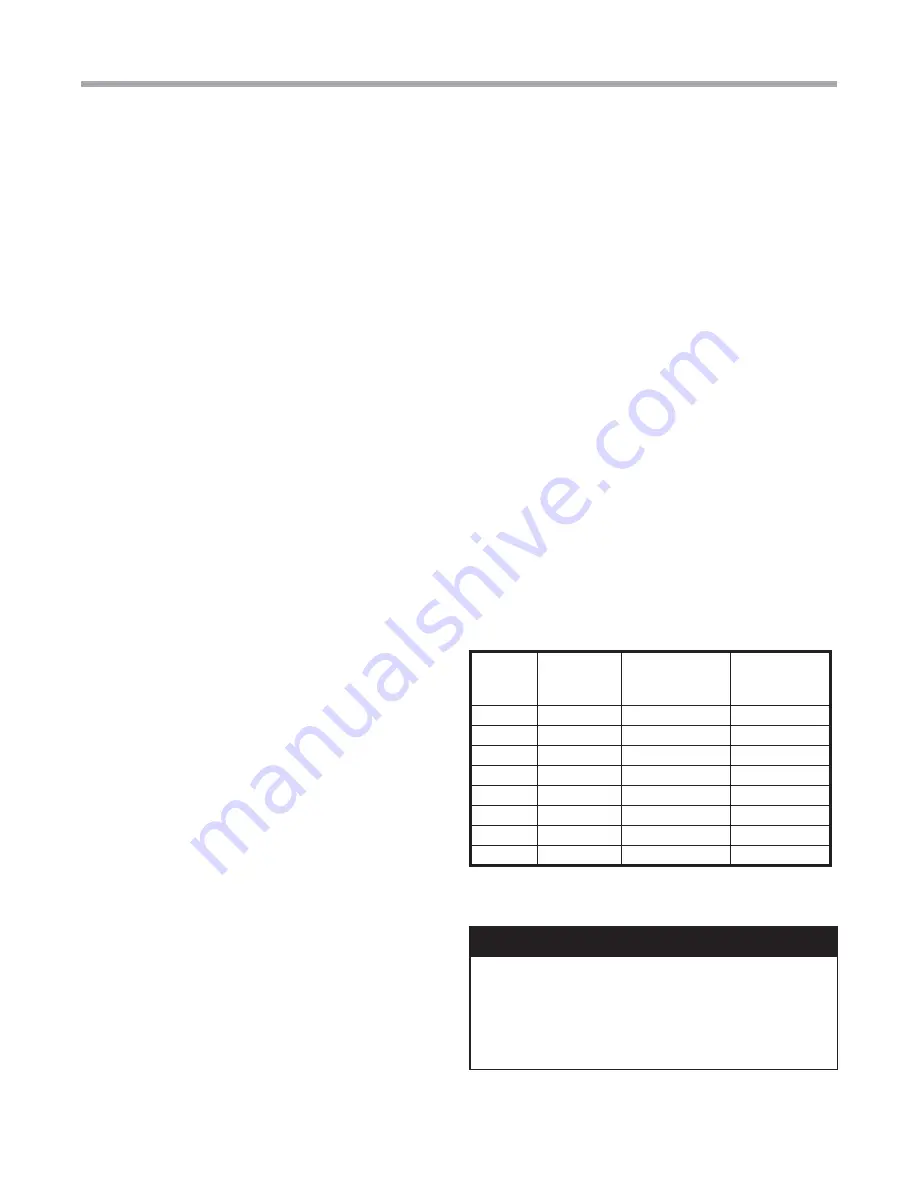
9
R e m o t e H W G
R e v i s e d : M a rc h 1 2 , 2 0 1 9
c l i m a t e m a s t e r. c o m
Hot Water Generator Module - Domestic Water Installation
Table 2: HWG Water Piping Size and Length
Unit
Nominal
Tonnage
Nominal
HWG Flow
(gpm)
1/2" Copper
(max length*)
3/4" Copper
(max length*)
1.5
0.6
50
-
2.0
0.8
50
-
2.5
1.0
50
-
3.0
1.2
50
-
3.5
1.4
50
-
4.0
1.6
45
50
5.0
2.0
25
50
6.0
2.4
10
50
*Maximum length is equivalent length (in feet) one way of type L
copper.
