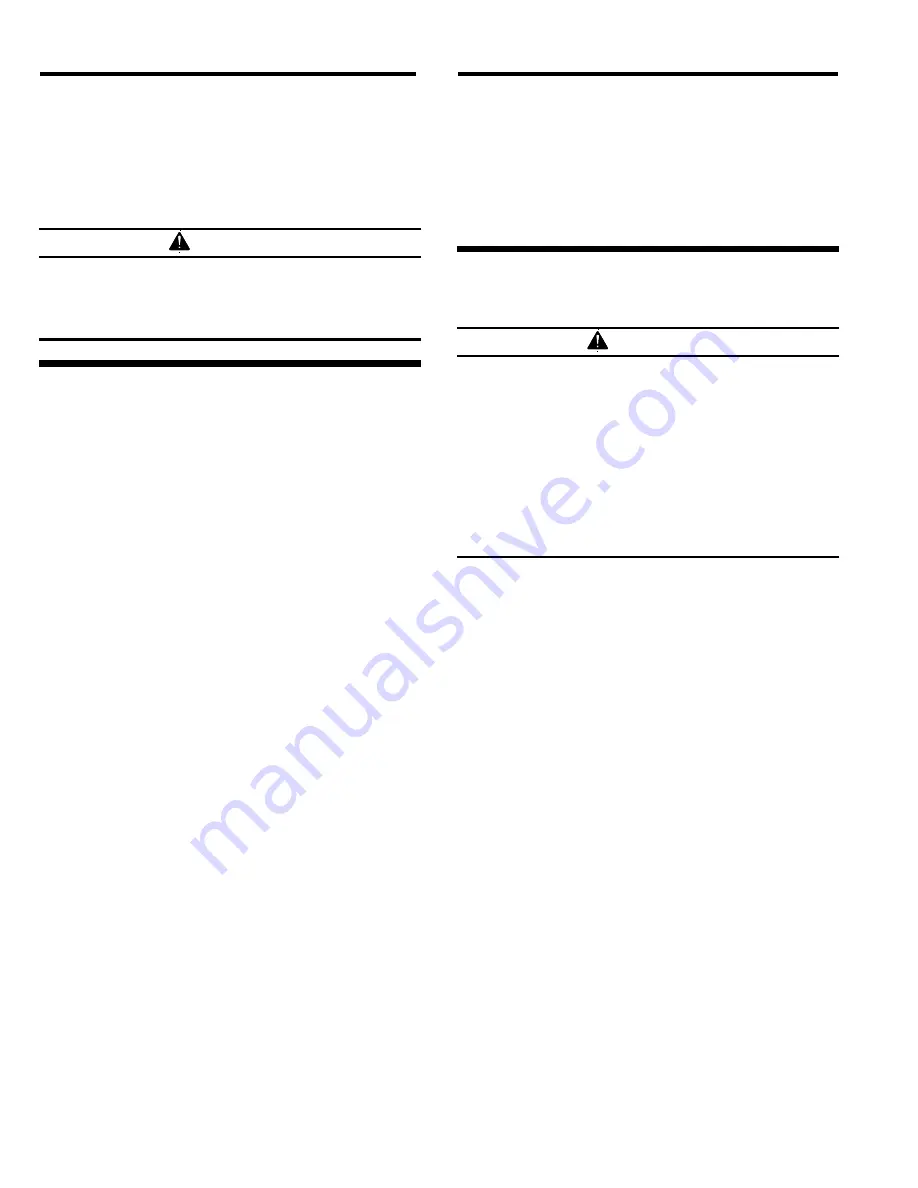
SENTINEL MEDIA METERING VALVE
Page 4
2.8.2.6
If a pressure regulator is used, control air for the
Sentinel should be sourced up-stream of the regulator.
Doing so allows full line pressure to control the valve
while blasting pressure can be adjusted down to
approximately 30 psi. The Sentinel valve requires control
line pressure to be between 62 psi and 150 psi.
NOTE: The ACS performs dual functions: Use it to clear
abrasive from the blast hose and to blow off abrasive
from the blasted surface at the blasting area. Small
amounts of abrasive may come out the nozzle with the
air. Residual abrasive may remain that will have to be
removed outside the blast area prior to painting.
Excessive compressed air pressure could
cause a blast machine to rupture. To prevent
serious injury or death, do not exceed the rated
pressure of the blast machine vessel.
WARNING
4.0 MAINTENANCE
3.0 OPERATION
3.1
When the valve is correctly installed, it opens and
closes pneumatically as control-air is applied or removed
from the valves actuating piston. If the valve is used in
conjunction with the remote control system, it opens
when the remote controls begin the blasting process,
and closes when the controls stop the blasting process.
If the valve is used independently of remote controls, it
opens and closes with the use of the ACS valve.
3.2 Abrasive
Metering:
Abrasive will not flow
through the valve unless it is open (see Paragraph 3.1)
Abrasive flow is adjusted at the metering handle. The
valve is closed when the handle is fully right. To adjust,
close the valve and slowly move the handle to the left to
increase flow. Use as little abrasive as possible while
maintaining the best cleaning rate. Generally, with the
correct mixture, abrasive can be seen as light
discoloration as it exits the nozzle. The valve is fully
open when the handle is fully left.
3.3
Operation of the Abrasive Cut-Off Switch.
3.3.1
The ACS valve is “OFF” (no abrasive) when the
toggle is toward the nozzle ("EXH" port) or down if
installed on the Sentinel valve as shown in Figure 2.
Abrasive flow is “ON” when the toggle is pointing back
away from the nozzle ("CYL" port) (up if it is as shown in
Figure 2).
3.3.2
By moving the switch to the “OFF” position, the
air supply to the abrasive metering valve is cut off,
closing the valve and stopping the abrasive flow. This
allows the operator to have air alone coming from the
nozzle, which can be used to clear the blast hose before
shut-down, and to blow abrasive off the blasted surface.
The switch can be opened or closed any time but will not
activate the metering valve unless the control handle is
pressed.
Failure to observe the following procedures
before performing any maintenance on a blast
machine could cause serious injury or death
from the sudden release of trapped compressed
air.
WARNING
•
Depressurize the blast machine.
•
Lock out and tag out the compressed air
supply.
•
Bleed the air supply line to the blast
machine.
NOTE: The following instructions are for servicing a
valve that has been removed from the blast machine.
The easiest way to remove the valve, is to remove the 4
bolts holding the flanged adaptor to the valve assembly
and disconnecting the pusher line. The valve and lower
piping can then be removed as an assembly. The
flanged adaptor will remain on the machine, but should
be inspected for wear. If it has been determined that
service is required only in the upper portion of the valve
(shut-off section), the upper valve section can be
removed as a unit as follows:
Attach a small air line to the upper body cylinder port to
retract the shut-off piston. Remove the 4 flanged adaptor
bolts and the bolts and studs holding the lower body
assembly to the upper body assembly. The upper body
assembly may then be removed without removing any of
the blast machine plumbing. Depressurize the air line
once the assembly has been removed.
4.1
Removing Upper Body Assembly (shut-off
section).
4.1.1
Remove nuts and cap screws holding the upper
body onto the flanged adaptor.
4.1.2
Attach an air line to the fitting on the cylinder
port on the upper body assembly, and pressurize the
line to retract the shut-off piston.