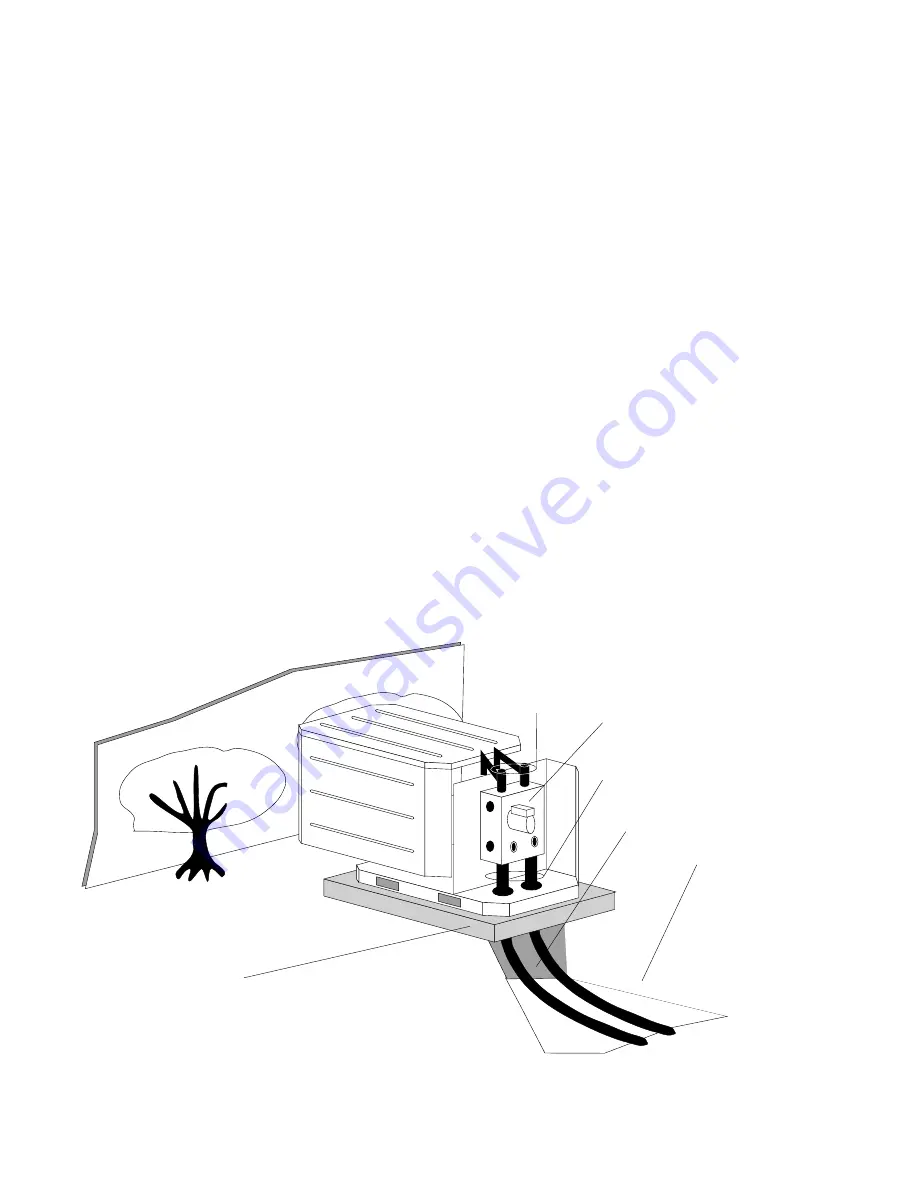
Page 8
Fill loop with water from a garden hose through flush
cart before using flush cart pump to ensure an even fill.
Once full, do not allow the water level in the flush cart
tank to drop below the pump inlet line or air can be
pumped back out to the earth loop. Maintain a fluid level
in the tank above the return tee so that air can not be
continuously mixed back into the fluid. 50 psi surges can
be used to help purge air pockets by simply shutting off
the return valve going into the flush cart reservoir. This
‘dead heads’ the pump to 50 psi To dead head the pump
until maximum pumping pressure is reached, open the
valve back up and a pressure surge will be sent through
the loop to help purge air pockets from the piping
system. Notice the drop in fluid level in the flush cart
tank.
If air is purged from the system, the level will
drop only 1-2 inches in a 10" diameter PVC flush
tank (about a half gallon) since liquids are
incompressible
. If the level drops more than this,
flushing should continue since air is still being
compressed in the loop fluid. Do this a number of times.
When the fluid level is dropping less than 1-2" in a 10"
diameter tank the flow can be reversed. Finally the dead
head test should be checked again for an indication of air
in the loop.
This fluid level drop is your only
indication of air in the loop.
Antifreeze may be added
before, during or after the flushing procedure. However,
depending upon which time is chosen, antifreeze could
be wasted when emptying the flush cart tank. Loop static
pressure will fluctuate with the seasons. Pressures will be
higher in the winter months than during the cooling
season. This fluctuation is normal and should be
considered when charging the system initially. Pressurize
the loop to a static pressure of 40-50 psi (winter) 15-20
psi (summer).
After pressurization, be sure to remove the plug in the
end of the Grundfos loop pump motor(s) to allow trapped
air to be discharged and to insure the motor housing has
been flooded. This is not required for Taco circulators.
Insure the loop flow center provides adequate flow
through the unit by checking pressure drop across the
heat exchanger and comparing it to the figures shown in
Table 13.
ANTIFREEZE
- In areas where minimum entering loop
temperatures drop below 40
°
F or where piping will be
routed through areas subject to freezing, anti-freeze is
needed. Alcohols and glycols are commonly used as
antifreezes, however your local territory manager should
be consulted for the antifreeze best suited to your area.
Freeze protection should be maintained to 15
°
F below
the lowest expected entering loop temperature.
If unit is
located outdoors freeze protection should be
maintained to 25
°
F below the lowest expected
entering loop temperature.
Consult the Flow Controller
Installation Manual for further details.
FREEZE PROTECTION
- When an antifreeze is
selected the freeze protection setpoint should be switched
to the lower setting to avoid nuisance faults. Consult
'freeze protection' in the controls section for more
information.
Figure 5. Typical Earth Loop Connection
Paradigm
Condensing
Unit
Air Pad with
access hole
Header Pit
Backfill carefully to avoid
stress on piping and flow
controller connection
P/T Ports
Insulate all piping with 1/2”
closed cell insulation
Flow Controller
Содержание 38 WQ-S018SSC301
Страница 17: ...Page 17 Paradigm 18 60 230 60 1 Wiring Diagram Part 69828103 Rev C 8 19 99 GT S 18 60 ...
Страница 29: ...Page 29 MAINTENANCE NOTES ...
Страница 30: ......