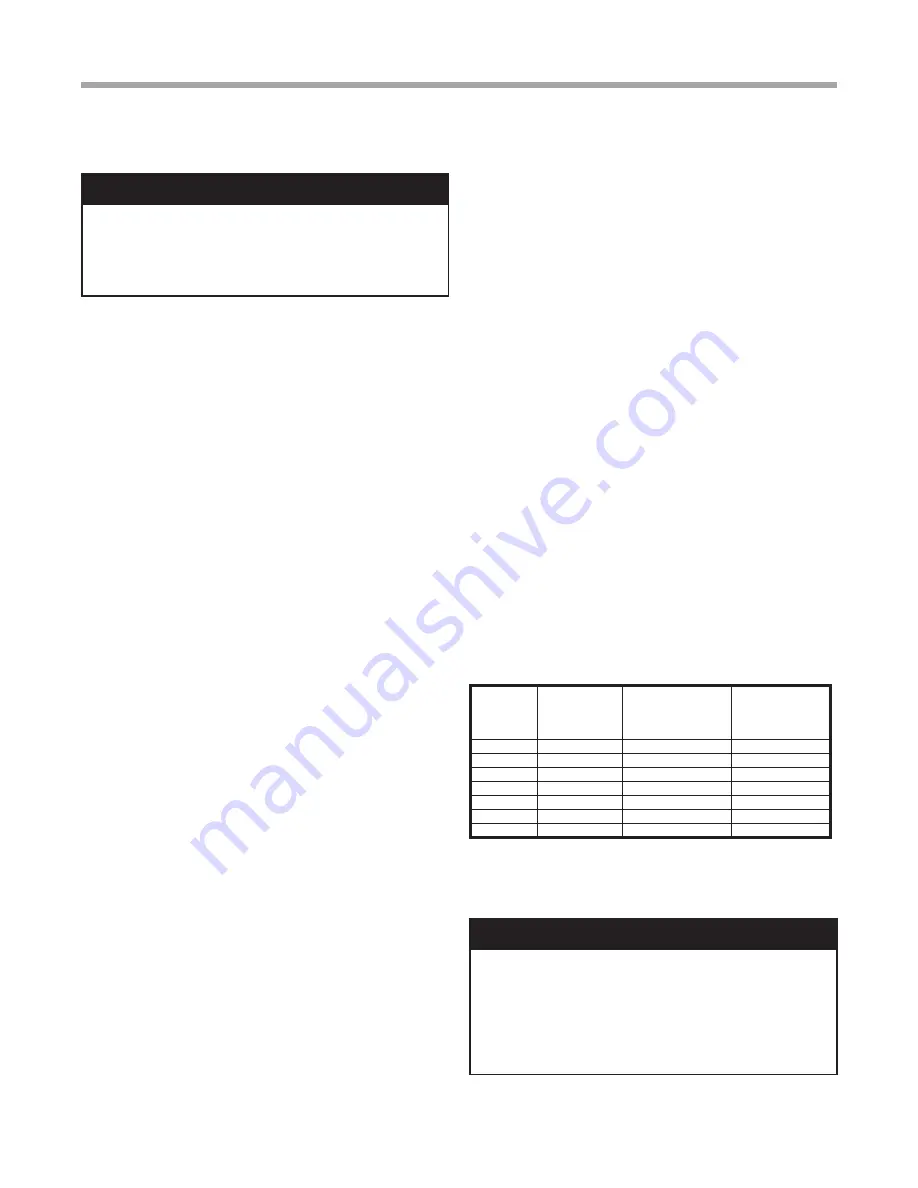
31
c l i m a t e m a s t e r.c o m
Tranquility
®
30 Digital (TE) Series IOM - 60Hz HFC-410A
R e v. : O c t o b e r 5 , 2 0 2 1
The heat pump, water piping, pump, and hot water tank
should be located where the ambient temperature does
not fall below 50°F [10°C]. Keep water piping lengths at a
minimum. DO NOT use a one way length greater than 50 ft.
(one way) [15 m]. See Table 6 for recommended piping sizes
and maximum lengths.