CAUTION!
CAUTION!
Use only copper piping for HWG piping due to
the potential of high water temperatures for water that has
been in the HWG heat exchanger during periods of no-
fl
ow
conditions (HWG pump not energized). Piping other than
copper may rupture due to high water temperature and
potable water pressure.
Warning! The HWG pump Is fully wired from the
factory. Use extreme caution when working around
the microprocessor control as it contains line voltage
connections that presents a shock hazard that can
cause severe injury or death!
The heat pump, water piping, pump, and hot water tank
should be located where the ambient temperature does
not fall below 50°F [10°C]. Keep water piping lengths at a
minimum. DO NOT use a one way length greater than 50 ft.
(one way) [15 m]. See Table 2 for recommended piping sizes
and maximum lengths.
All installations must be in accordance with local codes. The
installer is responsible for knowing the local requirements,
and for performing the installation accordingly. DO NOT
energize the pump until “water tank re
fi
ll” section, below is
completed. Powering the pump before all installation steps
are completed may damage the pump.
Water Tank Preparation
1. Turn
o
ff
power or fuel supply to the hot water tank.
2. Connect a hose to the drain valve on the water tank.
3. Shut
o
ff
the cold water supply to the water tank.
4. Open the drain valve and open the pressure relief valve
or a hot water faucet to drain tank.
5. When using an existing tank, it should be
fl
ushed with
cold water after it is drained until the water leaving the
drain hose is clear and free of sediment.
6. Close all valves and remove the drain hose.
7. Install HWG water piping.
HWG Water Piping
1. Using at least 5/8” [16mm] O.D. copper, route and install
the water piping and valves as shown in Figures 1 or 2.
Install an approved anti-scald valve if the 150°F HWG
setpoint is or will be selected. An appropriate method
must be employed to purge air from the HWG piping.
This may be accomplished by
fl
ushing water through the
HWG (as In Figures 1 and 2) or by Installing an air vent at
the high point of the HWG piping system.
2. Insulate all HWG water piping with no less than 3/8”
[10mm] wall closed cell insulation.
3. Open both shut o
ff
valves and make sure the tank drain
valve is closed.
Water Tank Refi ll
1. Close valve #4. Ensure that the HWG valves (valves #2
and #3) are open. Open the cold water supply (valve #1)
to
fi
ll the tank through the HWG piping. This will purge air
from the HWG piping.
2. Open a hot water faucet to vent air from the system until
water
fl
ows from faucet; turn o
ff
faucet. Open valve #4.
3. Depress the hot water tank pressure relief valve handle to
ensure that there is no air remaining in the tank.
4. Inspect all work for leaks.
5. Before restoring power or fuel supply to the water heater,
adjust the temperature setting on the tank thermostat(s)
to insure maximum utilization of the heat available from
the refrigeration system and conserve the most energy.
On tanks with both upper and lower elements and
thermostats, the lower element should be turned down
to 100°F [38°C] or the lowest setting; the upper element
should be adjusted to 120-130°F [49-54°C]. Depending
upon the speci
fi
c needs of the customer, you may want
to adjust the upper element di
ff
erently. On tanks with a
single thermostat, a preheat tank should be used (Fig 2).
6. Replace access cover(s) and restore power or
fuel supply.
Initial Start-Up
1. Make sure all valves in the HWG water circuit are fully
open.
2. Turn the heat pump power and remote HWG power “o
ff
”
and switch dip switch DIP 3.4 on the HWG controller to
the “o
ff
” (enabled) position to activate the HWG.
3. The HWG pump should not run if the compressor is not
running.
4. The temperature di
ff
erence between the water entering
and leaving the HWG should be approximately 5-10
°
F
[3-6
°
C].
5. Allow the unit to operate for 20 to 30 minutes insure that
it is functioning properly.
6. Always turn dip switch DIP 3.4 on the HWG controller to
the “on” (disabled) position to deactivate the HWG when
servicing the outdoor compressor section.
Содержание AHWG
Страница 2: ...This page was intentionally left blank...