All installations must be in accordance with local codes. The
installer is responsible for knowing the local requirements,
and for performing the installation accordingly. DO NOT
activate the HWG (turn DIP 3-4 to the ON position) until
“Initial Start-Up” section, below is completed. Powering the
pump before all installation steps are completed will damage
the pump.
Water Tank Preparation
1. Turn off power or fuel supply to the hot water tank.
2. Connect a hose to the drain valve on the water tank.
3. Shut off the cold water supply to the water tank.
4. Open the drain valve and open the pressure relief valve
or a hot water faucet to drain tank.
5. When using an existing tank, it should be flushed with
cold water after it is drained until the water leaving the
drain hose is clear and free of sediment.
6. Close all valves and remove the drain hose.
7. Install HWG water piping.
HWG Water Piping
1. Using at least 1/2” [12.7mm] I.D. copper, route and install
the water piping and valves as shown in Figures 21 or
22. Install an approved anti-scald valve if the 150°F HWG
setpoint is or will be selected. An appropriate method
must be employed to purge air from the HWG piping.
This may be accomplished by flushing water through the
HWG (as in Figures 21 and 22) or by installing an air vent
at the high point of the HWG piping system.
2. Insulate all HWG water piping with no less than 3/8”
[10mm] wall closed cell insulation.
3. Open both shut off valves and make sure the tank drain
valve is closed.
Water Tank Refill
1. Close valve #4. Ensure that the HWG valves (valves #2
and #3) are open. Open the cold water supply (valve #1)
to fill the tank through the HWG piping. This will force
water flow through the HWG and purge air from the HWG
piping.
2. Open a hot water faucet to vent air from the system until
water flows from faucet; turn off faucet. Open valve #4.
3. Depress the hot water tank pressure relief valve handle to
ensure that there is no air remaining in the tank.
4. Inspect all work for leaks.
5. Before restoring power or fuel supply to the water heater,
adjust the temperature setting on the tank thermostat(s)
to insure maximum utilization of the heat available from
the refrigeration system and conserve the most energy.
On tanks with both upper and lower elements and
thermostats, the lower element should be turned down
to 100°F [38°C] or the lowest setting; the upper element
should be adjusted to 120-130°F [49-54°C]. Depending
upon the specific needs of the customer, you may want
to adjust the upper element differently. On tanks with a
single thermostat, a preheat tank should be used (Fig 21).
6. Replace access cover(s) and restore power or
fuel supply.
Initial Start-Up
1. Make sure all valves in the HWG water circuit are
fully open.
2. Turn on the heat pump and allow it to run for
10-15 minutes.
3. Set S3-4 to the “ON” position (enabled) to engage the
HWG. See Figure 24.
4. The HWG pump should not run if the compressor is not
running.
5. The temperature difference between the water entering
and leaving the HWG coil should be approximately
5-10°F [3-6°C].
6. Allow the unit to operate for 20 to 30 minutes to insure
that it is functioning properly.
Hot Water Generator
Table 6: HWG Water Piping Sizes and Length
⚠
WARNING!
⚠
WARNING!
The HWG pump Is fully wired from the
factory. Use extreme caution when working around
the microprocessor control as it contains line voltage
connections that presents a shock hazard that can cause
severe injury or death!
Unit
Nominal
Tonnage
Nominal
HWG Flow
(gpm)
1/2" Copper
(max length*)
3/4" Copper
(max length*)
2.0
0.8
50
-
2.5
1.0
50
-
3.0
1.2
50
-
3.5
1.4
50
-
4.0
1.6
45
50
5.0
2.0
25
50
6.0
2.4
10
50
*Maximum length is equivalent length (in feet) one way of type L copper.
⚠
CAUTION!
⚠
CAUTION!
Use only copper piping for HWG piping due to
the potential of high water temperatures for water that has
been in the HWG heat exchanger during periods of no-flow
conditions (HWG pump not energized). Piping other than
copper may rupture due to high water temperature and
potable water pressure. CPVC, PEX, or other plastic pipe
should not be used HWG piping